How formwork technology has evolved in India
By Edit Team | April 13, 2018 11:28 am SHARE
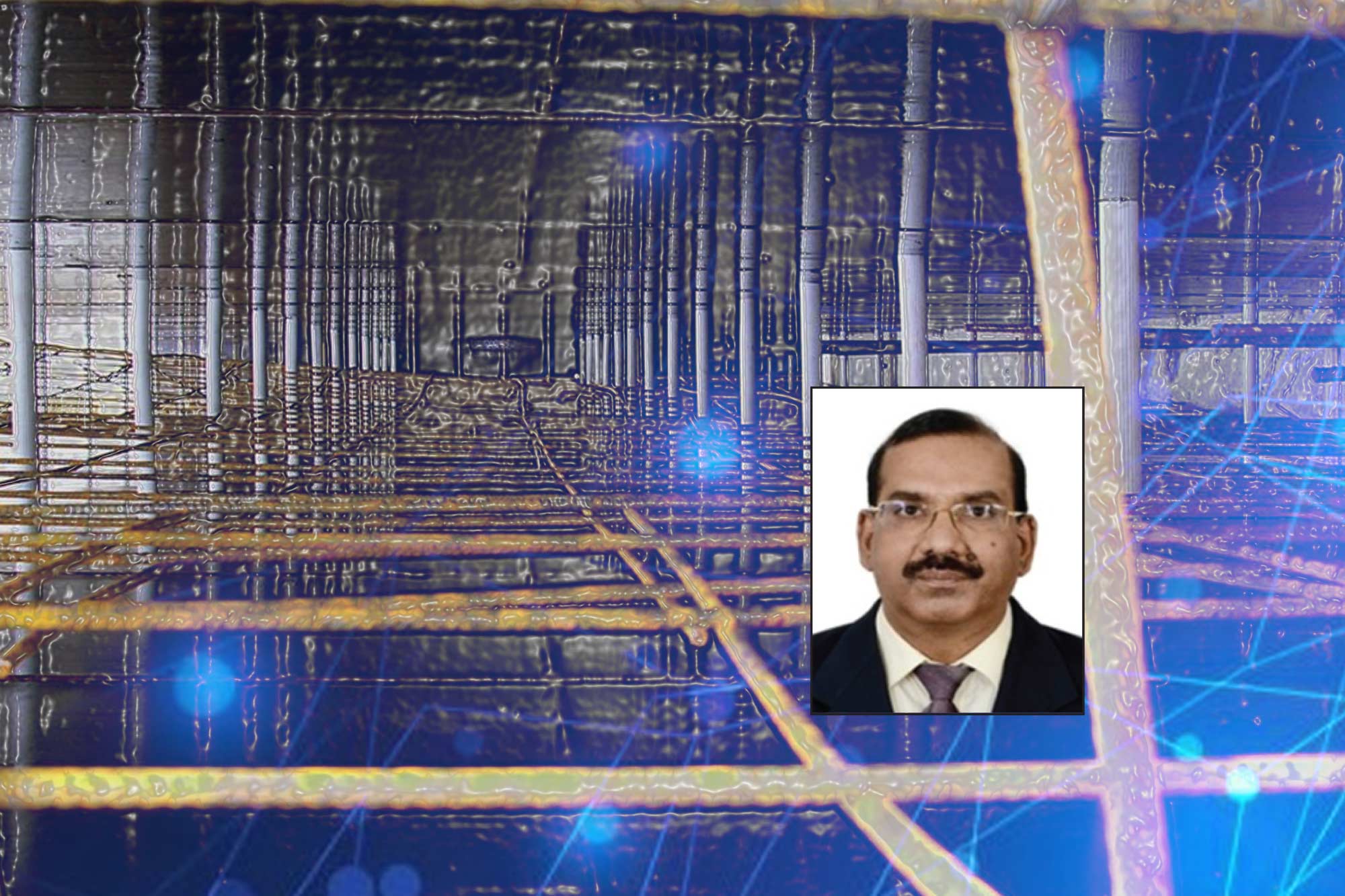
In last one or one and half decade we have seen many high-rise buildings coming up, otherwise India known for traditional 5 to 10 storey building in urban areas and one or two floors in other parts. The unprecedented development in urban areas and scarcity of land forced emerging of high rise buildings of 50 floors and above.
The high-rise buildings also bought new construction technologies for faster and safer construction. Entry of international construction firms in Indian construction space also helped in emergence of global proven practices.
High-rise buildings are rapidly becoming a developing nature of urban zones due to increased population and businesses. The core of high-rise buildings is one of the most important elements in such gigantic structures. Fast and efficient construction of the concrete core of a high-rise building is essential to maintain phased progress on other parts of the building. Formwork is one of the most important factors in determining the success of a construction project in terms of speed, quality cost and safety of work.
In high-rise building construction the most efficient way to speed up the work is by achieving a very short floor cycle. That directly depends on the selected form work type for the construction.
Formwork companies are making all efforts to innovate new systems for better and quicker results. Taking cue from the developed world, Indian construction industry has started using some of the world class technologies. Several formwork systems are in use at different places in the world; eventually the systems which are reasonably economical and easy for operation with skilled labour are more useful in India. Leading players in this industry are Doka, Mascon System, MFE Formwork Technology (Mivan), Meva, Waco, Forming Access and Support, Inc (FASI), Peri, BSL Scaffolding, Uday Structurals & Engineers, Paschal etc.,
Climbing formwork is a special type of formwork for large vertical concrete structures. Climbing formworks will represent an effective solution for structures that require seamless walls, or their form is very repetitive.
There are several types of climbing formwork, depending on the type of building being built. They can move on their own, using hydraulic or electric jacks, commonly known as ‘self-climbing formwork’, or they can be relocated with cranes and other equipment.
There is also a gliding formwork, called Slipform but it is moving continuously (when pouring is being made) instead of periodically like the self-climbing formwork. The self-climbing formwork remains in place during the pouring process. Crane picked-up jump forms are typically used on buildings of five stories or more; fully self-climbing jump form systems are generally used on structures with more than 20-floor levels.
Normally, this type of formwork is constructed from steel members. Concrete form panels are attached to this frame; some of them supported on rollers. After the concrete walls are poured, it is released and moved away from the wall. Then, if self-climbing formwork is being used, jacks lift the frame up to the next level or to the next area where it will be used. Hydraulic jacking mechanisms independent of any external crane or lifting equipment. This is normally a relatively fast procedure.
Once the climbing formwork is in position, the panels are closed, and the next concrete wall is poured.
The cycle continues, which is normally three to five days. Faster times can be achieved but you will need a specialised and trained crew. However, the limiting factor to faster times is usually the construction of the floor slabs, which are poured as a separate process.
Where to use climbing formworks
It is highly recommended in super tall structures like skyscrapers, bridge pylons, airport control towers, high-rise buildings, elevator shafts, and silos.
Self-climbing systems are available as single or double jump formwork assemblies. As the name implies, the double jump system jumps two floors at a time leading to significant reduction of cycle time; the work to be done is halved. For instance, steel fixing activities have to be done only once every two floors, and the same concept applies to concrete pouring as two consecutive floors are poured together. Other time-consuming activities such as surveying operations, formwork alignment, and reinforcement inspections are also optimised to boost core wall construction speed. Therefore, as the number of cycles is largely decreased, the construction time undergoes substantial drops. The formwork is totally isolated from external weather conditions by cladded screens and a top deck free from mass constraints. This provides workers with a safe and adequate working environment.
Formwork systems play a vital role in leading high-rise construction, and technological advancements are pushing the limits of formwork industry to new perspectives allowing it to surpass traditional constructability constraints. The role of formwork systems in high-rise projects goes beyond erecting concrete elements to set the pace of construction processes at different fronts. Innovative features provided by advanced formwork technologies play a major role in streamlining concrete and non-concrete activities where downstream tasks are more sensitive to formwork pace. For example, this applies to the case of elevator related activities that undergo the same core wall cycle and to column and slab-related activities that follow the advanced perimeter pace. Advanced systems also impact logistics planning as faster labour and material delivery rates are achievable due to crane schedule release and the use of building service elevators early on in the project.
About author:
K Rajarama Rao, Chief General Manager – Materials, NCC Limited, is a civil engineer and seasoned category and supply chain expert in the construction industry with over 30 years of experience.
• They usually do not require a crane to move them reducing also your general condition cost.
• Increase construction speed is obtained by allowing the vertical and horizontal parts of a building to be built concurrently.
• It minimises labour time and has a better productivity rate (these systems are designed for repetitive actions) and less labour is required to set up the forms.
• Increased safety as the labour of setting and removing is less than traditional systems.
• It does not need additional supports to the formwork (it is supported by the walls just poured).
• It can be used during almost all type of weather.
• High-quality surface finishes can be achieved.
• Can sustain high winds (better productivity on windy days).
• The formwork system is easy to clean and reuse with little waste generated compared to traditional systems.
• Other protection systems (Screens) can be hung off a big Jump Form and climbed with the system.
• These systems will minimise the usage of scaffolding and temp work platforms.
Cookie Consent
We use cookies to personalize your experience. By continuing to visit this website you agree to our Terms & Conditions, Privacy Policy and Cookie Policy.