Mineral Beneficiation Expertise at MSEL
By Edit Team | November 8, 2016 6:30 am SHARE
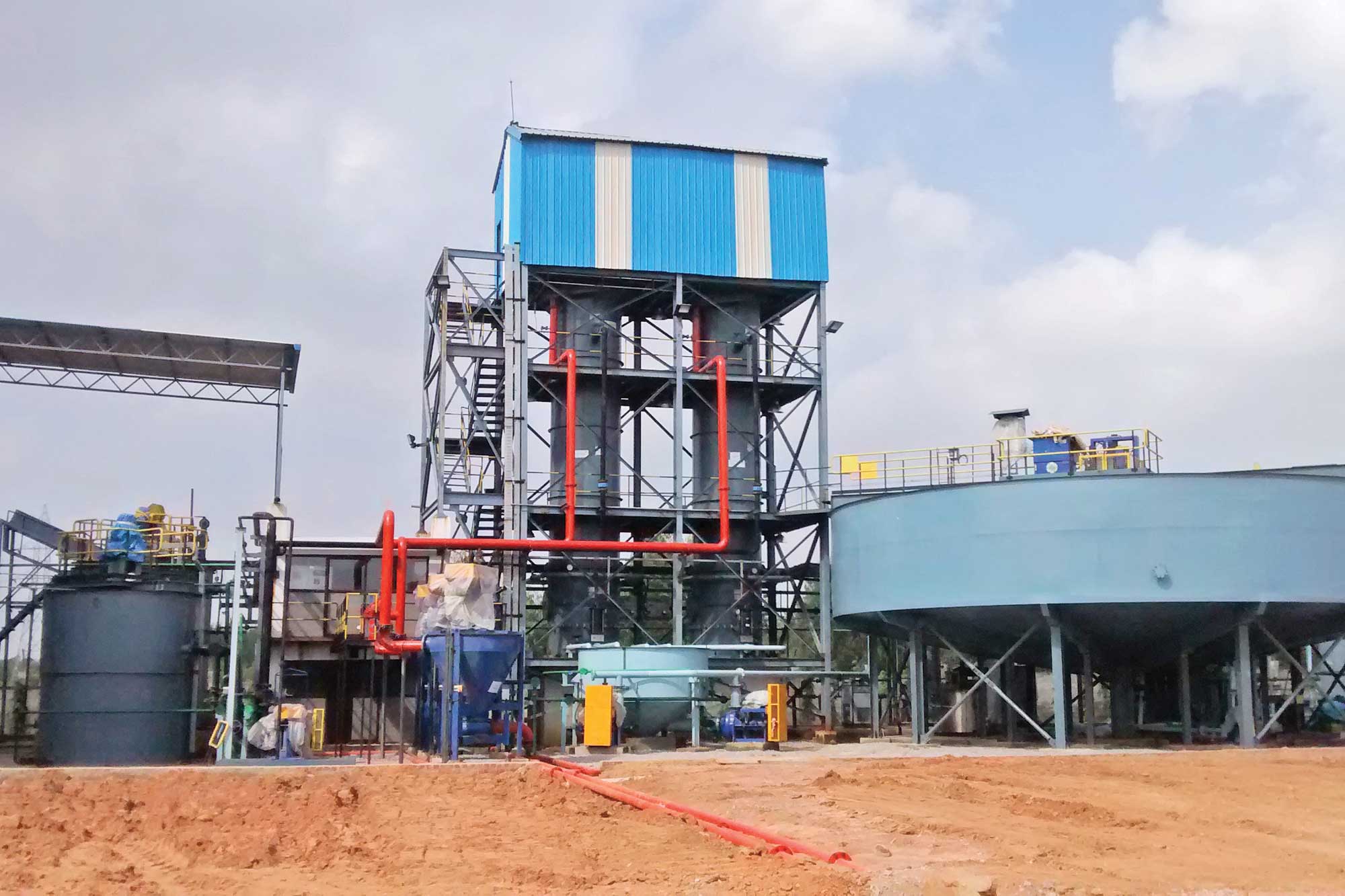
Historically, most mineral beneficiation plants have been built as complete projects on EPC basis involving civil, structural, electrical, piping and all other site work. However, there are several clients who seek plants to be set up on EP basis where they look for technology and reliable equipment along with performance guarantees. This not only saves costs significantly as turnkey contractors hedge for uncertainties but also reduces cycle time drastically. The project ownership is high as the operating team is involved in setting up of the plant right for the conceptualisation of the project.
McNally Sayaji Engineering Limited (MSEL) meets this need by offering complete basic engineering for the plant and the process equipment package. Based on customer needs, the offering can be expanded to include detailed engineering and other equipment like utilities, instruments and valves, electrical panels and automation etc.
MSEL’s main advantage lies in the fact that most of the equipment required for a beneficiation plant are manufactured in-house. For the balance equipment not in its range, MSEL have entered into strategic tie ups with leading global companies. Either way, MSEL possesses a deep understanding of the technology for each equipment, its capabilities and limitations, the installation and maintenance requirements and general do’s and don’ts. The project team at MSEL has engineers who have operated and maintained large process plants and hence provide the practical inputs. Put together, MSEL’s knowledge base helps the company to design process plants that are well laid out to facilitate convenience for operation and maintenance. More importantly, the plant designs ensure that the teething problems are reduced to a bare minimum and the start-up and stabilisation of the plant is completed within a short span.
A few landmark projects
MSEL has till date designed and supplied the following plants
• 110 TPH Iron ore grinding and filtration system to feed a 0.6 mill TPA Pelletisation plant for Sarda Energy and Minerals Ltd, Raipur
• 160 TPH Iron ore grinding and filtration system to feed a 1.2 mill TPA Pelletisation plant for MSPL, Hospet
• 35 TPH Baryte Beneficiation plant for Andhra Barytes Ltd at Mangampet in Andhra Pradesh.
• 175 TPH Iron Ore Beneficiation plant with Gravity and High Gradient Mag separation to feed a 0.8 mill TPA Iron ore beneficiation plant for Rashi Ispat Ltd, Bilaspur
• 45 TPH Baryte beneficiation plant for Oren Hydrocarbons Pvt Ltd, Chennai
• Two 250 TPH Iron ore Beneficiation plant with Scrubber, Jigs (Coarse and Fines), High gradient Magnetic separation, Thickening and Filtration at Sanindpur Mines, Barbil for Rungta Sons Pvt Ltd.
Manufacturing prowess
MSEL’s manufacturing range includes a wide range of crushing, screening, feeding, grinding and other beneficiation equipment like rotary scrubbers, slurry pumps, thickeners, flotation cells and filter press. The various crushers includes jaw, single and double roll, hammer mills, impactors and ring granulators. MSEL designs and manufactures roller screens, circular, linear and elliptical screens. The largest apron feeder of 74-metre length has been manufactured by MSEL. MSEL also manufactures vibratory feeders and roller feeders.
Most of the ball and rod mills in the country for mineral processing plants are supplied by MSEL and are manufactured at the Kumardhubi works of MSEL which has the capability of manufacturing mills up to 5.2-metre in diameter. The ball mills are of mechanical (diaphragm) and overflow Discharge type while the rod mills are of end peripheral, central peripheral and overflow discharge type. Grinding mills are widely applied in mineral processing industry (iron, lead-zinc, uranium etc.), cement industry, new building materials, fire resistant materials, fertiliser Industry, porcelain and glass industry and steel plants. The mills are renowned for reliability and performance and there are many references of installations more than 30 years old.
MSEL has been manufacturing Slurry Pumps, thickeners and flotation cells for over 20 years. The technology for these equipment was based on collaborations with world’s leading manufacturers for these equipment.
There are over 5,000 slurry pumps operating in India and overseas catering to a range of applications and transporting a variety of slurries. Some of the key applications include ball mill discharge, tailings disposal, ash slurry disposal, slag granulation, flotation froth slurry, and mill scale slurry. The range includes single casing as well as twin casing horizontal pumps, vertical sump pumps and Froth pumps with integral conical tank. Pumps can be offered to handle slurry volumes upto 2,500 cum/hr and deliver heads up to 90-metre.
MSEL has supplied over 300 thickeners in various sizes upto 65 m dia. Again, these thickeners are being used for solid liquid separation in a wide range of applications which includes concentrate and tails applications in mineral beneficiation plants, dust and scales in steel and sponge iron plants, sand slimes, chemicals, coal, industrial effluent, sugar juice, paper etc.
MSEL flotation cells have almost 80 per cent share of the installations in India. The cells employ forced air and are offered with a U-shaped tank that provides several advantages over conventional rectangular cells. The company’s cells are operating in beneficiation circuits for Lead Zinc, Copper, Iron ore, sillimanite, coal, graphite, Limestone etc.
In addition, MSEL has recently tied up with Choquenet of France to offer filter presses for a wide range of applications. Three filters have been delivered for iron ore tailings application and another three filters for blast furnace scrubber dust application.
MSEL manufacturing range also includes various material handling equipment like the stacker, reclaimer and stacker cum reclaimer, wagon tipplers, paddle feeders, pulleys and idlers. MSEL has a long standing collaboration with Famur Famac for manufacture of these equipment and has till now manufactured more than 45 stacker cum reclaimers and 15 wagon tipplers.
Apart from its own equipment, MSEL has a modern manufacturing facility at Asansol for precision machining and manufacturing of large equipment mainly for the steel plant. They include equipment for the billet and bloom caster (all types of roller tables, billet lifting device, TOCB, dummy bar unit, tundish components and machine support structures), convertors (various ladles, ladle transfer car, hood traverse carriage, scrubbing towers) and blast furnace (bleeder valve, dewatering drum, profile meter). The customers include Siemens (now Primetals), SMS, Danieli and Paul Wurth as well as the steel majors like Bhusan Power and Steel, JSW and JSPL.
A major advantage MSEL is the set-up of strong after sales service team and availability of spare parts with branch offices located at all major mineral belts of the country.
Authored by__
Subir Chaki
Whole Time Director
McNally Sayaji Engineering Ltd.
Cookie Consent
We use cookies to personalize your experience. By continuing to visit this website you agree to our Terms & Conditions, Privacy Policy and Cookie Policy.