Perlcon GIB: Aggregate for lightweight concrete
By Edit Team | December 27, 2016 12:20 pm SHARE
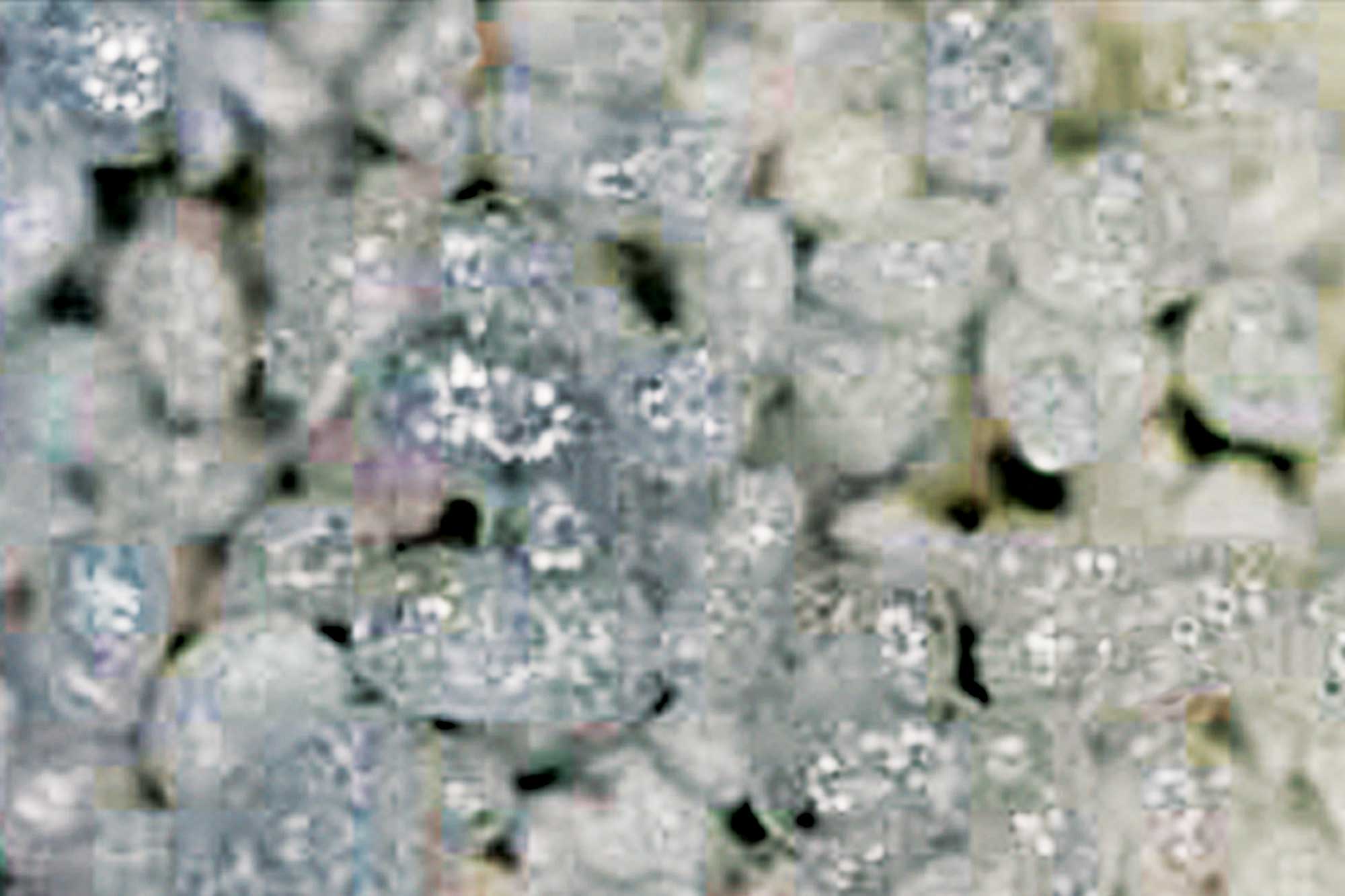
Glazed Iso Ball (GIB) claims to be the lightest aggregate having density from 100 kg/cu.m. – 250 kg/cu.m. This material, white or light grey in colour, is about 1/10 the weight of sand or gravel.
The specially processed GIB aggregate consists of expanded particles for use in lightweight concrete, fire retardant plaster or insulating concrete as replacement of sand or gravel or in combination with sand/gravel.
For easy handling and accurate on-the-job mixing, it is usually marketed in HDPE bags, ready for use with cement or gypsum. The many, tiny glass-sealed cells in each particle of expanded GIB make it highly insulating as well as comparatively non-absorptive. Thus GIB mixes with about 30 per cent less water than comparable lightweight aggregates.
Following advantages of GIB result in saving of time, labour and materials:
Lightweight: GIB in combination with Portland cement is the lightest of all mineral aggregate concretes. By use of light weight aggregate – GIB, concrete up to 500 kg/cu.m. can be designed thus greatly reducing the deadweight of floor, roof and wall constructions.
Fire retardant: Light weight concrete with Perlcon GIB is incombustible and has received 3-hour ratings in fire tests. It is ideal for fire-retardant roof and floor fills, for thin concrete curtain walls and for precast panel and block constructions where insulation and fire resistance is required.
Insulating: Countless tiny air cells in GIB aggregate produce concrete with an insulating value up to 20 times better than ordinary concrete. The company claims, a 2-inch thickness of Light Weight concrete with GIB provides U value of 2.78/inch thickness and is entirely inorganic—not subject to damage by water, vermin or fungus and doesn’t catch fire.
Workable: Light weight concrete with GIB can be job-mixed or transit mixed, and then poured, pumped, or plastered into place. Its light weight simplifies handling, speeds construction and reduces cost of placement. The dry concrete can be nailed, sawed
and worked with ordinary carpentry tools.
Specifications:
Recommendations
• For lightweight insulating GIB concrete, the proper mix proportions can be designed on the basis of desired compressive strength, thermal conductivity or other physical properties.
• For insulating roof fills and short span structural roof decks, normally 450-500 kg/cu.m. concrete is recommended and 500-600 kg/cu.m. density concrete for floor fills and short span lightweight floors.
Materials
• Cement shall be Ordinary Portland cement meeting the requirements of ASTM Specification C-150/ IS Specifications.
• Aggregate shall meet the sieve analysis specifications for lightweight Type ‘‘A’’ concrete aggregate and shall have a loose density of 120-190 kg/m3 when measured by the shovelling procedure of ASTM C-29.
• Air entraining admixture can be added if required.
• Water shall be clear and free from oil, acid, alkali, organic matter or other deleterious substances, preferably potable.
Mixing
Concrete with GIB shall be mixed in a paddle type plaster machine or a drum type concrete mixer. The required amount of water, air entraining admixture and Portland cement shall be placed in the mixer and shall be mixed until slurry is formed.
The proper quantity of GIB aggregate shall then be added to the slurry and all materials mixed until desired wet density is reached. Mixing should be slow and for a short period just enough to ensure all is mixed.
Placing
• GIB concrete shall be carefully deposited and laid as screed in a continuous operation until a panel or section is completed. Steel trowelling shall be avoided. Rodding, tamping and vibrating shall not be used unless so specified by the architect.
• Expansion joints as per specification at each 30 m transverse length.
Curing
Light weight concrete shall be protected for at least the first three days in accordance with good job practice to keep it from drying too rapidly or freezing. Freshly poured concrete shall be given adequate protection against damage by heavy rain. No traffic shall be allowed until concrete can sustain a man’s weight without indentation.
For roof deck use, concrete shall cure at least 5 to 7 days before placing of the built-sip roof. If rain occurs at the end of the curing period, 1 to 2 additional days must be allowed before the built-up roof is placed.
Cookie Consent
We use cookies to personalize your experience. By continuing to visit this website you agree to our Terms & Conditions, Privacy Policy and Cookie Policy.