Plant Prefab completes new prefabricated residence in Palo Alto
By Edit Team | October 23, 2019 6:12 am SHARE
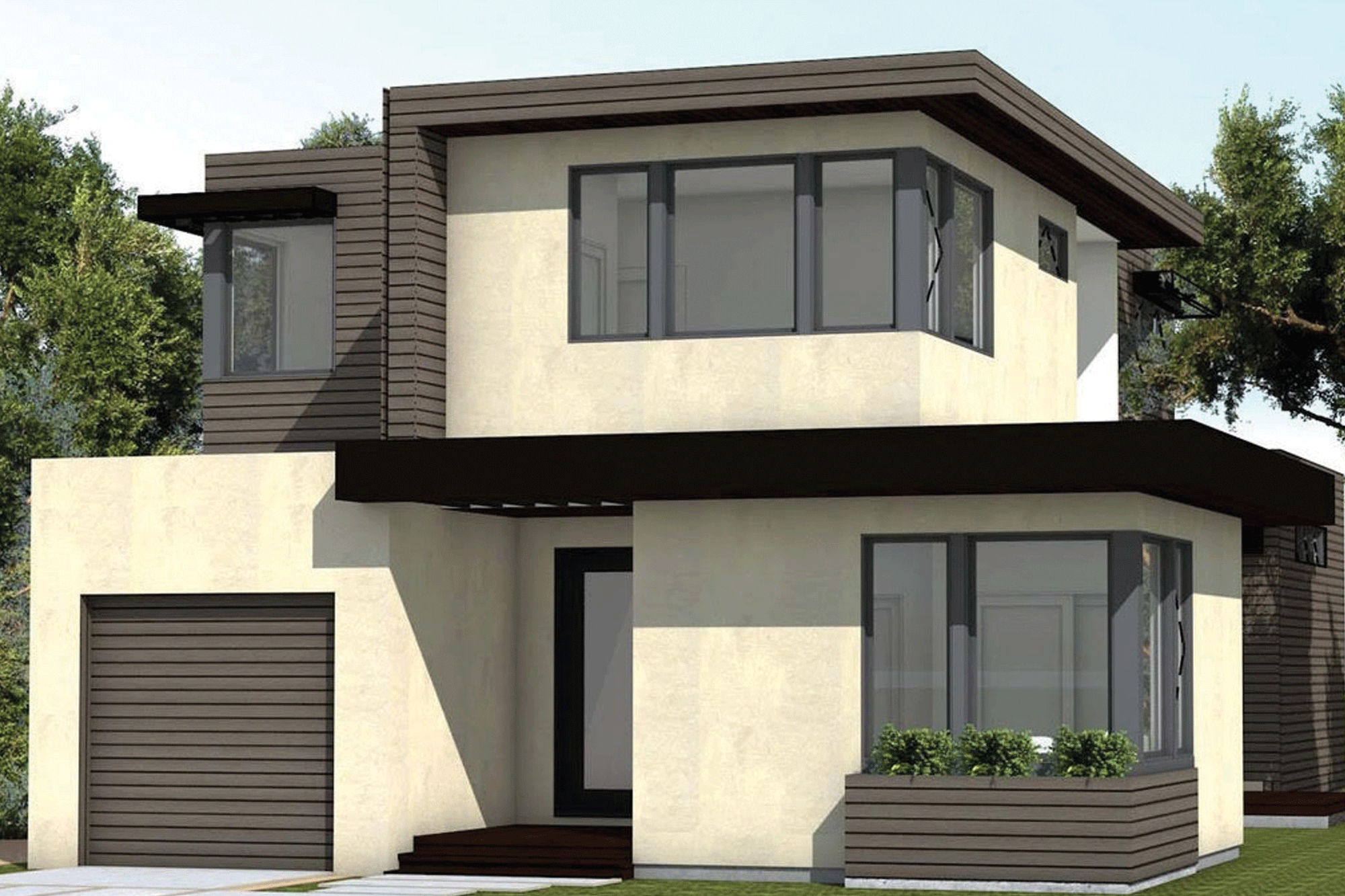
P lant Prefab, a leading custom home design and prefabrication company, installed a residential project in Palo Alto, highlighting a building system that allows the construction of custom homes faster with less cost and construction waste than similar site-built homes.
The collaboration between to by long design and Plant Prefab is a 2,371 square feet, 4 bedroom, 3 bath residence on Waverley Street near Palo Alto’s midtown. It is a compact design that maintains a sense of openness on the first floor with tall ceilings in the stairwell and living room, utilizing large windows and sliding glass walls to prioritise natural light and access to outdoor living areas. The building is heated by radiant flooring and features thermally broken aluminium windows in combination with a high value insulation at the walls and roof to create an energy efficient envelope. The exterior materials include wood siding over a rain screen which wraps the building, adding texture between smooth stucco walls. Installed in only eight hours, the home replaced the outdated house on the property. Recent data indicates that median home prices in Palo Alto hit an all-time high of $2.7 million last year, with tight supply and strong demand being the main drivers.
According to Steve Glenn, founder and CEO of Plant Prefab, people hoping to live in Palo Alto or surrounding areas crave high-quality homes that are healthy, energy efficient, use sustainable building materials and are of the highest quality, but the available supply of construction companies in the Bay area to build these homes is constrained and expensive. “Plant Prefab is the first company focused on building extremely high quality, custom, sustainable homes based on plans clients develop with their own architects or that they select from our architect partners,” Glenn said. “By building off-site in parallel to the site work and in a controlled, all weather facility, we reduce the construction schedule by 50 percent or more versus a tradition site-based construction process — and we dramatically reduce the noise and disruption to our client’s neighbours.”
Cookie Consent
We use cookies to personalize your experience. By continuing to visit this website you agree to our Terms & Conditions, Privacy Policy and Cookie Policy.