Inventive advances in concrete and asphalt plants
By Staff Report | October 21, 2024 3:05 pm SHARE
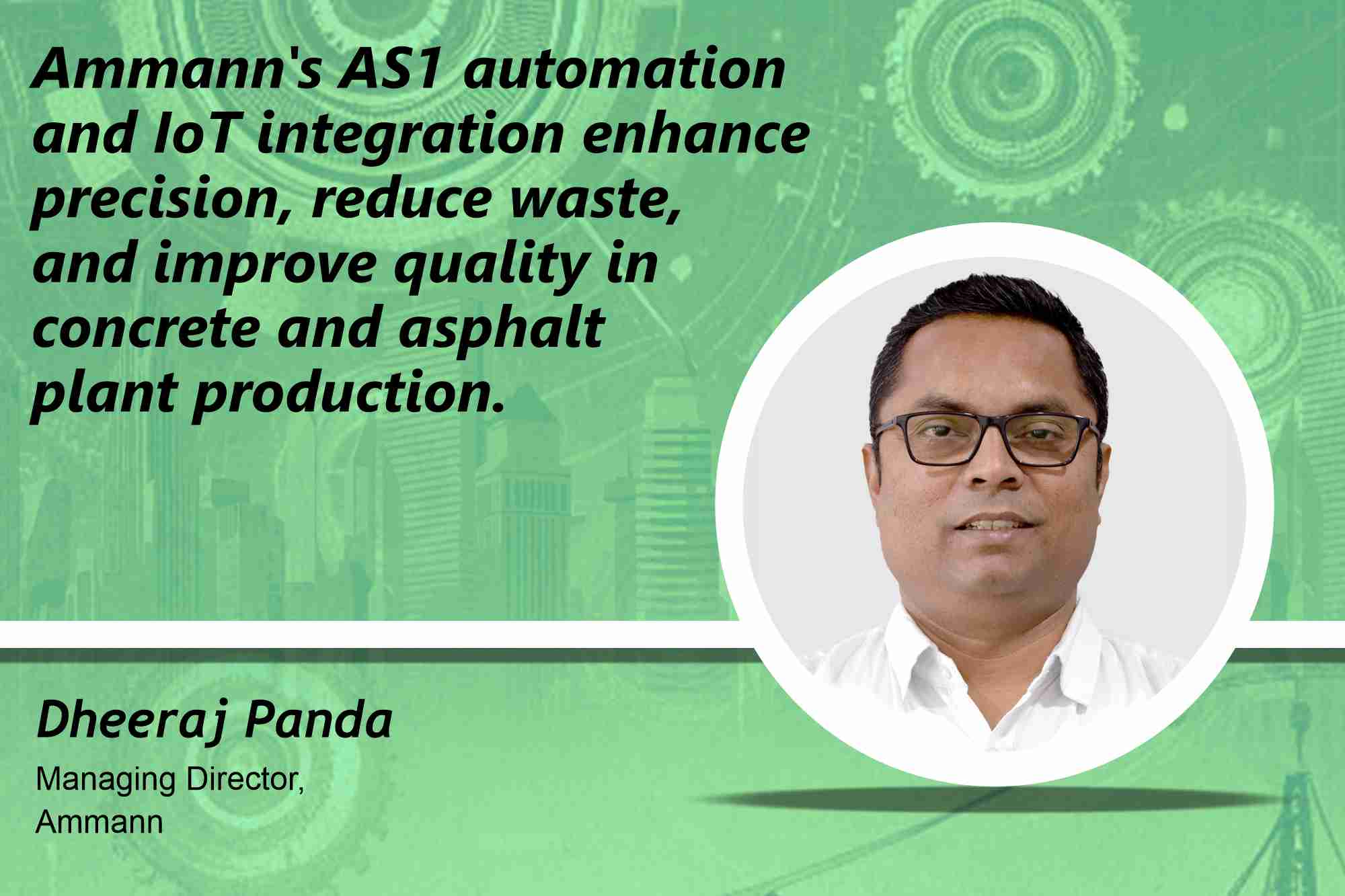
At the crossroads of sustainability and technological advancement, Ammann is shaping the construction industry’s future. Through cutting-edge automation, eco-friendly practices, and pioneering materials, Ammann’s concrete and asphalt plants are leading the way in efficient and sustainable infrastructure development.
The construction industry stands at a crucial juncture where the demands for efficiency, sustainability, and technological advancement drive significant changes. Ammann, a global leader in the field, has been instrumental in pushing the boundaries of what is possible in producing concrete and asphalt. Through integrating smart technologies, sustainable practices, and innovative materials, Ammann is not just meeting the current demands of the industry but is actively shaping its future.
Smart technologies in concrete and asphalt plants
Precision and consistency are paramount in the construction landscape. Ammann’s concrete and asphalt plants are designed with cutting-edge AS1 automation and control systems that streamline production. These systems ensure that every batch of concrete or asphalt is produced with the exact specifications required for the project, reducing deviation and enhancing quality.
The automation in our plants extends to various aspects of production, from material feeding and mixing to temperature control. These systems have sensors and feedback loops that constantly monitor the process, making real-time adjustments to maintain optimal conditions. The result is a significant reduction in waste, energy consumption, and the likelihood of human error, all of which contribute to a more efficient and sustainable operation.
The control systems are also designed to be intuitive and user-friendly, enabling operators to manage complex production processes easily. This ease of use is complemented by the ability to store and retrieve production data, allowing for detailed analysis and continuous improvement in plant operations.
Ammann has embraced the potential of the Internet of Things (IoT) and Artificial Intelligence (AI) to enhance the performance of its plants. IoT sensors are strategically placed throughout the plant to collect real-time data on various parameters, such as temperature, moisture, and material flow. This data is then analysed using AI algorithms to predict potential issues, such as equipment wear or material inconsistencies, before they lead to significant problems.
For example, maintaining the correct temperature is crucial for achieving the desired mix quality in asphalt production. IoT sensors monitor the temperature throughout the process, while AI analyses this data to detect any deviations that could affect the final product. If a potential issue is detected, the system can automatically adjust the process parameters or alert the operators, ensuring that the mix meets the required standards.
Predictive maintenance is another significant benefit of IoT and AI integration. By continuously monitoring equipment conditions, the system can predict when maintenance is needed, allowing operators to address issues before they cause downtime. This not only enhances the reliability of the plant but also extends the lifespan of the equipment, resulting in lower operational costs and increased productivity.
Monitoring and managing our plants remotely provides flexibility and control that are increasingly important in a sustainable construction environment. With remote monitoring, operators can oversee the operation of multiple plants from a central location, making it easier to coordinate large-scale projects that span different geographic regions.
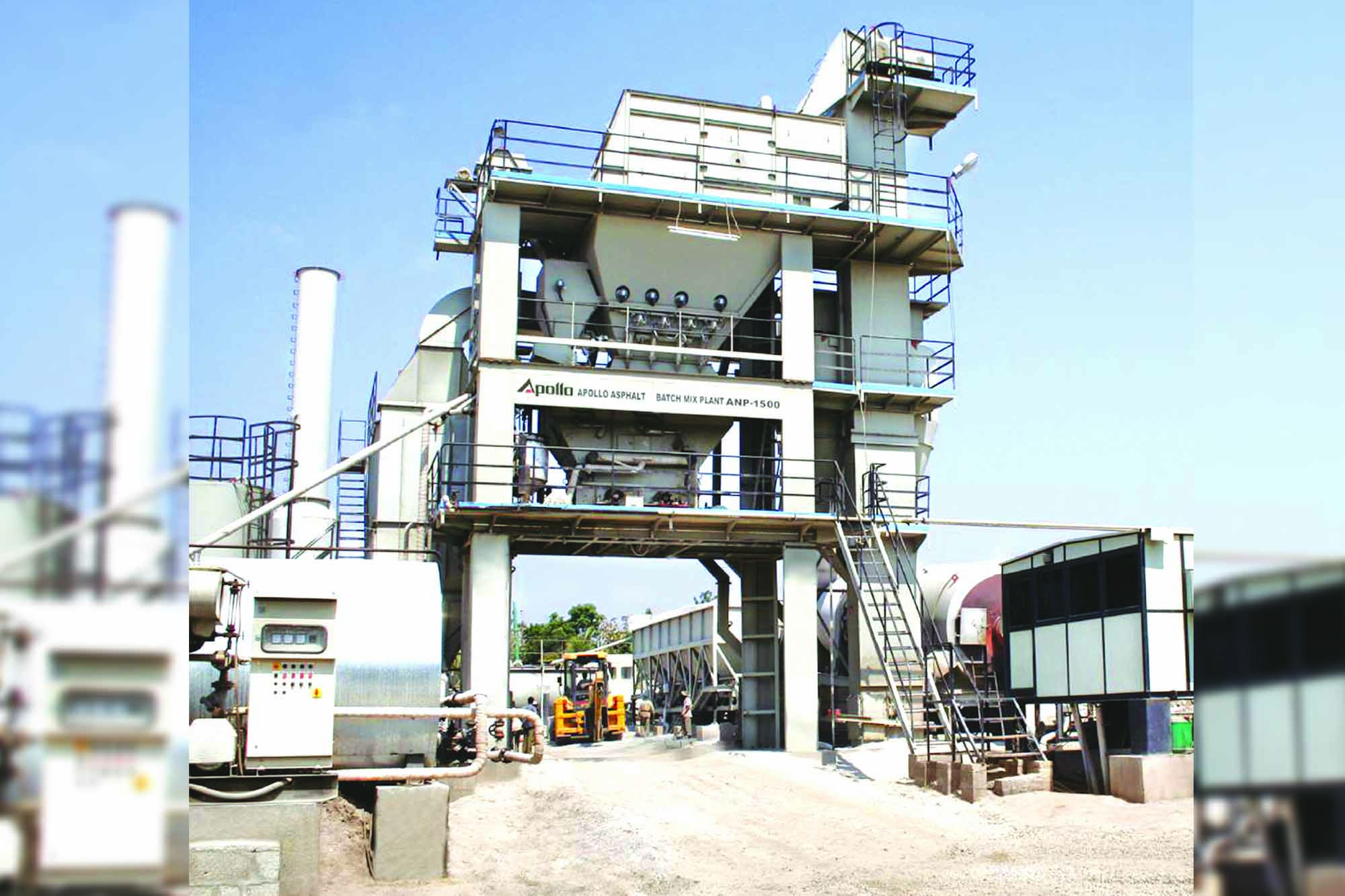
Remote management capabilities also allow for rapid response to changing conditions. Whether adjusting production schedules in response to weather changes or scaling up operations to meet an unexpected surge in demand, making these adjustments in real-time is invaluable. This flexibility improves operational efficiency and ensures that projects are completed on time and within budget.
Sustainable practices in concrete and asphalt production
As the world becomes more conscious of the environmental impact of industrial activities, Ammann has made energy efficiency and emissions reduction a core focus of its plant design. Our asphalt plants, for example, are equipped with energy-efficient motors, Low-temperature asphalt technology, an advanced burner, alternate carbon-neutral fuel, and dryer technology. The state-of-the-art Pollution control unit optimises fuel combustion, significantly reducing greenhouse gas emissions.
Ammann uses energy-efficient motors, pneumatic actuation, and drives in concrete plants to reduce electricity consumption. These measures reduce the plants’ energy footprint and result in significant cost savings for operators.
Ammann’s commitment to reducing emissions extends to dust control systems in concrete and asphalt plants. These systems capture and filter dust particles, preventing them from being released into the atmosphere. This improves air quality in and around the plant and ensures compliance with increasingly stringent environmental regulations.
Our plants can also be equipped with special silencers to reduce noise
One of the most significant advancements in asphalt production is the ability to recycle Reclaimed Asphalt Pavement (RAP). Ammann has pioneered the development of plants that can incorporate high percentages of RAP into new asphalt mixes. This reduces the need for virgin materials, conserves natural resources, reduces bitumen usage, and lowers asphalt production’s carbon footprint.
The use of RAP also has economic benefits, as it reduces material costs for contractors. Our plants are designed to ensure the recycled material is fully integrated into the new mix without compromising quality. This is achieved through precise temperature control and mixing processes that ensure the recycled asphalt bonds effectively with the new materials.
Ammann promotes using recycled aggregates and supplementary cementitious materials (SCMs) such as fly ash and slag in concrete production. These materials are by-products of other industrial processes and can replace a portion of the cement and aggregates in concrete mixes. This reduces the demand for natural resources and enhances the durability and performance of the concrete.
In addition to recycling water, Ammann’s plants are designed to minimise water use overall. This includes optimising the mix designs to reduce the water-to-cement ratio in concrete and using additives that improve workability without increasing water demand. These measures help maintain Ammann plants, even in challenging environments and help them operate sustainably.
Innovative materials in concrete and asphalt plants
Ammann’s commitment to innovation is evident in its development of high-performance materials that enhance the durability and efficiency of its plants.
For example, critical components in their asphalt plants, such as mixing arms and liners, are made from wear-resistant alloys that can withstand the abrasive nature of the processed materials. This reduces the frequency of maintenance and replacement, resulting in lower operational costs and less downtime.
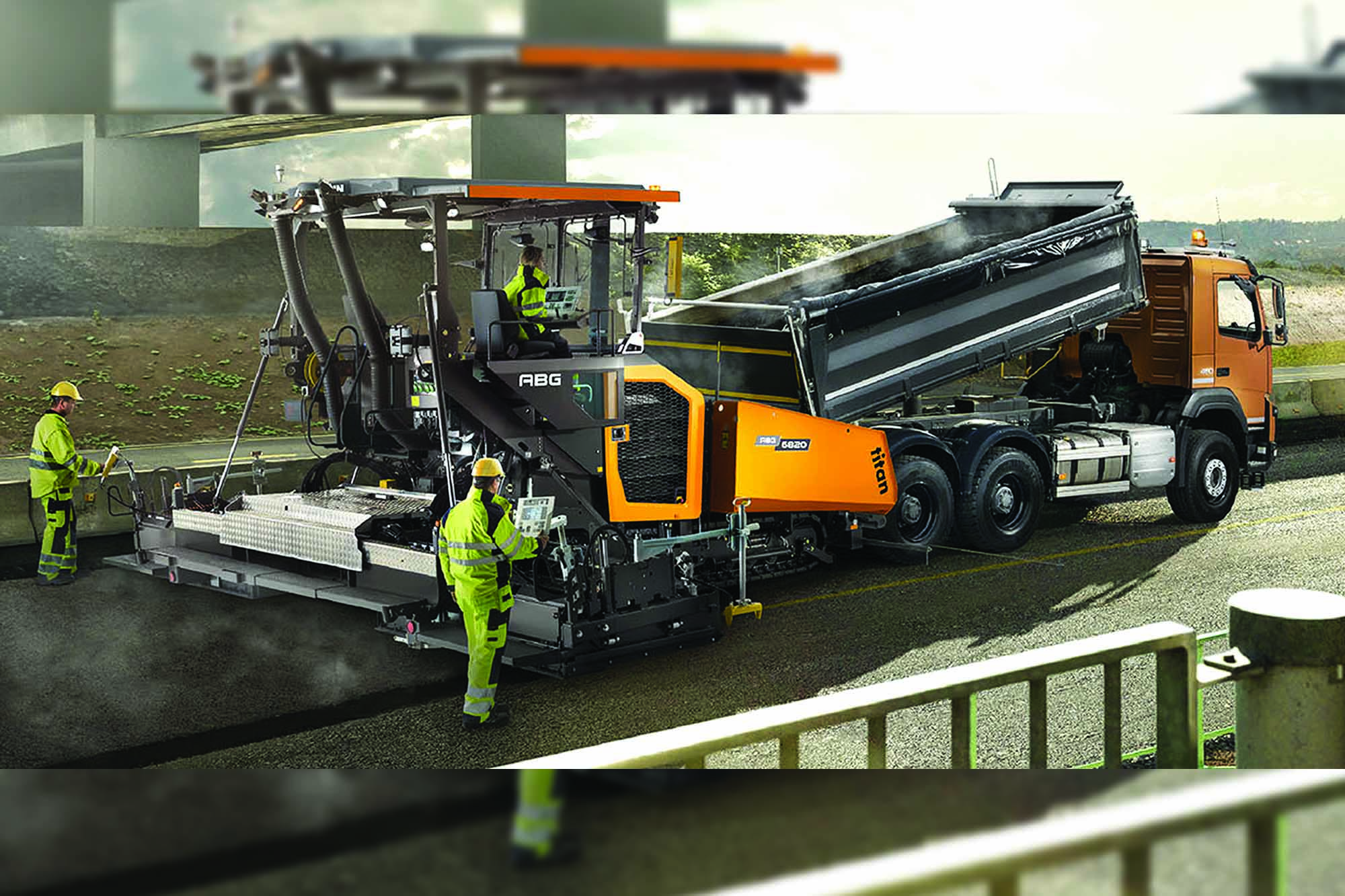
Ammann ELBA produces high-performance concrete mixers that can incorporate advanced admixtures to improve strength, durability, and workability. These mixes are designed to meet the specific requirements of different construction projects, from high-rise buildings to infrastructure projects like bridges and roads.
Ammann is at the forefront of developing and using sustainable concrete and asphalt production materials. Using supplementary cementitious materials (SCMs) like fly ash and blast furnace slag reduces the production process’s carbon footprint in concrete. These materials not only replace a portion of the cement but also improve the long-term durability of the concrete.
Ammann plants can use bio-based additives and rejuvenators to enhance the performance of recycled asphalt. These additives help restore the properties of aged asphalt, allowing it to be reused multiple times without compromising quality. This contributes to a circular economy where materials are continually recycled, reducing waste and conserving resources.
Ammann’s concrete and asphalt plants are a testament to the company’s dedication to pushing the boundaries of what is possible in construction. By integrating smart technologies, sustainable practices, and innovative materials, Ammann is not only meeting the current demands of the industry but is also setting the stage for a more efficient, sustainable, and technologically advanced future.
The company’s commitment to sustainability is evident in its focus on energy efficiency, emissions reduction, and the use of recycled materials. Meanwhile, its investment in smart technologies and high-performance materials ensures that Ammann’s plants remain at the cutting edge of the industry, delivering superior performance and value to customers worldwide.
As the construction industry continues to evolve, Ammann’s holistic approach to innovation will play a crucial role in shaping the future of infrastructure development. By staying ahead of trends and anticipating the needs of its customers, Ammann is not just a leader in the industry but a pioneer, paving the way for the construction of tomorrow.
For more information, visit: https://www.ammann.com/en-IN/
Cookie Consent
We use cookies to personalize your experience. By continuing to visit this website you agree to our Terms & Conditions, Privacy Policy and Cookie Policy.