How PEB can save you money?
By Edit Team | May 17, 2017 9:49 am SHARE
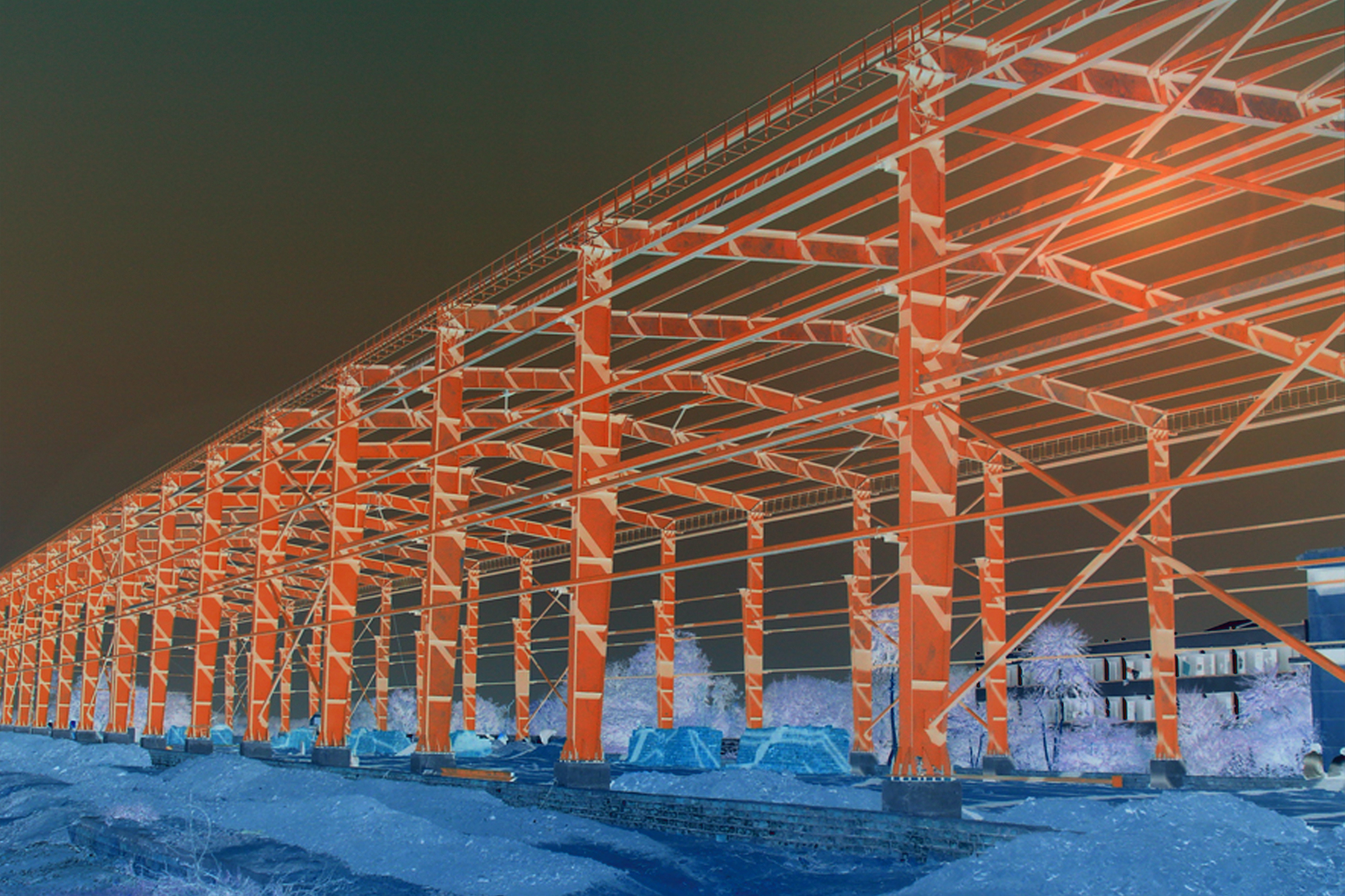
PEB is hogging the spotlight as the preferred modes of construction for warehouses and industrial buildings. Here we discuss why PEBs are economical.
Steel construction has found wide acceptance over conventional methods in industrial and commercial sector. Pre-engineered steel buildings have proven to be way safer, stable, fire resistant, energy efficient, and take less time to build. Steel construction offers better designs along with greater safety than that offered by conventional construction types. Steel proves to be relevant and beneficial to several construction verticals offering longevity of structure lifespan.
Cost savings starts from preparation stagePre-engineered steel buildings which were previously viewed as an expense, is now perceived as an investment. According to Gautam Suri, CTO and Founder Director, Interarch Building Products Pvt Ltd, “Cost savings begin right on the drawing preparation stage. Systems engineering and fabrication methods help reduce interim financing costs through faster construction and minimised field erection expense. An added benefit is the earlier occupancy of the facility and a head start on day-to-day operations of the client.”
Benefits from energy savings
He adds, “Pre-engineered buildings (PEBs) are eco-friendly and are made of material that is recyclable upto 90 per cent, saving primary resources and reducing waste, and thus saving energy. The unique design of these buildings helps in proper ventilation and temperature control, thus providing healthy and comfortable indoor environment and saves the day-to-day energy consumed.”
Lower life cycle cost
The foundation is comparatively lighter in the case of steel, thus further reducing the initial cost. “If we compare the complete life cycle of a pre-engineered building and RCC, then it is observed that a PEB is much more economical,” Suri said.
Reduced construction time
Due to the systems approach, the use of high strength steel, tapered built-up sections which are optimised by the computerised design program and the use of continuous light gauge secondary steel section, there is an overall reduction in steel weight, cost and time relative to conventional steel construction.
PV Rao, Managing Director, Pennar Engineered Building Systems Ltd opines, “PEBs are a predetermined inventory of raw materials that has proven over time to satisfy a wide range of structural and aesthetic requirements. The components are engineered beforehand and standardised. Use of these standard components reduces the engineering, production and erection time. Use of customised software for design and drafting increases the speed of the project.”
The production line is highly sophisticated, having auto welders, multi-cutting torches, shear cutting machines etc., which greatly reduce the time of fabrication of built-up components. Roll forming machines for producing Z&C members and sheeting, having standard dimension, increases the production capacity of secondary members. Use of standard accessories greatly increases the speed of production and erection.
Buildings are typically delivered in just a few weeks after approval of drawings. Foundation and anchor bolts are cast in parallel with manufacturing of the building. “Site assembly is fast, as all building components are delivered finished, ready for site bolting. It can reduce total construction time on a project by at least 50 per cent. This will allow faster occupancy and earlier realization of revenue,” Rao states.
Lower cost
Due to the systems approach, there is a significant saving in design, manufacturing and site erection cost. The structural elements are shaped to follow the stress diagram of the member, thus reducing weight, cost and load to foundations. The secondary members and cladding nest together reducing transportation cost. The overall price per square meter may be reduced as much as 30 per cent lower than conventional steel.
Savings by design
Nowadays most of the warehouses and industrial buildings are built by using the PEB technology, which was previously built either by conventional or RCC method. According to Dr. Sandeep Gupta, MD, Richa Industries Ltd, “The most important aspect which makes PEB widely accepted over conventional methods is cost and time saving feature.”
He further adds, “PEB designs are more effective and best optimised by using various software. Subsequently PEB also adopts lightweight foundations which can be embraced and prompts design coherence which decreases the overall building cost. These PEBs are designed and constructed by most optimised steel sections hence it reduced the consumption of steel as compared to standard steel section designs.”
Reduced manpower cost
PEBs are manufactured in factory premises by using automatic machines and are fabricated in such a way that they just need to be assembled and bolted at site. So, according to Dr. Gupta, it reduces the deployment of manpower and decrease over all manpower cost.
Faster ROI
The most important aspect of cost saving in PEB is Return on Investment (ROI) factor. “PEB is most advanced and follow the fastest mode of construction which helps in bringing down the overall project schedule quite a great extent as compared to conventional or RCC buildings. Due to faster completion customer can generate revenue in the shorter span of time and this results in lesser maturation period on investment and can promote faster ROI,” asserts Dr. Gupta.
Cookie Consent
We use cookies to personalize your experience. By continuing to visit this website you agree to our Terms & Conditions, Privacy Policy and Cookie Policy.