Raising the bar of durability in heavy-duty infrastructure with SNTP ISI Mark Reinforcement Couplers
By Staff Report | October 24, 2024 2:39 pm SHARE
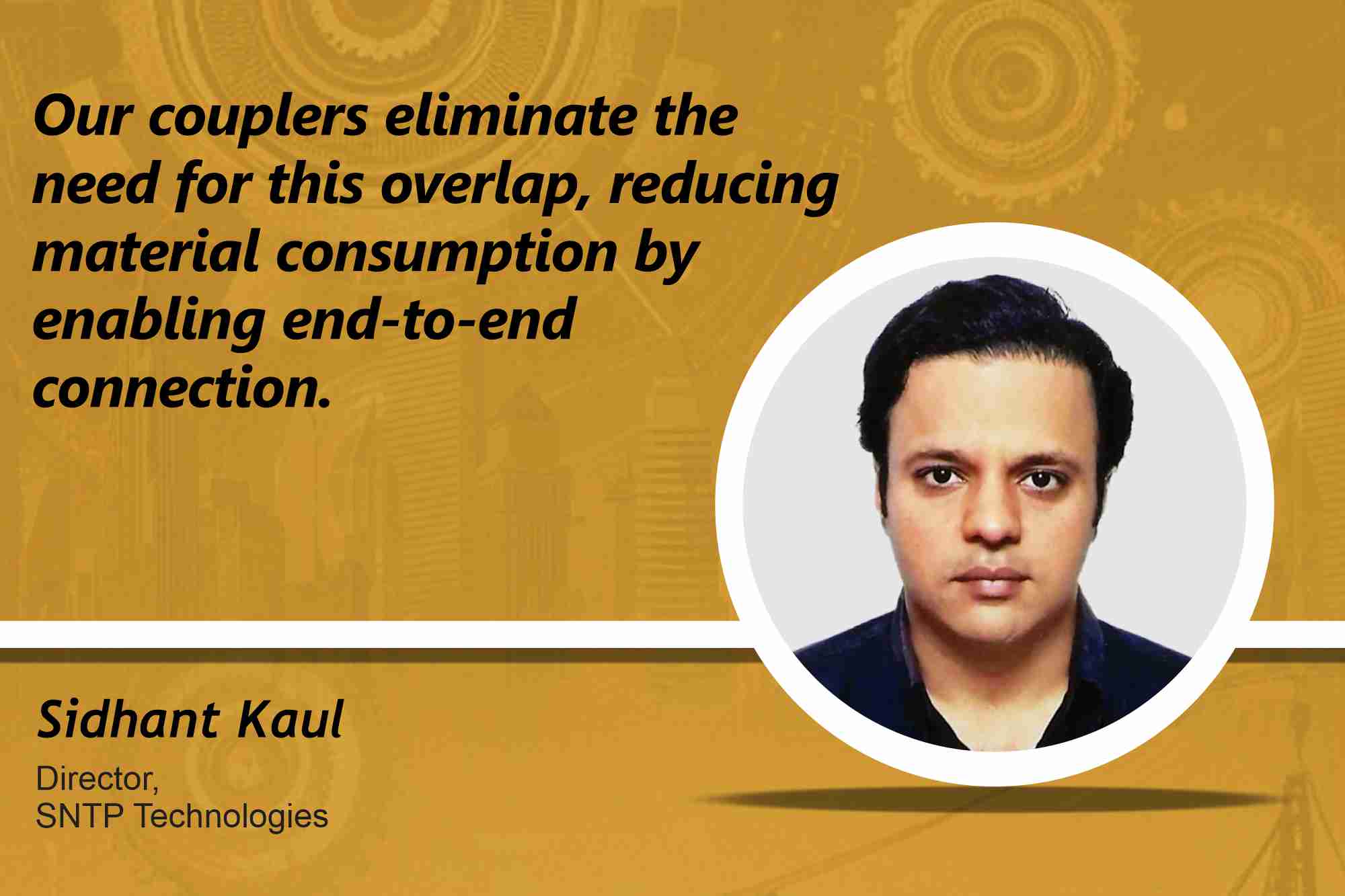
SNTP Technologies, India’s pioneering firm in achieving India’s first and only ISI Mark License for Reinforcement Couplers, is reshaping the construction landscape by enhancing resource efficiency and minimising steel wastage in large-scale projects.
As India’s first and only company to receive ISI Mark certification for rebar couplers, how have you leveraged this distinction to reduce steel wastage and enhance resource efficiency in large-scale construction projects? Additionally, why is BIS certification critical for ensuring quality and safety in such projects?
As India’s first and only company to receive ISI Mark certification for rebar couplers, we have set a new benchmark in the construction industry. The ISI Mark, awarded by the Bureau of Indian Standards (BIS), ensures that our couplers meet the highest quality, safety, and reliability standards per the IS 16172:2023 code. This certification is critical for large-scale projects where structural integrity is paramount. With our ISI Mark Rebar Couplers, we have significantly reduced steel wastage by eliminating the traditional need for overlapping bars, which consume more steel. BIS certification is crucial because it guarantees that every coupler we produce undergoes rigorous testing, ensuring durability and compliance with national safety standards. In an industry where safety is non-negotiable, the ISI Mark gives project developers and engineers the confidence that our couplers will perform under high-stress conditions, ultimately contributing to their projects’ overall efficiency and safety.
The key benefits of using our couplers include the minimisation of overlapping steel. Traditional methods of splicing rebars involve overlapping bars and increasing steel use. Our couplers eliminate the need for this overlap, reducing material consumption by enabling end-to-end connection. Additionally, precise steel utilisation is achieved with our couplers, allowing rebar to be cut to exact lengths and minimising waste from excess cutting. This ensures efficient use of steel resources, particularly in projects where precise lengths are critical. Furthermore, the reduction in labour and time is notable, as our coupler systems streamline the splicing process, decreasing the amount of labour required and time spent on site. This translates into more efficient project execution, less time-dependent material use and reduced idle resource consumption.
Enhanced structural efficiency is another significant advantage of our couplers, which are tested according to IS 16172:2023. They provide high strength and fatigue resistance, reducing the need for additional reinforcement in critical load-bearing structures. This ensures efficient material usage without compromising safety or performance. Moreover, the reuse of scrap steel is facilitated, as short steel bars that would otherwise be discarded can be connected and reused, thereby reducing the amount of scrap generated during construction. These benefits make our rebar couplers a sustainable choice for large-scale infrastructure projects, including highways, bridges, tunnels, and other heavy-duty constructions, supporting resource efficiency and cost-effectiveness.
With your SNTP ISI Mark Rebar Coupler, how do you see this innovation impacting the construction of critical infrastructure projects like bridges and high-rise buildings?
With the introduction of our ISI Mark Rebar Coupler, we foresee a transformative impact on the construction of critical infrastructure projects such as bridges, high-rise buildings, and other large-scale structures. The coupler’s compliance with the stringent IS 16172:2023 standards ensures its ability to deliver unmatched strength and durability, which are essential for these high-stakes projects.
For infrastructure like bridges and high-rise buildings, where the structural integrity and load-bearing capacity are non-negotiable, our couplers provide seamless and strong connections between rebar, ensuring that the structures can withstand heavy loads, vibrations, and stress over time. The couplers’ tested resistance to high fatigue loads, surpassing 2 million cycles, means they’re ideally suited for critical projects that demand long-term reliability.
By eliminating the need for overlapping rebar, our couplers help reduce steel consumption, making the construction process more efficient and sustainable. This is particularly impactful in large infrastructure projects where optimising material usage is crucial for cost control and timely completion.
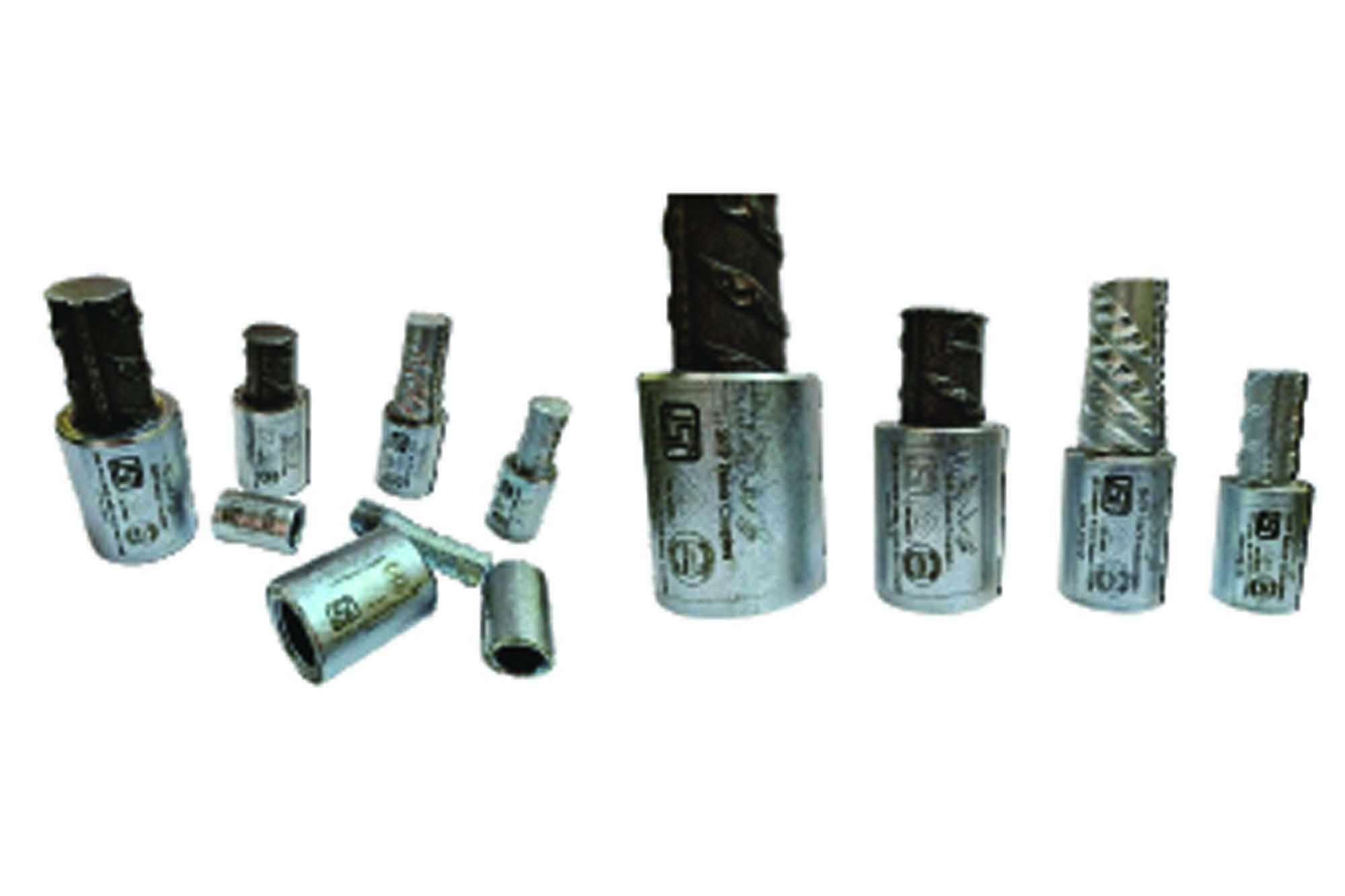
Our ISI Mark Rebar Coupler enhances the structural performance and safety of critical projects and supports faster, more resource-efficient construction, aligning with the industry’s modern demands.
Rebar congestion is a common challenge in construction. How do the SNTP Reinforcement Couplers help alleviate this issue, and what are the resulting benefits for concrete quality and structural integrity?
Rebar congestion poses significant challenges in construction, particularly at lap splice zones, where overlapping bars can increase material usage and hinder concrete placement. Our Rebar Coupler offers an effective solution to this issue by providing a mechanical connection between reinforcing bars, thereby reducing congestion and enhancing concrete quality and structural integrity.
Employing our Rebar Couplers eliminates the necessity for traditional lap splicing. This reduction in overlapping bars leads to decreased rebar congestion, facilitating easier concrete placement and consolidation. Consequently, the risk of voids and honeycombing is minimised, resulting in improved concrete quality. The technical benefits of our Rebar Couplers are substantial. The reduction in lap length is notable, as mechanical couplers remove the need for extended lap lengths required in conventional splicing, optimising rebar usage and reducing material waste. Furthermore, the precise nature of mechanical connections allows for exact rebar lengths, significantly reducing cutting waste and the generation of offcuts.
Our Rebar Couplers are designed to meet or exceed the tensile strength of the connected rebars, ensuring a robust and durable connection that maintains the structural integrity of the reinforced concrete element. In summary, integrating our Rebar Couplers in reinforced concrete construction effectively addresses rebar congestion, improving concrete quality and enhancing structural performance.
How does your range of couplers support the creation of durable infrastructure capable of withstanding increased environmental stresses?
Our Couplers represent the future of durable infrastructure, providing a robust and technically advanced solution capable of withstanding increased environmental stresses. They excel in several key areas, beginning with superior load transfer and stress distribution. Designed for a mechanical connection that matches or exceeds the tensile strength of the parent rebar, our couplers ensure seamless load transfer across the splice. This structural continuity allows critical infrastructures, such as bridges, tunnels, and high-rise buildings, to effectively distribute stresses, including axial tension, compression, and shear forces, without compromising stability.
Our couplers are engineered to perform under dynamic and cyclic loading conditions, meeting the rigorous fatigue requirements of IS 16172:2023. Their ability to withstand over 2 million fatigue load cycles makes them highly suitable for infrastructure in seismically active zones or high-load environments, where repeated loading, such as traffic on bridges and train movements in tunnels, can lead to premature failure of traditional lap splices. Additionally, corrosion protection is a significant consideration in infrastructure durability, as environmental degradation, particularly corrosion due to moisture and chemical exposure, is a critical factor in infrastructure deterioration. Our couplers undergo rigorous testing for corrosion resistance, employing surface treatments and material selections that prevent galvanic corrosion. This protection is essential for structures exposed to aggressive environments, such as marine infrastructure, bridges, and coastal developments.
The design of our couplers also leads to a reduction in congestion and enhanced concrete placement. These couplers reduce rebar congestion by eliminating the need for lap splicing, thereby improving concrete flow and consolidation during casting. This results in fewer voids and better compaction, which is crucial for achieving uniform concrete strength and durability, particularly under freeze-thaw cycles and chloride penetration conditions. Also, our couplers are tested and certified to comply with BIS IS 16172:2023 and international standards such as BS 8110 and Eurocode 2. This adherence ensures that the couplers can withstand environmental stresses while maintaining the integrity of reinforced concrete structures.
Another advantage of our couplers is their ability to eliminate lap length and offcuts. Traditional splicing requires extended lap lengths, leading to material wastage and potential weak points. Our couplers remove the need for lap lengths, reducing rebar consumption and minimising offcuts, which results in more efficient material use and higher-quality connections. Incorporating our couplers into infrastructure projects ensures optimal mechanical performance and enhances structures’ long-term durability and resilience, especially in challenging environmental conditions.
We offer a diverse range of couplers tailored to meet various engineering needs. Our Crimp-IT Couplers are suitable for in-situ bars and are known for their quick installation and high load-bearing capacity. The T-BAR Couplers are specifically designed with self-aligning threads, ensuring seamless integration, performance, and a thread-locking mechanism. Meanwhile, the R-B Couplers are engineered to meet or exceed the tensile strength of the parent rebar, providing reliable mechanical connections between reinforcement bars. These couplers are particularly effective for tension and compression applications, making them ideal for high-stress environments.
The Bolted Couplers offer a versatile and robust solution for connecting rebars in various structural applications. Utilising a bolting mechanism, they ensure a secure and efficient connection, making them suitable for projects with critical ease of assembly. These couplers can be used in multiple configurations, accommodating various rebar sizes and orientations. Lastly, our HD Anchors are heavy-duty anchoring solutions designed for high-performance applications in demanding environments. They provide exceptional load capacity and stability, making them ideal for critical infrastructure projects and suitable for concrete, rock, or soil anchoring. Together, our Couplers are essential components for future-proof infrastructure, delivering both performance and longevity.
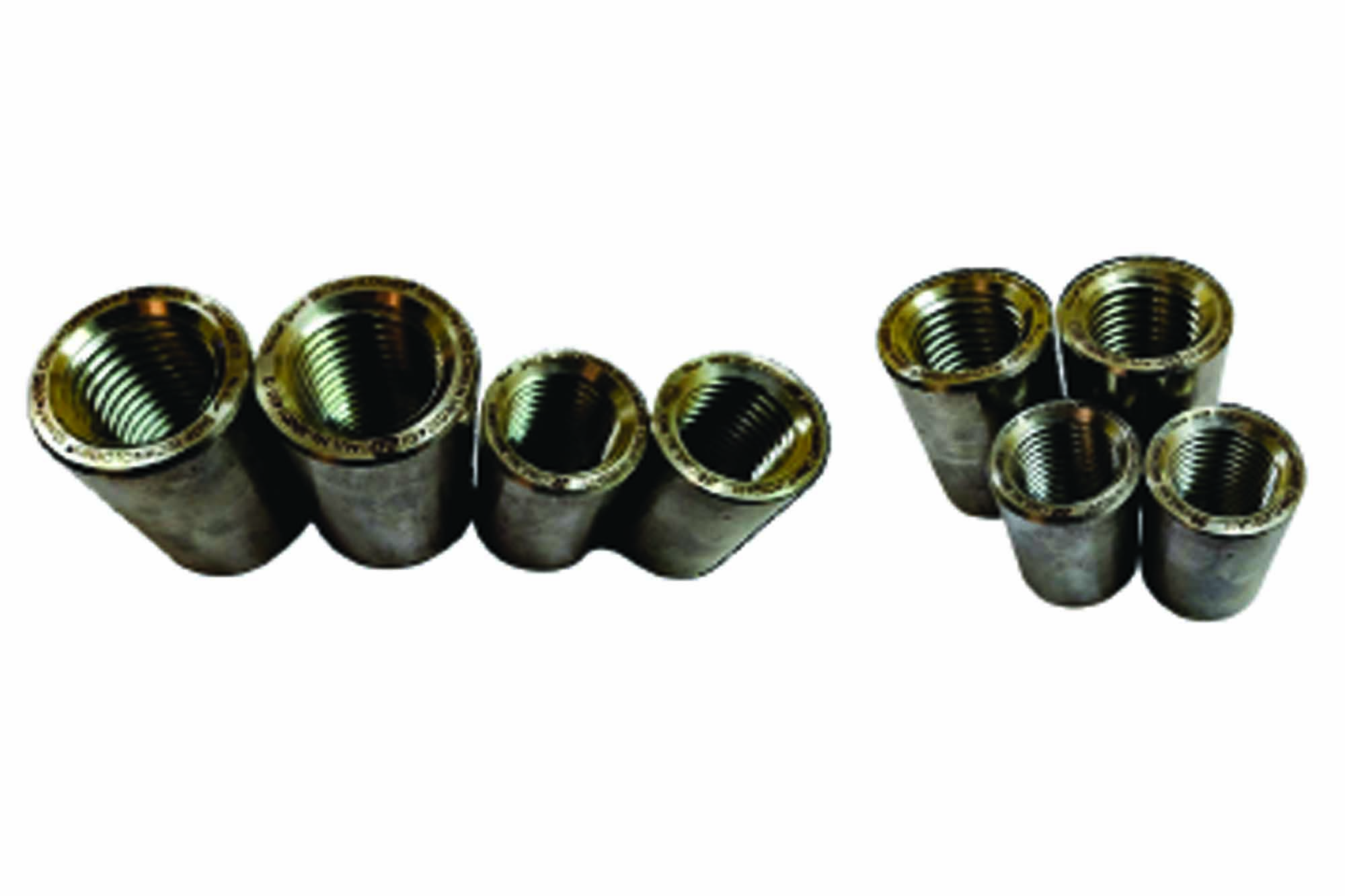
What innovations can we expect from SNTP Technologies India in Mechanical Splicing and Construction?
One key area of our focus will be advanced material science, where we aim to develop high-strength alloys that create new alloy compositions offering improved strength-to-weight ratios and enhanced corrosion resistance. This innovation is expected to significantly boost the durability of our couplers and anchors. Additionally, integrating smart materials that respond to environmental changes could provide real-time feedback on structural integrity, further enhancing safety and performance.
Sustainability initiatives will also play a crucial role in our future innovations. To reduce the carbon footprint of our products, we are emphasising the use of recyclable and environmentally friendly materials in our manufacturing processes. This includes sourcing raw materials from sustainable suppliers and implementing energy-efficient manufacturing practices.
On the technological front, we will continue to leverage advancements in automation and robotics for more efficient production processes. The introduction of AI-driven quality control systems will enable us to ensure the consistency and reliability of our couplers. We envision employing digital twin technology to simulate the performance of our products under various stress conditions, allowing for optimisation before production.
In line with these technological advancements, we will enhance our product offerings with innovative design features such as modular couplers that allow for easy adjustment to different rebar diameters and configurations. This adaptability will cater to a wider range of construction applications, from residential buildings to large infrastructure projects.
We are committed to continuous R&D initiatives to improve our product range, focusing on user feedback and industry trends. Collaborating with universities and research institutions will foster innovation, ensuring our solutions remain at the forefront of the construction industry. SNTP Technologies India is poised to lead the way in Mechanical Splicing and Construction innovation, creating solutions that meet the demands of today’s construction landscape and anticipate the challenges of tomorrow.
Cookie Consent
We use cookies to personalize your experience. By continuing to visit this website you agree to our Terms & Conditions, Privacy Policy and Cookie Policy.