Precast technology offers a full range of turnkey services
By Edit Team | May 17, 2023 5:32 pm SHARE
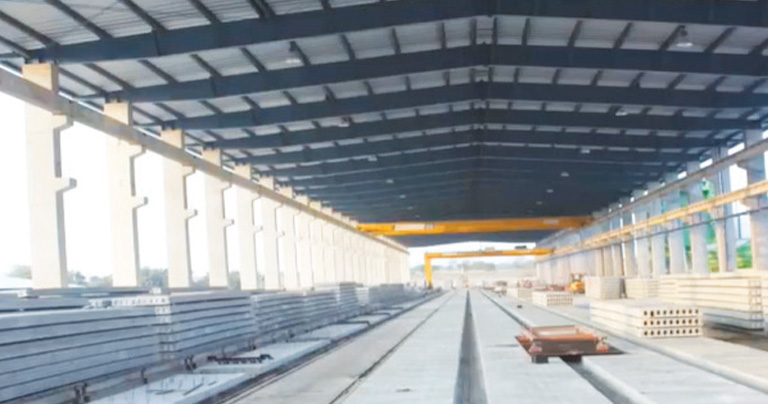
This article highlights the different aspects of precast technology and its usage in various infrastructure projects.
Precast Construction Technology consists of various precast elements such as walls, beams, slabs, columns, staircase, landing and some customised elements that are standardised and designed for stability, durability and structural integrity of the building.
Design, strategic yard planning, lifting, handling, and shipping of precast pieces are all required during the construction of a precast residential structure. This method is appropriate for the construction of tall structures that can withstand lateral stresses caused by seismic activity and wind as well as gravity loads. The building’s framework is designed to allow for the greatest possible number of mould repetitions.
According to Sridhara CN, Associate Director-Technical and Marketing, Preca Solutions India Ptd. Ltd precast construction is always preferable because hundreds of labourers’ energy would be needed if you cast a slab. Therefore, precast technology can eliminate the need for wooden pole supports, metal jacks, and other materials. Instead of hiring self-employed workers to build the site, precast technology allows eight to ten employees to complete the same amount of work with just one crew. A multi-story structure with 30 to 60 floors must be physically moved from the lowest level to the upper level, floor by floor, to create a block wall. If the wall is precast, they will capture the entire wall in the factory, deliver it, and work on the site. This will happen with ease in the construction sector.
Functional areas where precast elements are used and have proven to be an effective solution in executing large-scale projects include roads, seaports, bridges, airports, etc.
When developing safety control, the safety department faces significant challenges. In precast, a limited amount of labour is needed, making it simple to regulate them. In terms of quality, all of the buildings’ caches or whatever damage we need to repair with plastering and finishing. There is no need for plastic in precast once it has been produced and directed; it is then ready for painting with putty and paint. Precast is also superior since staircases are included to allow for simple access to the floors.
Precast items are all environmentally friendly goods, and the procedure makes it easier to conserve energy and prevent environmental effects. Due to the sheer amount of pollution we produce and the precast technology’s adaptability, we may use it in any industry where we use steel or concrete in current construction without any procedural limitations.
Precast technology offers a full range of turnkey services, from casting to building assembly and completion. The structural analysis and design of precast building structures will adopt the requirements specified in the National Building Code, local regulations, and relevant Indian Standard Codes (latest revisions) listed herein. It will include all the designs’ production specifications, finishes, and PMCs. The all-Indian curriculum is commonly used for precast sector design and construction. More significantly, the PCA handbook, in particular, is one we can use because it is equivalent to our national building code in every chapter and discusses precast units chapter by chapter. They explain precast units in the PCA handbooks in great detail. Turnkey engineering solutions for civil structures from design to delivery, from casting to erecting and finishing.
Cookie Consent
We use cookies to personalize your experience. By continuing to visit this website you agree to our Terms & Conditions, Privacy Policy and Cookie Policy.