MMD provides green mining solutions
By Edit Team | March 20, 2017 10:23 am SHARE
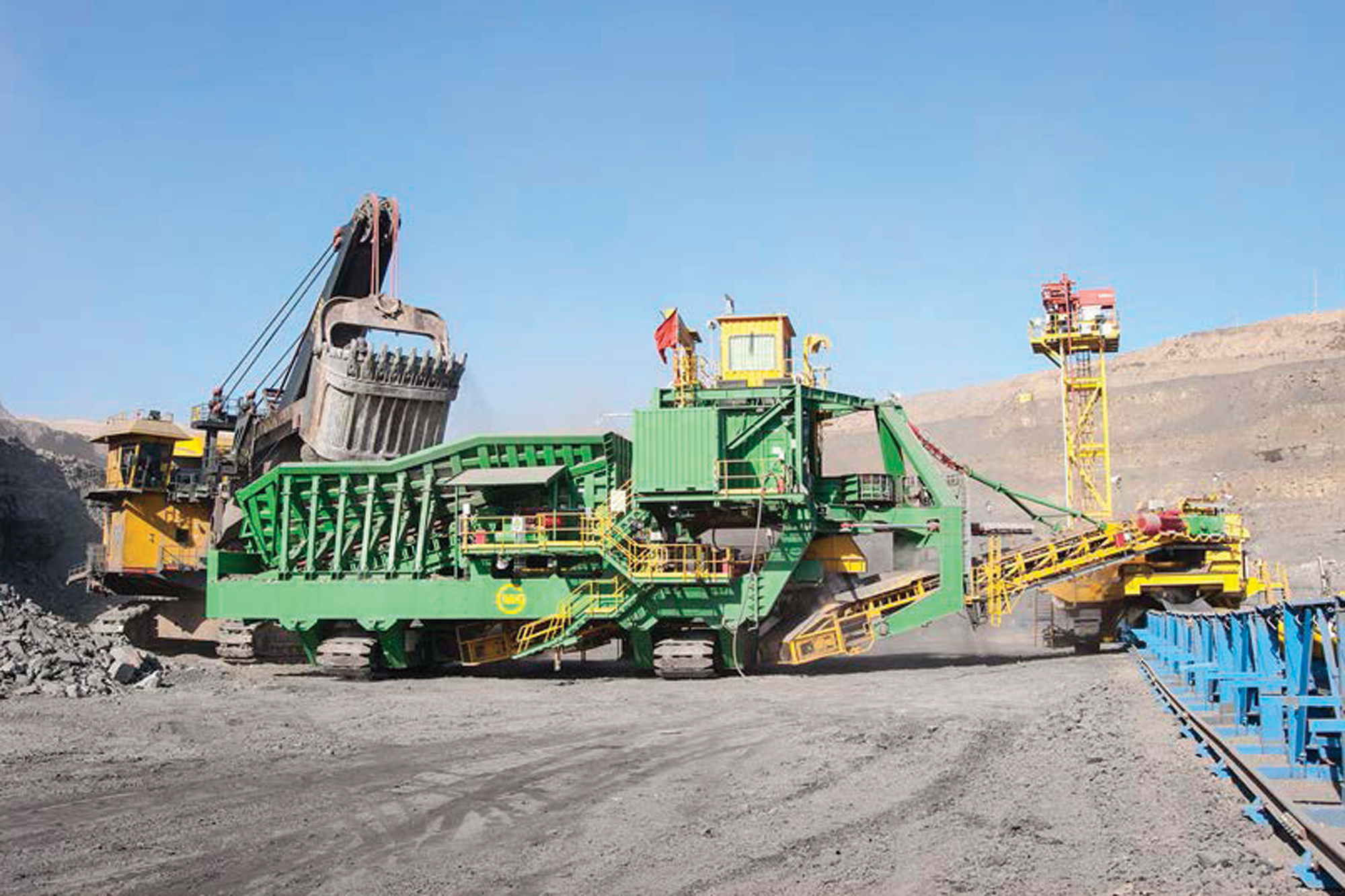
The article explains why a mining operator should consider MMD Sizer.
Global mining is changing: rising costs, environmental pressures and health and safety have called time on traditional truck and shovel methods. As the industry becomes increasingly aware of the need for “Sustainable Mining”, the ecological benefits derived from the elimination of dust and reduction of harmful greenhouse emissions caused by truck and shovel methods are self-evident.
“Green” has never been a new word or a passing fad for MMD: one of the global leaders in In-Pit Sizing & Conveying (IPSC) technology, the company have been providing greener and cost-effective solutions for operators worldwide for over 35 years.
IPSC systems are a cost-effective and safer alternative to discontinuous material haulage by dump trucks; reducing operating costs, improving safety, and reducing CO2 emissions, dust, and noise pollution. Employing either fully mobile, semi mobile or static Sizer units in conjunction with conveyors, IPSC efficiently processes and transports material out of the mine.
MMD has been producing Semi-mobile IPSC units since the early 1980s. It is generally fed by a small fleet of trucks transporting material short distances from the mine face. The Sizer unit reduces material in preparation for efficient conveyor haulage out of the mine. As the mining face progresses these units are relocated occasionally to minimise the truck haulage distance.
Features of MMD IPSC
Efficiency and flexibility
Semi mobile sizer units leverage the flexibility of truck haulage together with the efficiency of conveyor haulage. This provides the ideal efficient solution for many mining scenarios where mining flexibility is vital, such as selective mining (blending), heavily faulted seams or irregular shaped ore bodies.
Modular construction
Semi-Mobile units are constructed in easy-to-assemble modules that can be relocated closer to the mine face by the MMD Atlas Transporter.
Reliable
Through the use of the well-established components such as the twin shaft Sizer and heavy duty apron plate feeder, MMD Semi Mobile units deliver the reliability and robustness required for IPSC operations.
More features
• Bespoke solutions designed and optimised to meet mining requirements
• Throughput capacities up to and over 10,000 TPH
• Low carbon emissions and environmental impact by using all electrical power
• Automated material handling
• Maintenance friendly.
After five years’ development, MMD have designed and built the world’s most advanced Fully Mobile Sizer. The rig is the third generation in a series of high-capacity mobile units that eliminate the need for trucks altogether by processing and delivering material onto conveyors. What’s more, ‘Sizing’ is the only breaking system specifically designed for semi or fully mobile installation.
Historically, the very first mobile crushers, commonly used gyratory and jaw crushers, suffered one major drawback: the bulk weight of the equipment made them ‘moveable’ rather than ‘mobile’. The physical size of the crushing equipment (originally designed for static installations) generally resulted in structural constraints for mobile applications. As a result, nearly all of the early mobile crushers became expensive, practically static installations.
Why MMD Sizer?
The operating principles of MMD Twin Shaft Mineral Sizer provide various unique advantages which is inevitable for the green mining solution.
MMD Sizing Technology
The basic concept of the MMD Sizer is the use of two rotors with large teeth, on small diameter shafts, driven at a low speed by a direct high torque drive system. This design produces three major principles which all interact when breaking materials using Sizer Technology. The unique principles are: Three-stage breaking action, Rotating screen effect, and Deep scroll tooth pattern. Here we explain why MMD Sizer needs to be considered for your mining operations.
Accurate sizing
3-stage breaking action.
Rotating screen effects
The interlaced toothed rotor design allows free flowing undersize material to pass through the continuously changing gaps generated by the relatively slow moving shafts.
Deep scroll tooth pattern
The deep scroll conveys the larger material to one end of the machine and helps to spread the feed across the full length of the rotors. This feature can be used to reject oversize material from the machine.
Lower energy consumption
With large teeth and small shaft diameters the material is gripped and broken in shear rather than compression force resulting in much lower energy consumption.
Fines generation
Deep scroll tooth pattern which acts as a rotating screen allowing already undersize material to pass without any further size degradation or power usage. MMD Sizer technology produces the minimum fines.
Handle wet & sticky
MMD Sizer claims to be the only solution to handle wet and sticky with high moisture content in the material. Minimum space requirement Originally Sizer is invented by MMD Founder Mr. Alan Potts to facilitate British underground coal mines where space was a constraint. The machine is very compact and requires minimum space to install.
Minimum downtime
MMD Sizer requires minimum downtime, the complete one set of wear components can be replaced within one to two shifts of same day. This minimum downtime increases productivity significantly.
Support steel structures for gearboxes
All gearboxes are mounted to the sizer itself resulting in correct alignment at all times and not requiring a support frame or separate structure. MMD Heavy Duty Gearbox specially designed to facilitate MMD Sizer only. On twin drive machine the gearboxes are mounted on the same end of the sizer allowing inline or perpendicular installation without restricting maintenance access to drives.
Scroll pattern
MMD Sizer is having the unique scroll pattern. The deep scroll tooth pattern which acts as a rotating screen allowing already undersize material to pass without any further size degradation or power usage. The scroll pattern can also be utilised to move the material in a particular direction i.e. away from the infeed point to allow larger lumps to be broken without obstructing the material flow, to spread the material evenly over the full length of the Sizer maximising capacity, or to push oversize lumps towards the end of the machine where the oversize can be rejected. MMD Sizer has Automatic Reject Facility.
Machine vibration
Because the shafts rotate at low speeds, the vibration is minimal and contained within the sizer case.
Easy maintenance
• Sizer can be mounted on wheel carriages for easy maintenance.
• Gearbox oil needs to be changed after 06 months or 1,500 operating hours whichever is earlier.
• Fluid coupling oil requires to be changed around after one year.
• Lesser height of machine will enable service engineer to do the periodic maintenance more comfortably.
• Lesser weight of the heaviest component will optimise in selection of the lifting equipment such as EOT crane, hoists etc.Lesser installation cost
• Only levelled & compacted civil bed is required depending on the arrangement.
• Due to lesser height and compact size, minimum headroom is required for maintenance.
• Minimum chute work and no heavy structural steel support is required.
• Hence, minimum man power is required to install the machine.
• Machine installation time is less (within a day) subject to availability of adequate resources.
• No special tools and tackles required during erection and commissioning.
• Operational expenditure is very less
• Electrical consumption is very low.
• Very less spares consumption.
• Consumables requirement is very low.
Authored by_
Subhajit Chaudhuri,
Vice President,
MMD Heavy Machinery (India) Pvt Ltd
Cookie Consent
We use cookies to personalize your experience. By continuing to visit this website you agree to our Terms & Conditions, Privacy Policy and Cookie Policy.