Mega projects showcase the potential of precast in India
By Edit Team | October 30, 2023 5:13 pm SHARE
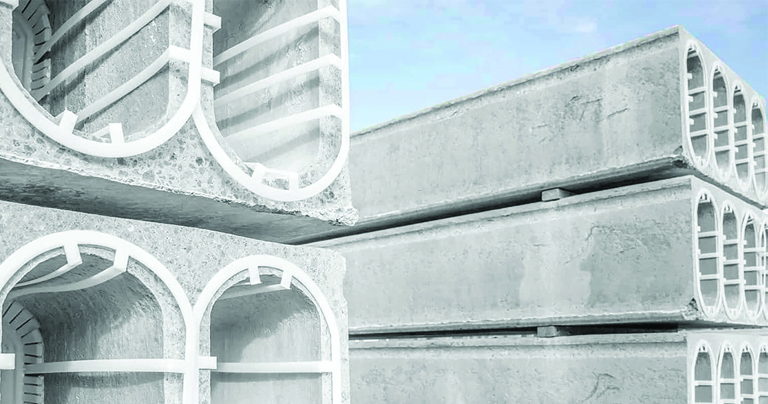
Story by story, Asia’s tallest precast towers, with a planned Built-up Area of 3.7 million square meters, stretch toward the sky in Hyderabad, Telangana State, India. My Home Construction chose Elematic as its structural design partner and equipment supplier for this monumental project.
Following the construction of two iconic 43-story towers in Hyderabad, each rising to 180 meters, six more are set to join them. Each tower occupies a Built-Up Area (BUA) of 241,000 square meters. The cumulative area for the eight towers is a staggering 1.9 million square meters, marking them as part of the world’s most expansive commercial precast development.
Together, the tower and non-tower spaces encompass over 3.7 million square meters. The inaugural two towers are expected to be completed by next year. Once the entire “My Home – GRAVA” project concludes in 2050, it’s estimated that around 250,000 professionals will be working within these IT structures.
Pioneering precast in India
In a departure from the construction norms of traditional Indian buildings, every element of this development is crafted in a factory and then assembled on-site, thanks to the adoption of precast construction technology. The Senior President for Projects at My Home Construction, Ravi Sai describes the mega project as both a challenge and a thrill for all involved, given its pioneering essence.
As one of the rapidly escalating economies globally, India has witnessed My Home Construction, a renowned developer and construction firm based in Hyderabad, grow extraordinarily. To maintain this momentum and elevate its scale of operations, My Home sought a construction methodology that is time-efficient, material, workforce, and eco-friendly.
Sai says, “There was a necessity for assistance to identify the optimal technology that would elevate our development standards.” This search for innovation led them to embrace precast technology, with Elematic playing a crucial role in this transformative journey.
Quality and speed with less labour
My Home comprehensively analysed various construction techniques before settling on precast technology for their ambitious project. “We considered steel, but it couldn’t match the affordability and availability of precast concrete structures. Precast not only guarantees quality and speed but also requires significantly fewer workers. As the volume of construction escalates, the expenditure declines. With increased capacity utilisation, the costs plummet. It became apparent that precast was the definitive choice for a project of this scale,” explains Sai. “After extensive research, we are confident that we’ve chosen the correct direction.”
In a comparative assessment, Sai reckons that utilising traditional cast-in-situ concrete construction for a project of such magnitude would necessitate the engagement of up to 7000 workers. In stark contrast, around 200 individuals are currently employed at what is now India’s most extensive precast plant, efficiently producing all requisite components. The quality of slabs, panels, beams, columns, and staircases is meticulously maintained. An additional team of 150 specialists oversees the ongoing construction activities on-site.
Elematic – a one-stop shop for design, equipment, and installation.
The revelation that precast was the optimal solution led My Home to find a substantial supplier capable of designing, delivering, installing, and servicing a precast plant of unprecedented scale in India. “I’ve been familiar with Elematic since 1993. Their equipment ranks highly globally, easily within the top 3. The assurance that they can provide future service and spare parts supply made our decision straightforward,” shares Sai.
Elematic was brought into the project’s fold during the planning stage about three years prior. “Being integrally involved in such an expansive project from its inception marks a monumental milestone in Elematic’s journey,” expresses Chander Dutta, the Managing Director of Elematic India, with a mix of pride and joy.
Tailored to meet the project’s unique demands, a precast plant boasting an annual Built-Up Area capacity of 460,000 square meters was established. This facility outfitted with moulds and machines installed by Elematic’s adept project team, is geared to supply all the precast components required for this ambitious undertaking. “Our approach begins with a thorough assessment of the client’s needs and project specifications,” Dutta explains. “Armed with insights from the concept design study and data on the daily requirement of various elements, we customised the plant to be a perfect fit for this project, ensuring automated, flexible, and waste-free production.”
Mr. Sai, overseeing this colossal venture, applauds the efficiency of the factory and the post-sale services offered by Elematic. He attests that the transition from shop drawings to the production of precast elements has been seamless. “We’ve hosted visitors from the UK who were astounded by the superior quality of precast concrete produced here in India,” Sai remarks, his pride evident in his smile.
Designing for repeatability
The entire structural design of the development has been the responsibility of the Elematic Structural Design team based in India. Both Dutta and Sai agree that the collaboration between their respective teams has been exemplary, although not without its challenges.
In the initial stages of the GRAVA project, a distinct design was applied to each floor. This presented complications for the structural designers, as each floor demanded individual calculations and designs for various dimensions and loads. Every element needed a tailored design approach.
However, a shift occurred with the introducing of a new team of architects. The design process was streamlined, with all floors above the lobby being uniformly designed. This modification enabled My Home to fully leverage the efficiencies of factory-based building technology fully, bringing the process back on course and advancing it ahead of the anticipated schedule!
Under pressure to show the potential of precast
Taking the lead and embarking on ambitious projects comes with its own set of challenges and anxieties, shares Sai. “The onus is on us to prove the viability of precast. With a venture of this magnitude, I grapple with a sense of trepidation daily.”
To mitigate any potential issues, He emphasises My Home collaborates with top-tier consultants. He ensures that the equipment used in the precast factory and construction site is second to none.
“This project serves as a testament and a monumental showcase of the possibilities with precast in India,” Sai asserts. “Upon its successful completion, there will be no room for doubt – precast represents the way forward!”
Precast in India
India is on a trajectory of rapid economic expansion, with projections from the International Monetary Fund (IMF) indicating a persistent growth rate of over 6% annually extending into the next decade. With a population exceeding 1.4 billion, the nation is witnessing a construction surge, particularly in the southern regions, known for their IT and technology enterprises concentration.
Traditional cast-in-situ construction, although prevalent, is grappling with constraints like stringent timelines and a need for more skilled labour. These challenges catalyse a shift towards more efficient, mechanized, less labour-intensive construction methods.
The Indian Government has endorsed precast construction as a forward-thinking, innovative solution. This sentiment resonates with numerous developers across the country who are attuned to the advantages of this technology.
“An increasing demand for precast technology is evident, alongside expectations for expedited project deliveries,” notes Chander Dutta, Managing Director of Elematic India.
Demand for end-to-end solutions
Despite significant interest, India is still navigating the complexities of fully embracing this innovative construction technology, leading to a surge in demand for comprehensive solutions. Elematic commands a pivotal presence in the Indian market, holding nearly 70% of the market share. A dynamic team of approximately 150 specialists offers an all-encompassing source for precast technology, including structural design, project installation, commissioning, and ongoing support and maintenance. Given that many regions in India are prone to seismic activity, Elematic’s engineers are adept at creating structures engineered to withstand earthquakes.
Elematic’s upcoming colossal project involves a partnership with Sun Pharma, a leading global pharmaceutical entity headquartered in India. The collaboration entails providing the technology and overseeing the erection of an impressive 1,000 towers, each scaling 28 stories.
FACT BOX
The My Home GRAVA project, Hyderabad, India
Timeline
o Plant installed, and the project started in 2021
o First two towers (phase 1 of 4) planned to be completed by 2024
o The entire project should be completed and ready for use in 2050
Buildings
o A planned total BUA of 3.7 million square meters (40 million square feet)
o Commercial buildings for IT offices
o 43-story, 180-meter towers
o Structural design by Elematic in cooperation with Sweco Finland
Precast plant
- Tailor-made and delivered by Elematic for the project
- Manufactures all types of elements needed for the project
- Prestressed hollow core slabs
- Prestressed precast beams
- Precast columns
- Precast shear walls
- Precast stairs
- Can be used for other projects afterwards
Cookie Consent
We use cookies to personalize your experience. By continuing to visit this website you agree to our Terms & Conditions, Privacy Policy and Cookie Policy.