PEB Airports to fuel India’s aviation growth in the hinterlands
By Edit Team | November 15, 2022 4:00 pm SHARE
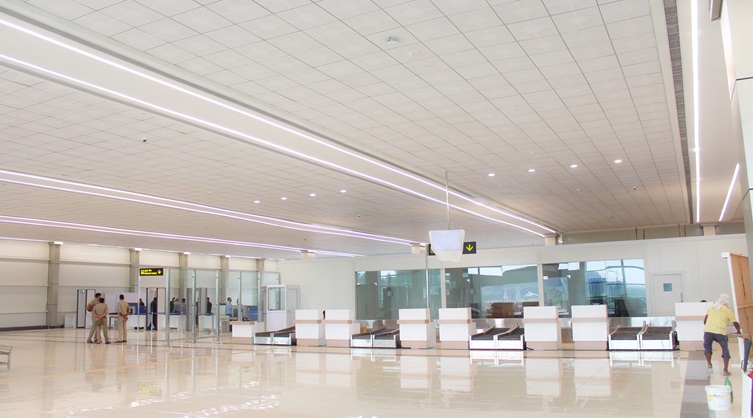
Under the UDAN Scheme, the government has to develop airports in areas with extreme weather conditions, such as the Northeast and Himalayan regions.
The Government of India has placed a strong emphasis on developing new airports as well as expanding and upgrading those that already exist. The government is working to connect tiers 2–3 with air services as part of the ambitious low-cost flying programme known as the UDAN scheme in order to encourage their economic development and facilitate travel. The construction of terminals, hangars, and office buildings is part of this transformation initiative. The wants of common citizens to utilise air travel facilities in the near future, however, appear to be a challenging feat given the length of the time traditional civil development takes and its other limitations.
Prefabricated buildings make it simple to tackle several constraints, notably fulfilling web traffic requirements, the immediate need for space, and comprehending the potential for rapid development. Additionally, tier 2-3 cities’ restricted access to resources, particularly machinery, makes heavy building there a little bit more challenging. The major players in this predicament will need to examine how to overcome the inadequacies of conventional civil construction techniques. Prefabricated buildings come into play as a solution in this scenario, and their implementation is now imperative.
Building enclosures and structural frames
The construction duration, which has been a major obstacle in the way of the UDAN Scheme, may be diminished significantly with the use of factory-made enclosure structures that include structural frames, a roof, and wall support. The factory serves as the primary location for the creation of these structures. Thereafter, the parts are hauled to the site and soldered together. This illustrates how straightforward the construction phase is and has the potential to accelerate the pace at which new airport facilities are erected.
Traditional construction, on the other hand, necessitates halting a portion of the process, which is inconvenient for commuters. Additionally, there are occasions when construction labourers must halt working. These circumstances either result in a delay in the project’s delivery or a cessation of all flying activities. Prefabricated buildings dramatically change the situation. The provision of additional space has no impact on the airport’s aviation operations because these structures are constructed off-site.
Innovating existing airports with prefabricated structures
Furthermore, these modular structures give airport administrations the ability to establish ad hoc spaces and accommodate unforeseen demands. A temporary area made of prefabricated materials might be a great alternative for remodelling or renovating existing airports or terminals. These designs are versatile and customised to order, so they may provide a solution for just about any circumstance. These structures can help the ATC ensure smooth flight operations in addition to addressing space needs in this way.
Dealing with the cost complications
Cost is yet another significant element that presents challenges for the stakeholders. Since the projects require a substantial amount of money to be fully functional, the cost of building or refurbishment is a factor investor are always apprehensive about. Prefabricated buildings are an option that can assist in reducing expenses in this area as well. As opposed to traditional construction, these prefabricated structures don’t need to be built from scratch on the job site. They considerably cut expenditures as a result. They are also a financially viable alternative to conventional buildings because they are long-lasting and require little to no upkeep.
Addressing geographical uncertainties
The UDAN Scheme requires the government to build airports in a variety of harsh weather areas, including the Northeast and Himalayan regions. Prefabricated designs are also quite suitable for such climates. They can survive extreme weather conditions such as heavy rain, wind, and snow. In addition, these structures can withstand considerable earth vibration and are resistant to earthquakes.
Most significantly, they are green building designs. The construction materials used can be recycled and repurposed. The efforts of the relevant stakeholders in environmental safety may be aided by these aspects. They can also provide a safe atmosphere for commuters, something that is impossible with conventional building techniques since they generate dust.
The airport infrastructure needs quick, dependable, and environmentally friendly development solutions since the government is eager to remake flying simple and economical to improve the ease of travel in Tier 2–3 cities. Only with such architecture can a pleasant and hassle-free travel experience be guaranteed. The greatest alternative to traditional construction and the best way to satisfy public demand is to use modular, prefabricated building technologies. The UDAN Scheme’s goal will be more straightforward to accomplish within the allotted period with its aid. To accelerate airport development in line with “New India,” the stakeholders must examine the potential of these construction solutions and maximise their benefits from them.
(This article has been authored by Nikhil Bothra, Director, Epack Group)
Cookie Consent
We use cookies to personalize your experience. By continuing to visit this website you agree to our Terms & Conditions, Privacy Policy and Cookie Policy.