Maintenance: secret of better PEB life
By Edit Team | February 19, 2014 10:02 am SHARE
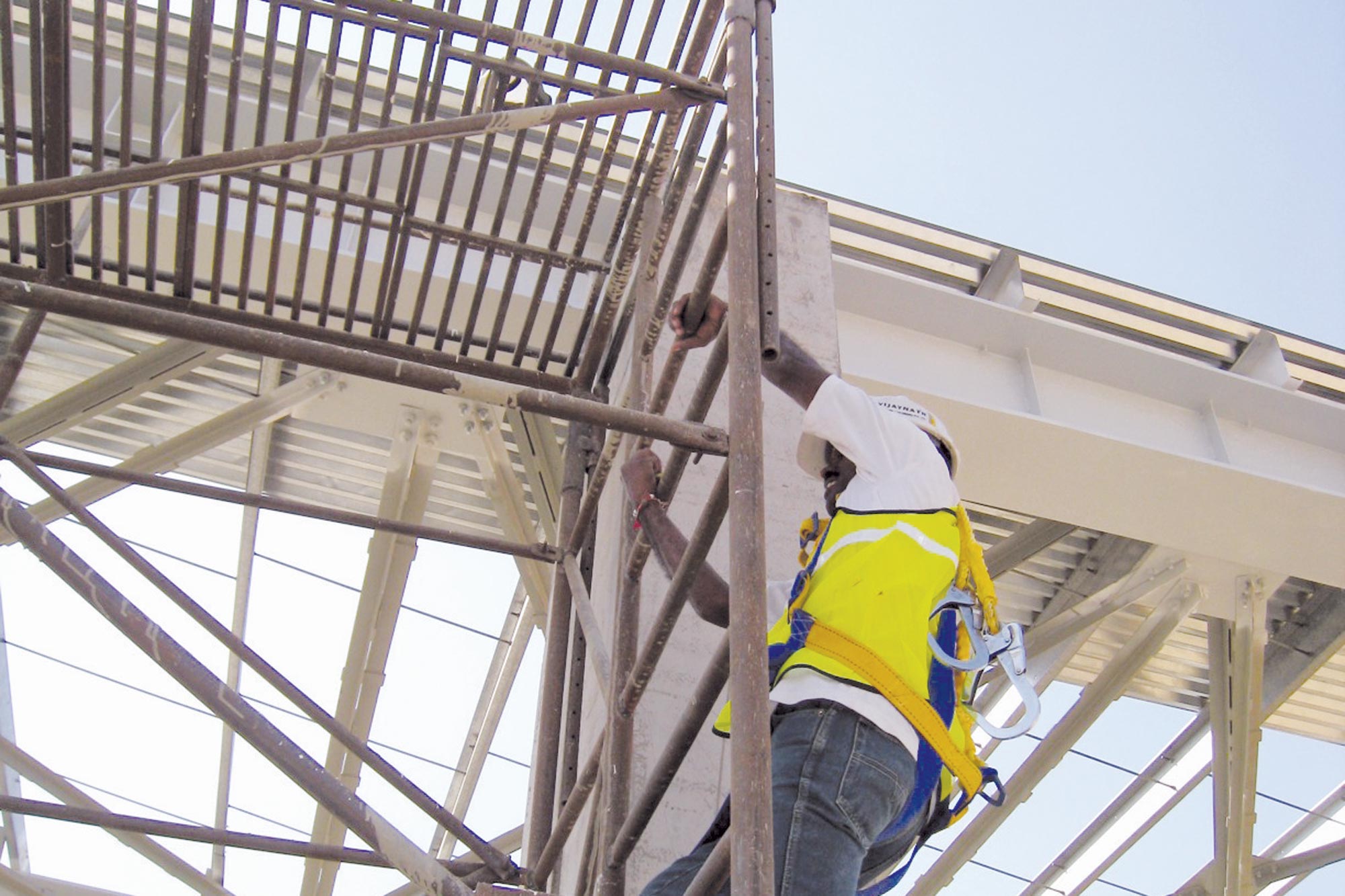
A preventive maintenance program is a key factor in maximising the life expectancy and dependability of PEBs
India has the fastest growing market in the PEB construction segment. Infrastructure development and the increasing popularity of PEB systems in the industrial sector have led to a robust growth of Indian PEB market. PEBs have hit the construction market in a major way owing to the many benefits they possess. The PEB concept has been gaining momentum, and the scope of growth is increasing due to India’s huge infrastructural requirements. The scope of using PEBs ranges from showrooms, low height commercial complexes, industrial building and workshops, stadiums, schools, bridges, fuel stations, aircraft hangers, exhibition centres, railway stations and metro applications.
Regular maintenance
Regular maintenance is an important factor to maximise the life of PEBs. PEBS Pennar, which has taken up many major projects, believes a preventive maintenance program is a key factor in maximising the life expectancy and dependability of roof systems. I. V. Ramana Raju, Sr General Manager – Sales and Marketing, PEBS Pennar, says, “Maintenance depends upon the locality of the building. Building areas with moisture and dry climate requires proper care than in mild and less populated industrial areas. Maintenance of the building can be taken by stagnation of unwanted materials and debris. Mostly, the vulnerable areas of the building like gutters, down spout, roof sheets and shelters areas under eaves and canopies covered with dirt, gutter and water should be washed off with clean water and soft brush. Less preference to maintenance will lead to short life of buildings.”
According to Rohit Ranjan, General Manager – Marketing, Tata BlueScope Building Solutions, “The steel buildings also require attention to maintain their performance, appearance and value like any other investments. Steel buildings considerably have lower maintenance need than those of concrete structures. Nevertheless, maintenance contributes to the appreciably longer operational life of a steel building. Clean surfaces enhance the life of steel buildings as well as improve the thermal performance of steel buildings. Corrosion and physical damage are area for concern. Timely repair retains both functionality and aesthetics of the structure.”
Mahesh Verma, Sr Vice President – Operations, Interarch, believes that a metal building or roof assembly should last 15 to 30 years before serious maintenance is required. Yet, due to various environmental and pollution related factors, many metal buildings and metal roofing assemblies require slight maintenance from time to time. “To achieve the desired life and functionality, maintenance of the building is also important just like other maintenance of machines and equipment,” he said.
Maintenance period
Periodic maintenance of PEB depends upon the environmental zone and pollution level in which the building is located. In PEB, the core maintenance is required for the steel roofing and cladding.
In the humid areas, buildings should be taken much care as the moisture presents in the air breakdowns the paint.
Maintenance procedure
“Maintenance procedures varies from building to building and depends upon building design, material specifications and access provisions,” explains Mr Ranjan. “It is also necessary to ensure that the leak-proof performance of the building is not compromised.”
According to Mahesh Verma, “Preventive maintenance of PEBS begins immediately after a project is erected. Waste and small items such as screws, pop rivets, drill bits, or any ferrous objects are removed by sweeping with a soft nylon brush. Large items such as sheet metal cut-off are removed by hand to avoid damaging the surface of the roof panels. Sand and dust shall be removed by washing with clean potable water and a soft nylon brush. To remove saline deposits that become encrusted on the panels of buildings located in high pollution industrial areas, or close to marine environments should be washed with the mild detergent added to the initial washing water. Oil, grease, tar, wax, or similar substances can be removed with mineral spirits, followed by a detergent solution and a clean potable water rinse. Caustic or abrasive cleaners may damage the paint and zinc layers.”
Need of expertise
According to Anjan Dutta Roy, Vice President, Tiger Steel Engineering (I) Pvt. Ltd., “Pre-engineered steel building is a highly technical product to maximise the operable benefits. The expertise is required for its each and every aspect — be it design, manufacturing or erection.”
Interarch PEBs use a variety of materials, all built up using high tensile 550 Mpa steel. All buildings are 100 per cent steel which is recyclable up to 90 per cent. Their construction sites help in reducing the carbon footprint by reducing the solid waste and construction waste, resulting in less maintenance of the building. Buildings are engineered, designed and conceptualising keeping in mind the local climate. So that everything could be incorporated beneficially for the design of the building. The use of natural ventilation systems in buildings keeps the temperature in control and provides healthy, comfortable indoor environment which further requires minimal use of electricity. Interarch’s buildings are not just eco-friendly, or maintenance free in the long run but also enable the projects to achieve higher LEED and IGBC ratings which contribute a higher certification for project.
Safety measures during maintenance
A completed roof of a steel building is a safe surface, except near the edge and roof openings, or if it becomes slippery due to moisture.
- The following steps should be maintained in maintenance:
- No walking on wet floors, gutters
- No stepping on skylights
- Availability of fire extinguishers.
- Use ladders that is 1 metre above the step-off
- Site safety procedure and emergency contacts.
Use of personal protection equipment, contemporary tools and machineries are mandatory. Use of passive restraint mechanisms like Skyweb fall protection system significantly reduces risk during maintenance. Sufficient precautions should also be taken toward electrical safety and hazardous substances.
Cookie Consent
We use cookies to personalize your experience. By continuing to visit this website you agree to our Terms & Conditions, Privacy Policy and Cookie Policy.