Reverse Osmosis and IonExchange – Unique process steps to minimize the liquid discharge
By Edit Team | August 28, 2020 10:37 am SHARE
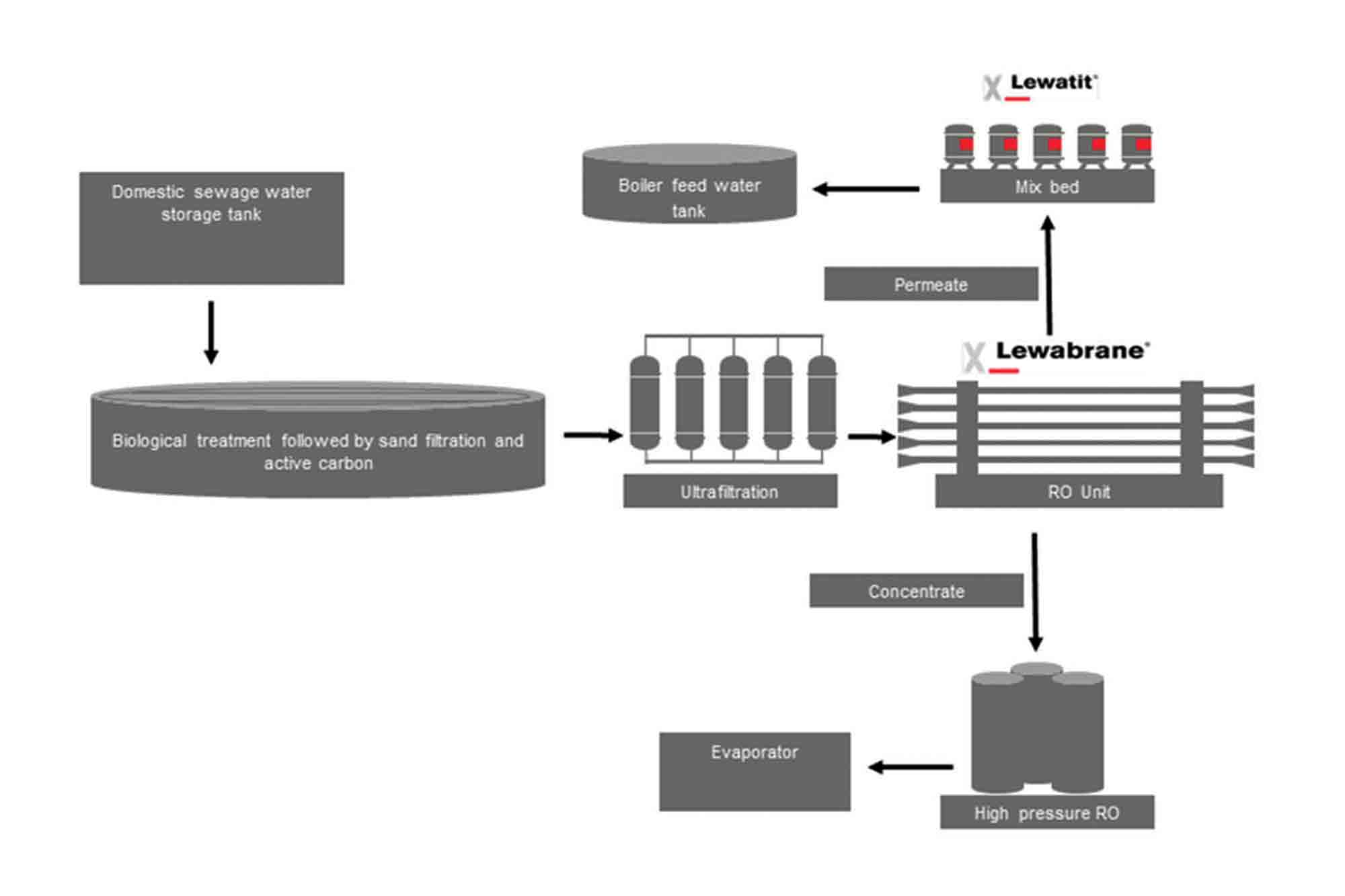
The application of water treatment technologies to achieve “minimal liquid discharge” (MLD) or “zero liquid discharge” (ZLD) is increasingly under consideration in today’s water-stressed world. MLD and ZLD are processes that minimize or eliminate the discharge of water or liquids from a plant process. The reasons to implement these processes can be
- Regulatory
- Cost-saving from water recycling, and reduction of water discharge costs
- Environmental – Increase sustainability of industrial sites in water-stressed regions
There are two treatment options for process water: internal recycling, and end-of-pipe treatment.
The internal recycling is conducted inside the plant processes and implemented by analyzing the water composition and the water quantity to make a so-called “pinch point” analysis. In this analysis, the water quality and water quantity are determined for a specific production step, and a decision is made as to whether it is possible to use the wastewater from a certain production step as the water supply for a separate production step. If usage is not possible, an interception technology may be used to get the water quality to the level suitable so that it can be reused. A typical technology for this is membrane technology. Depending on the type of contaminants, it can be microfiltration (MF) to remove bacterial substances, ultrafiltration (UF) to remove particulate and high molecular weight organics, nanofiltration (NF) to remove divalent salts and organics or reverse osmosis (RO) to remove salts and small organic compounds. Another technology that can be used is ion-exchange treatment (IX). This technology should be applied if a selective separation is preferred, e.g., to remove specifically some ionic contaminants from the process water or to recover valuable ionic or non-ionic substances selectively. This separation can be achieved using a special IX product called scavenger, selective resin or adsorber resin.
When interception technology is not possible, the client should consider the end-of-pipe treatment solution. In this case, the plant wastewater is collected and treated depending on the type of contaminants by either mechanical, biological, or filtration steps to produce a water quality that can be reused in an upstream plant process.
In MLD/ZLD processes, it is common that both interception and end-of-pipe treatment options can be applied for overall water management. Which treatment process is adopted usually depends on the size of the plant, and whether the treatment process is added to an existing plant. If an MLD/ZLD process implemented to an existing plant, in most cases an end-of-pipe treatment is preferred since less new piping, and less interference with the existing process is required.
In the following industrial examples, two MLD (minimal liquid discharge) processes, which were implemented in existing plants in India, are presented. These examples represent two different industries: the textile and the chemicals industry.
Chemical Industry
This zero liquid discharge wastewater treatment plant is located inside the water treatment facility section of a major specialty chemicals producer. The wastewater plant processes treated sewage water via UF (ultrafiltration) pretreatment, cartridge filtration, and RO membrane desalination. The desalinated water is further treated by degasification, and ion exchange mixed bed columns installed with Lewatit®MonoPlusS108H and MonoPlusM800 to prepare boiler feed water. The RO installation is a two-stage system with a capacity of 38 m3/h. The feed water to the RO has a TDS in the range of 600–1,300 mg/l. The permeate has a TDS below 20 mg/l, and after mix bed application, a final boiler feed water quality of < 0.1mg/l TDS and 0.02 mg/l silica.
The concentrate is further treated by high-pressure RO. The permeate of this concentrate RO is reused in the process, and, finally the brine concentrate is treated via an evaporation step to achieve the zero liquid discharge operation.
Table 1: At a glance:
Membrane performance
The water treatment installation was originally designed around “ultralow energy” seawater RO elements. However, after three years, these elements were replaced with Lewabrane® RO B400 HR elements since a performance projection (prepared with the LewaPlus® design software) showed that the required permeate quality could be achieved with standard test pressure BW elements operating at an even lower feed pressure.
After start-up, the predicted performance advantages of the Lewabrane® BWRO membranes were confirmed during routine daily operation. The RO feed pressure with Lewabrane® RO B400 HR was throughout three years below 9.5bar (with the previous SWRO elements feed pressures were on average12 bar). The RO system salt rejection was approx.98.6% (as compared to the 97.3% rejection achieved with the SWRO elements). The new Lewabrane® elements also provided an increased silica rejection (from 94% to 96.6%) resulting in an increase of the cycle time between regenerations for the mixed bed ion exchange system. After three years in operation (with monthly cleaning), the RO system rejection level is still in the order of 97.5%. Recently, the first stage Lewabrane® RO elements were replaced with a Fouling Resistant Type (Lewabrane® RO B400 FR) incorporating a 34mil feed spacer (recommended for wastewater application), which has resulted in a reduced cleaning frequency.
Textile Industry
The second industrial example is an innovative process in the textile industry. The dying process requires high concentrations of salt to fix the dyes onto the cellulose textile. At the end of the process, the wastewater stream consists of a high concentration of salts and organics. Discharging the untreated wastewater would not only be harmful for the environment, but it may also impact existing drinking water sources. Since the textile industry is an important employer, the Indian government strongly supports projects with MLD processes.
The aim of this MLD process was to reuse the process water, and recovery of the salt to
- Save feed water costs
- Realize cost savings by the recovery of the process salt
- Produce less waste
The key technologies to achieve a water quality, which could be reused in the process, were the application of a scavenger resin, a softening resin process, and a reverse osmosis process.
In this process, the wastewater is first treated with biological treatment (tertiary treatment) to reduce the amount of organics in the wastewater. This step is followed by quartz filtration. The process water is then passed through an ion-exchange treatment stage consisting of a scavenger resin to remove the organic substances, followed by high TDS water softening. Since sodium sulfate is added during the process, calcium must be removed to avoid the precipitation of calcium sulfate.
After the ion exchange sequence, the water is passed through a reverse osmosis system to remove salts and other remaining organics. The RO system operates at a recovery rate of 80%. The RO brine reject is further treated by NF (nanofiltration) membranes to recover the sulfate, while the sodium chloride, which passes through the NF membrane, is concentrated by a multiple-effect evaporator. The sodium chloride salts are finally dried in a solar pan (as solid waste).
The concentrated sulfate from the NF process step is reused in the process.
The efficiency of the different treatment steps can be seen in the following table:
Table 2: Water quality after treatment step
The MLD treatment process is extremely efficient, and this underlines the advantages of an ion exchange pretreatment for an RO process. The lifetime of the RO elements in this process is 3–4 years, with the added benefit of reduced COD content from the scavenger resin treatment step to reduce the potential of bio growth.
Table 3: At a glance: wastewater tram
Conclusion
The above industrial examples show that the reduction of wastewater, even in challenging process industries, is possible using the right tools. Ion exchange and reverse osmosis is a smart and efficient combination to treat wastewater with a high organics load and high salinity.
Even with waste-water as feed solution a final water quality, that can be used for boiler feed water, can be achieved by the combination of an RO system followed by polishing ion exchange mix bed.
The use of scavenger resin as a pretreatment before RO should be considered, to remove organics from the wastewater that can pass through an ultrafiltration process and lead to potential biofouling in the RO process.
Finally, for MLD/ZLD processes, it must be noted that it is often challenging to achieve standards, but innovative combinations of existing technologies make it possible to reach the targeted goal.
Cookie Consent
We use cookies to personalize your experience. By continuing to visit this website you agree to our Terms & Conditions, Privacy Policy and Cookie Policy.