Pre-engineered buildings with steel structures are the future
By Edit Team | October 30, 2021 7:15 pm SHARE
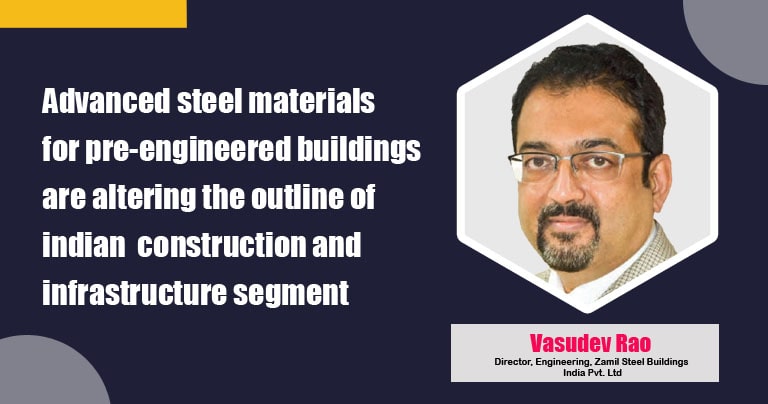
How is digitalisation impacting the design, flexibility and sustainability of Pre-engineered buildings?
Normally in any pre-engineered building, engineering, design and detailing are the two main aspects. Design being the first aspect, is the backstay based on the number of designs and other things are detailed into, and before further taking up for production.
So, earlier designs have had manual calculations, as we did not have modern digitised tools and systems, available for engineering; but today from design point of view, digitalisation has reduced our design cycle time. Like I said, earlier the manual process required more time and resources, whereas, currently you don’t need so many resources, and the time consumption has reduced when compared to the standard software that does the designing very fast.
Second aspect is, there are disadvantages of manual calculation – like handwritten & legibility issues, which usually differs from person to person; another one is continuous manual intervention resulting in a lot of errors; so, we had to have a checker who would keep a tab on all the designs and everything.
Today, due to digitalisation and related software, these concerns have been reduced to almost nil. Also, we see schedule improvisation, as there is a seamless flow of data, and with the help of digitalisation there is a shorter schedule unlike earlier one.
Third aspect is accuracy and quality; digitalisation helps us faster, accurate and efficient designs, and fourth one is efficient change management; suppose I completed a design and there are certain changes, earlier we used to note everything manually for work but with digitalisation you need to give inputs for the required changes, which further will provide the desired output quickly.
Talking about flexibility, today you can visualise, integrate and stimulate any project. This is a huge advantage attained by digitalisation of designs. Also, we have flexibility in the design models. Suppose we can’t have personal meetings with clients to explain our designs, we will create a model/sketch and will share to them; and in case client want changes they can be directly added and share the updated design/sketch. Last critical part is documentation. I have seen both phases of pre digitalisation, and current digitalisation. Earlier, we used to preserve hard copies of designs, drawing and everything and store them to our record room which was bigger than our office. Then came the microfilming aspect, where every document was microfilmed and stored. Whereas, presently you don’t need any such things, as with digitalisation, all the data can be easily stored and protected through cloud storage. So, these are the impacts that digitalisation has on design, flexibility and sustainability of PEB.
What are the various criteria’s that impacts the selection of steel products for PEB solutions?
When we talk about criteria for PEB, the first and the basic aspect involved is the project cost, and the second aspect is the construction time, which means, the required time to execute and complete the project.
For instance, a metro project is taking over 3 years of completion because it’s being constructed with more RCC than steel. RCC construction consumes more time for project completion, as that’s the standard construction time required for an RCC project. If I use steel products and make it pre-engineered, where they send their inputs for architecture too, based on those details we create designs and drawings, and make components/products based on steel products by choosing the right steel that fits best for the metro and other public interfaces. We just don’t pick and choose any steel, since such public structures require tubular steel similar to the ones in airport for aestheticity. I will use that kind of steel, fabricate it and then ship it. When fabricated steel reaches to the project site, it can be installed within a week, with the help of nut and bolt connections.
RCC would take minimum 3 years to complete, whereas if steel is used, it can commence and complete this project in three months, including the colourful sheets that add to the project’s aesthetics.
Next comes the energy efficiency. In RCC buildings, we have to make various provisions and other additional settings to have energy efficiency, whereas, in steel products you can simply place a solar panel on the top, which can be taken care of while selecting the steel products.
Next is the maintenance, Steel once painted and installed, doesn’t require much longer maintenance, but just regular periodic inspection. Also, you can make modifications to the steel products as they are very flexible.
Another aspect is appearance; you can give any shape to steel products of a pre-engineered building. PEB is also weather resilient, as they can withstand even critical weather conditions.
From an environmental point of view, RCC buildings are more dependent on natural resources like sand, aggregates, cement and others, whereas, steel has always been recyclable and environmental friendly and doesn’t release any pollution.
How do you see PEB becoming commercially viable for large buildings or tall buildings?
When look at situation back in 1920’s, since then steel was used due to its design, ductility, flexibility and other essential aspects. But we were in a different stage during those times back then since adoption was for proven methodology only. So RCC, stone and bricks were the chosen options. Even the public buildings were government controlled, as they looked upon for public safety irrespective of the cost. Trend is no more the same, as private organisations have come into the picture with latest technology. Today, everyone is cost conscious and want their projects to be efficient and sustainable, hence PEB becomes commercially viable as it can be commenced and completed at a shorter schedule. If you go for a usual construction process which consumes more than 6 years for project completion, will become uneconomical. So, steel construction’s speed, economy and the sustainability has less dependence on natural resources. This is why PEB has become very much viable today for big or tall buildings.
What kind of chemicals and coatings helped the PEB structure to last longer even in a corrosive environment?
Any structure, whether RCC or structural steel needs maintenance, and must be protected in any corrosive elements which can be done through various chemicals and coatings. But when it comes to steel you’ve got a large variety of materials available; like, epoxy coating, intumescent coatings, polymers, ceramic, PTSE, among the others that prevents and longer life of a PEB structure in any corrosive environment.
Which latest technologies have you been implementing to attend design precision in your in the PEB structure and the projects?
Earlier, we had in-house developed limited software tools used to make multiple designs, whereas, today we have so many commercially available software for the designs.
Every country has their own common commercial available software, so these are bought and validated for use in designs. Also we use CAD/CAM for drawings. We have latest software for precision connections also needed in designs of connections, as they are crucial part of any steel building. Thus buying such software from various resources to create an interconnection between all the design engineering aspects for further validation and to combine all these different software.
Hence, for this part, we have developed own automation tools, where we can do the project design, connection design, detailing to provide a quality output within a short span of three weeks. All these things are possible due to automation and in-house technologies. Since I have to present all project aspects to my customer in short time, these technologies allow me to create 3D models of design and structures for their reference.
If you are considering the selection of a particular aspect of a project, I think, since majority of the buildings has to have large spans for multiple use, PEB is the only solution; especially with steel materials as they are highly flexible, and is the only future. It’s always suggested to have PEB with steel structures, rather than conventional costly constructions.
Cookie Consent
We use cookies to personalize your experience. By continuing to visit this website you agree to our Terms & Conditions, Privacy Policy and Cookie Policy.