Mobile screening market: a fast moving industry
By Edit Team | May 27, 2014 11:00 am SHARE
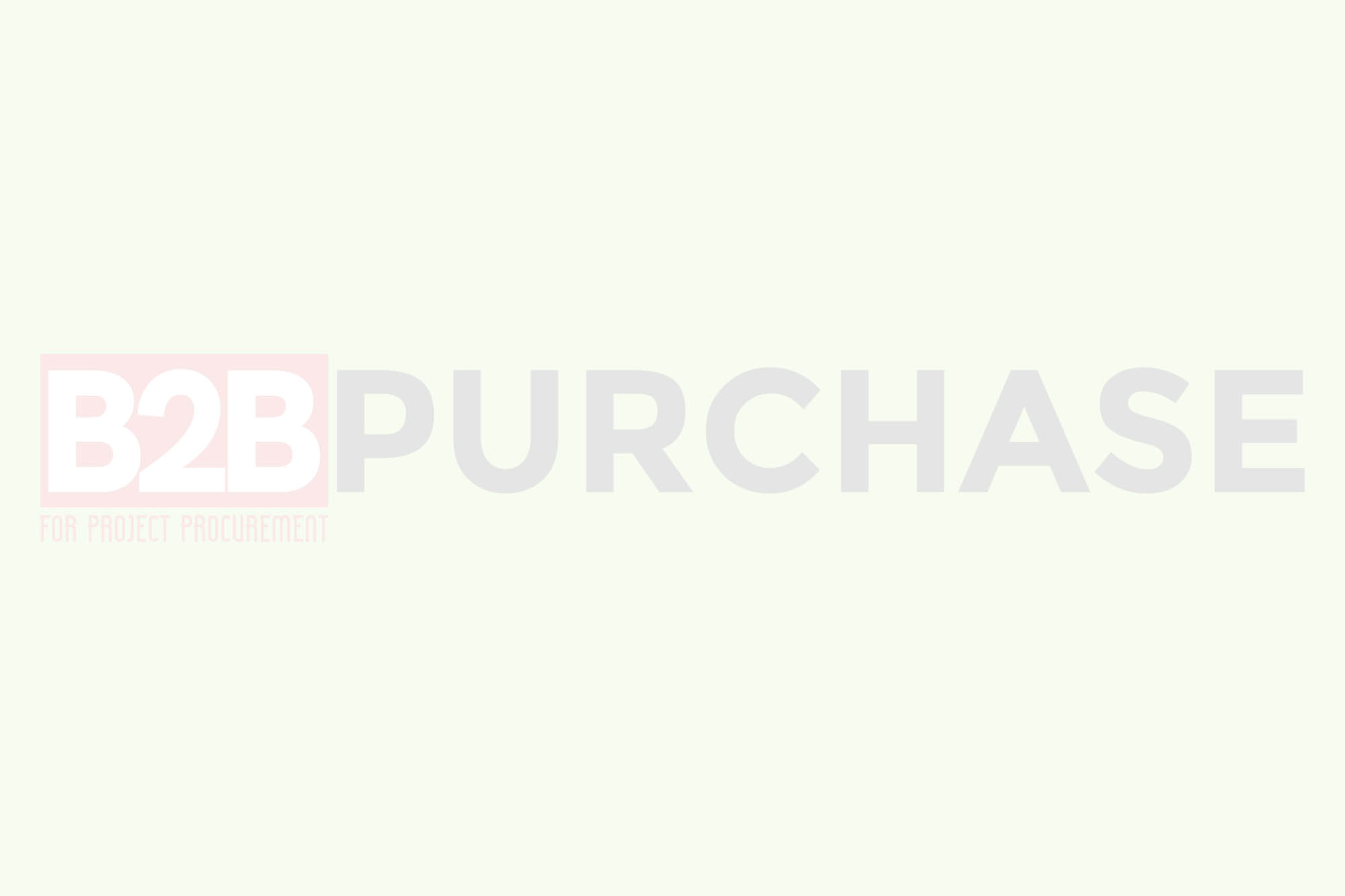
Over the past couple of decades customers have increasing latched on to the real benefits of the tracked mobile concept
Powerscreen offers a comprehensive range of mobile crushing and screening equipment. Its screening portfolio consists of three product ranges of tracked mobile screens: Chieftain incline screens, Warrior heavy-duty inclines, and H-range horizontal screens. These machines are working in many applications around the world ranging from quarry, ores, recycling, compost, topsoil, wood products, sand and gravel.
Current trends and future development
With continuously changing legislation and the specifications for aggregates becoming stringent, the mobile screening market is a fast moving industry. Equipment manufacturers therefore need to be forward thinking, anticipate how the market is moving, and react quickly in developing the right products for the market.
The Mobile Concept
Powerscreen primarily manufactures tracked mobile equipment. Over the past couple of decades customers have increasing latched on to the real benefits of the tracked mobile concept. Key advantages of tracked mobile equipment over static equipment include:
• More compact units
• Better suited to contractors
• Operates close to the quarry face reducing amount of big material needing hauled
• Lower capital depreciation
• No requirement for investment in infrastructure, foundations etc.
Types of Screeners
Scalping screens like the Powerscreen Warrior range are employed to allow small rock particles and fine material that do not require crushing to bypass further crushing stages. In quarry applications a scalping screen is generally used after the primary crusher. Material is passed over a vibrating mesh that allows particles less than a certain size to pass through. This material then bypasses the downstream crusher stages and travels directly to the final sizing screens.
In quarries with difficult to handle material, where clay and excessive moisture is present within the deposit, a Warrior is often used to remove the clay before the mineral is fed into the primary crusher. The material removed at this stage will usually still contain some usable rock and would have been washed to recover the maximum amount of aggregate before being fed into the sizing screens. But with new highly aggressive mobile screens like the Warrior 2400 and soon to be launched Warrior 2100, the requirement to wash material is vastly reduced due to the high reclamation rate made possible through a combination of high ‘g’ force and an elliptical stroke screenbox. This style of machine also offers versatility as the nominal 45 degree line of action can be altered by retiming the gears to give either a flatter angle for a faster rate of material travel, or a steeper angle for longer retention of material on the deck thereby creating a sharper size of product.
Final sizing screens like the Powerscreen Chieftain and H-range of machine use vibrating meshes with specific size apertures to separate oversize material from undersize material. Up to three decks are used in each screen to create several specific sizes of material in a single operation. A train of screens may be used in series so that material that is too coarse for one set of decks is passed onto the next screen allowing a great variety of different sized materials to be sorted. Materials that are too big to fit through any of these screens are sometimes re-circulated back into the secondary or tertiary crusher and may be cycled between the sizing screens and the crusher a number of times. As well as defining the material sizing, this process of material re-circulation also helps create a better shaped product with good cubicity.
How does it work?
So how does a screenbox actually separate material? Well, in general terms an out-of-balance rotating mass creates a vibrating motion of the screenbox structure which in combination with gravity tends to move the material over the mesh deck. This action causes ‘stratification’ which is when large particles rise to the top, and finer material falls to the bottom and is then able to pass through the screen deck.
There are many different types of screen media such as woven wire, welded wire, piano wire, self-cleaning mesh, fingers, grizzlys, punched plate and polyurethane media, to name but a few. To intelligently select the proper size and type of media, specific details of the application are necessary. Defining the right screening set-up is as much an art as it is a science and can be predicted to a certain extent. But with varying factors like moisture content, material gradation, surge potential, particle shape and characteristics; the final performance will only be fully known when the plant is run. When it comes to screening, there is definitely no substitute for experience.
Cookie Consent
We use cookies to personalize your experience. By continuing to visit this website you agree to our Terms & Conditions, Privacy Policy and Cookie Policy.