PEB is a choice for sustainable and eco-friendly construction
By Edit Team | January 9, 2021 1:20 pm SHARE
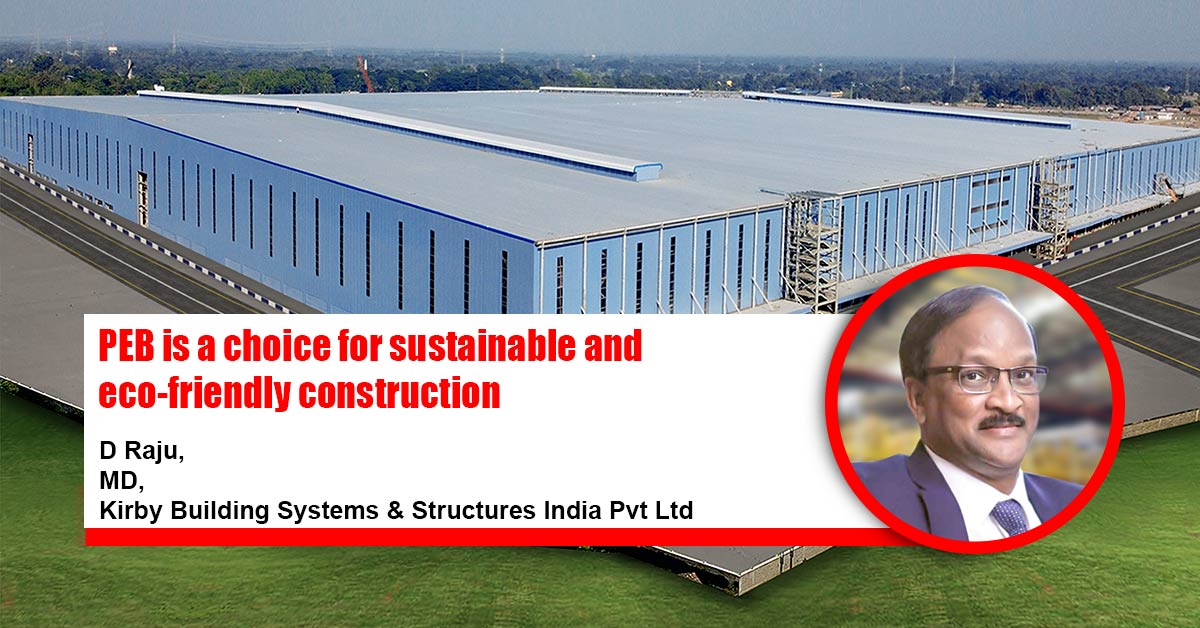
As steel is 100 per cent recyclable and can be reused for making other products again and again when compared to conventional buildings, says D Raju – MD, Kirby Building Systems & Structures India Pvt Ltd.
As another year sets in, what changes are you anticipating in the PEB market?
The construction and infrastructure sector is a vital sector of the Indian economy. Owing to the pandemic, it is facing a shortage of manpower besides which their order books too had weakened owing to projects getting stalled. In the last 3 to 4 months the economy has entered into a revival mode and at this crucial juncture, many companies are looking at pre-fabricated steel construction as it require the use of fewer labourers at the job sites. Accordingly, many other changes are being witnessed in PEB right across all the stages of project life cycle such as design, fabrication and erection, thereby creating new trends in the PEB industry. Some of the other trends include issuing of more number of tenders by private, public and government to go for prefab steel construction thereby increasing the market potential of the industry and also promoting the industry across new target audience. In recent years, affordable housing and airport buildings are also giving preference to prefab steel construction. With the economy opening up slowly, in the short term only some sectors are likely to witness positive growth. However, in the long term, over the next 2-3 years, the market will remain positive and a pre Covid-19 era growth is likely to come back.
Looking at the cost index, how PEB buildings are cost-efficient and energy-efficient vs conventional buildings?
PEB is one of the choices when it comes to sustainable and eco-friendly construction as steel is 100 per cent recyclable and can be re-used for making other products again and again when compared to conventional buildings. PEBs use simple nut and bolt connection for installation of sections which are transported from the factory as per the customer’s requirement and erected as per the standard procedures with world class safety protocols. All the sections of PEB are light weight, quicker design and detailing, factory fabricated with quality control, faster completion, future expansion and easily transportable when compared to conventional buildings. These building are also referred to as green buildings which have caught the attention of many builders, developers etc. across India and is making inroads across all types of construction. These buildings are cost effective, energy efficient and provide better quality environment as they are cooler in hot conditions due to the use of specific roofing materials, suitable insulation and natural ventilation. The use of skylights and solar panels mounted on rooftops of industrial buildings also meet daylight and captive power requirements which reduce the dependence on power supply from other sources and at the same time reduce emissions and gain carbon credits under clean development mechanism. Effective usage of insulation material, louvers and other materials also help in temperature control and rain water harvesting. This leads to a viable construction methodology which offers all the green benefits, dry construction, saving of natural resources etc. using environmentally friendly materials.
Which sectors you feel will define the market for PEB in the year 2021?
E-commerce and warehousing are playing a major role for the PEB industry in the ongoing Covid-19 pandemic. They are one of the major sectors generating demand for the pre-engineered steel buildings (PEB). Other sectors which are expected to drive demand for PEB include Fast Moving Consumer Goods (FMCG), agro related, defense, packaging, data centers etc. Kirby India has already ventured into construction of commercial buildings either completely in steel or composite form which is slowly being accepted by builders and developers as being witnessed in major cities across India. The company has already executed some high-rise buildings for commercial and residential segments and is currently executing over G+20 floors commercial office buildings and many more are in the pipeline. However, residential segment is yet to see the use of PEB as this will take some more years before it is fully adopted though some buildings have come up across cities using steel construction.
How are you channelizing the growth and adoption of indigenous technologies in your PEB products?
In the early 2000, warehouses were the initial driver for PEB but over the last two decades PEB has ventured into many other applications for different industry segments. Kirby India has grown manifolds over the last two decades executing simple box like buildings for warehouses to very complex industrial buildings to high rise-structures. The company is now adapting new innovative methods across design, fabrication and construction which has widened their scope of operations thereby continuously implementing newer ways of providing delightful experience to our customers. The value chain for any project in construction and infrastructure sectors consists of many components within different stages of the project lifecycle — pre-sales, design estimation, order processing, project planning and scheduling, drafting, material and inventory planning, procurement, production, quality check, supply, delivery, material inspection at site and construction. Kirby India is the first PEB company in India to integrate all its processes involved in a project lifecycle in SAP system with heavy customization as per our requirement thereby providing value to the customers. Kirby with its rich experience and a diverse project portfolio of over 25,000 diverse buildings for different industry segments across India, over the last two decades has consistently evolved and adapted newer types of construction methodologies to ensure projects are completed on time in a faster and a safer way.
Cookie Consent
We use cookies to personalize your experience. By continuing to visit this website you agree to our Terms & Conditions, Privacy Policy and Cookie Policy.