PEBS Pennar built 1 km long PEB warehouse for OPaL
By Edit Team | May 18, 2016 11:08 am SHARE
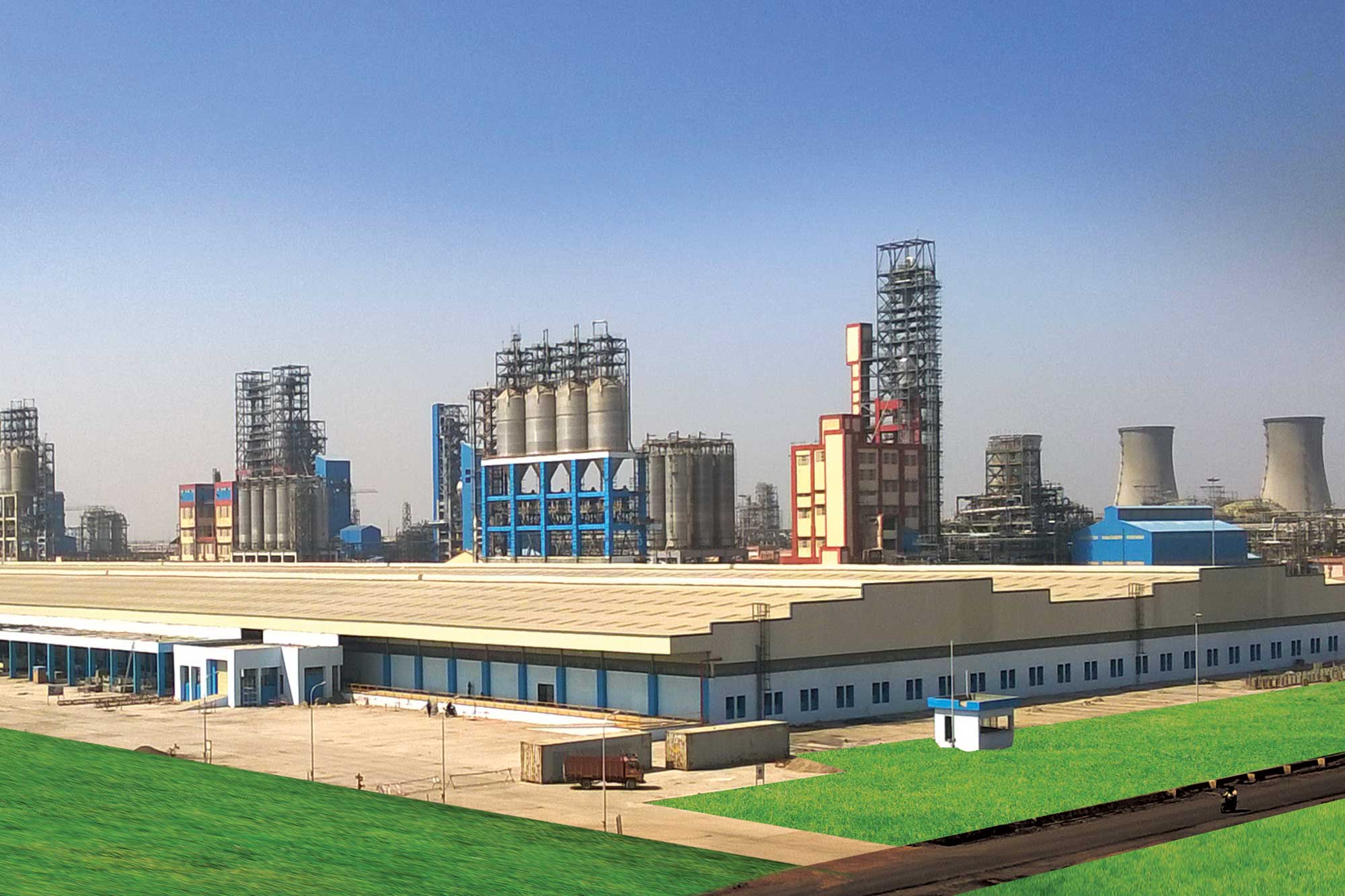
Pennar Engineered Building Systems Ltd. (PEBS Pennar), an ISO 9001:2008 certified company which is into design, manufacture, supply and installation of cost-effective pre-engineered steel buildings and building components for industries, warehouses, commercial centres, multi-storey buildings, aircraft hangars, defence installations and sports stadia has recently completed one of India’s longest PEB warehouse for ONGC Petro additions Ltd (OPaL) at Dahej, Gujarat.
The warehouse was conceptualised by IOT Infra and Engineers India Ltd to meet the massive storage requirement for ONGC. The building is 1 km long and 135 metres wide covering an area of 1,40,000 sq. metres. The design, fabrication and installation of the building were undertaken by Pennar Engineered Building Systems Ltd.
The building was designed with unsymmetrical frames where silo frames were considered with rafters resting on the RCC building. The building is the widest multi-gable building ever done by PEBS Pennar. Structure was designed with continuous jack portal where 24 metres jack-beams were used as the portal to make column less space inside the building as the customer required free end space of 135 metres by 24 metres along the length of the building.
The complete design was vetted by EIL (Engineers India Ltd), which had given the approval for the design after being satisfied with the codes and the design methodology adopted by PEBS Pennar. Star columns were used at every expansion joints in order to maintain portal stability and economics in longitudinal and transverse direction.
In addition to space restriction, the clear height had to be maintained along valley time to facilitate the movement of machineries and vehicles. Complete building was installed with Double Lok roofing system with 10 years of leak proof warranty.
Structural elements
The basic structural system consisted of main frames with secondary members provided between these frames for sheeting support. The columns and rafters of the building were of varying web depth with a maximum web depth of 1,000 mm. The rafters were resting on jack beams at interior of the building. These jack beams were spanning 24 metres and were for full length of the building at five locations, maximum web depth of the jack beam was 1,400 metres. The secondary members were cold formed “Z” or “C” sections varying in thickness and of maximum thickness of 2.5 mm.
Structural uniqueness
The project was unique and challenging in respect to both design as well as installation. Stability was the major concern with collateral load of dust, wind, speed and seismic load. There lies enormous efforts and toil of the entire team of engineers behind the approval of the project. Fabrication and transportation of huge structures was an exceptional task as it was not possible to carryout welding onsite. Apart from this, the biggest challenge was to gather and maintain a huge task force of skilled workers together and to maintain the momentum at project site all the time.
Steel specifications
The built up “I” sections and jack beams were fabricated from plates of ASTM with minimum yield strength of 345 mpa. The secondary members were from ASTM A 653 metres with minimum yield strength of 345 mpa. Other hot rolled sections used were angles, rods etc which was of IS 2062 with minimum yield strength of 240 mpa.
Challenges
Huge volume in terms of area of work was one of the major challenges for execution of the project. The whole project had to be handed over within a span of 8 months. Deploying multiple teams, resources and mobilising sufficient manpower and working in extended period of work was the ultimate confront for this project which the company came up with.
Safety
PEBS Pennar took special care about the project and manpower such that they were in safe hands, claims the company. Safety screening of deployed manpower, imparting onsite safety training, job safety analysis of individual work methods, safety gears like full body harness for workers on height, using safe access methods like boom-lifts, man-basket etc, was followed for safety.
Workmanship
• Supply of 5,000 tonnes fabricated structural steel completed in 120 days
• Completed installation of whole project in 8 working months
• Approximately 200-250 workers per day
• Total project management effort : 24 man-months.
Cookie Consent
We use cookies to personalize your experience. By continuing to visit this website you agree to our Terms & Conditions, Privacy Policy and Cookie Policy.