Sai-Ansh offers plug and use Foam Concrete plant
By Edit Team | July 2, 2015 11:43 am SHARE
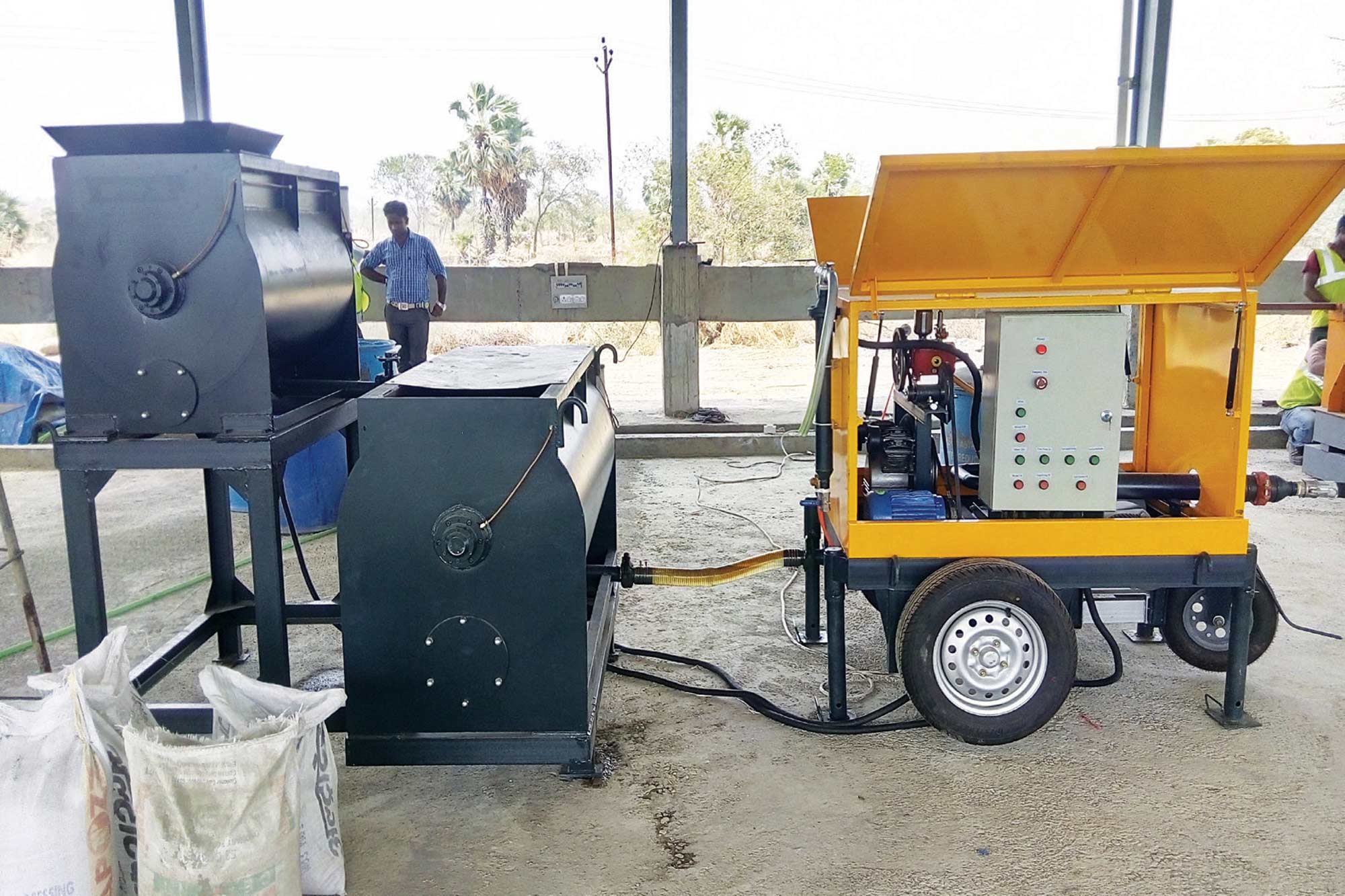
Foam Concrete is a very good replacement to block work, screed for surface preparation for waterproofing filling sunken area, and allied jobs
Foam Concrete or lightweight concrete are suitable for both precast and cast-in-place applications. Some of the highly insulative cementitious foams can be used as block fills, lightweight roof deck and void-fill materials. Good strength characteristics with reduced weight make lightweight Concrete suitable for structural and semi-structural applications such as lightweight partitions, wall and floor panels, and lightweight blocks. Cementitious Foams are suitable for thin layer coating applications where specific performance criteria are required. Foamed concrete and foamed cement have very fine pore structure. The dynamic nature of foam allows different foam rheology to be incorporated into the host cement or concrete matrix to satisfy a wide range of slump loss requirements.
The inert nature of foam systems makes them compatible with different kinds of aggregates, fillers, extenders, retarders, accelerators, colorants, hydraulic inorganic and many other additives.
Foam Concrete, also known as cellular concrete (CLC), is named after its peculiar composition a porous structure with microscopic air cells.
Advantages of Foam Concrete
• High heat and sound insulation
• Much faster spreading than the traditional mix of sand and cement
• Possibility to mix ingredients in the construction site, with no need for silos and expensive pre-mixed products
• Highly competitive price
• Energetic and economic saving
• High environmental compatibility.
Applications
Non-structural applications include:
• Layers: CLC is used mainly in insulating foundations and light layers, as a pipe height levelling and as a support to traditional layers, whose thickness and weight are thus reduced. Moreover, it improves considerably the damping of impact noise, thanks to its discontinuous and weak mechanical structure
• Sloping roofs: It is placed under waterproof layers, providing them outstanding values of thermal insulation
• Roadbeds
• Fillings: CLC proves a functional solution as a vault filling for constructions in old city centres, convents, hotels, hollow spaces or abandoned tunnels, underground passages or excavations of tubes to insulate their environment.
Structural applications include:
• Building blocks
• Prefabricated structures
• Placings.
CLC, together with sand in higher densities, is used more and more frequently as a real building material. It is particularly suitable for the production of building blocks, prefabricated panels, or cast-in-place vertical structures.
Foam Concrete plantSai-Ansh Engineers offers plug and ready-to-use type Foam Concrete plant, with integrated system consisting of mixer, foam generator and pump, working together.
With Sai-Ansh Engineers’s plant, Foam Concrete can be pumped to cast foam concrete walls or poured in moulds to make blocks or bricks. Foam Concrete can also be laid on terrace and other floors to get benefit of thermal and acoustic insulation, with all the other benefits of Foam Concrete. Foam Concrete is a very good replacement as screed for surface preparation for waterproofing and allied jobs.
The speciality of Sai-Ansh Engineers’s plant is that the density of the Foam Concrete can be adjusted easily by just turning a knob. The plant requires just 40 sq. ft. of area and requires just 06 HP (SA-40) of power (single-phase or three-phase motors can be provided), thereby considerably reducing the running cost. The plant can be very easily operated with just one operator by pressing buttons in the control panel, and unskilled labour to load the raw material.
“Sai-Ansh Engineers’s plant, like others, is not just a plant having a mixer, a Foam generator-cum-external compressor unit without any pumping facility,” claims the company. That was an old technology and a primitive method to make Foam Concrete where there was no consistency in the batches or even during discharge of a batch.
In Sai-Ansh Engineers plant, it takes merely 01-02 minutes to discharge one batch of Foam Concrete after the material is loaded in the plants mixer. Batch size depends on the capacity of the plant. Moreover, after the material is loaded in the mixer, there is no other operation to be done till the ready Foam Concrete is poured in the moulds or site at a distance of 200 metres from the plant, and 20 metres in height.
Even to adjust the density of the Foam Concrete one needs to just turn a knob and the quantity of foam will be varied and directly injected into the slurry, internally, thereby getting Foam Concrete of different densities. Complete secrecy in the mix design can be maintained as the setting of the Foam charged in the slurry can be locked.
Contact:
Sai-Ansh Engineers Pvt. Ltd.,
105, Stanford Plaza,Oshiwara Link Road,
Opposite Citi Mall,Andheri (West),
Mumbai – 400 053
Tele: 91-22-26732985
Mob: +91-9223347882
Email: rks@saiansh.com
www.saiansh.com
Cookie Consent
We use cookies to personalize your experience. By continuing to visit this website you agree to our Terms & Conditions, Privacy Policy and Cookie Policy.