Scaffolding & formwork for power plant execution
By Edit Team | July 18, 2016 10:37 am SHARE
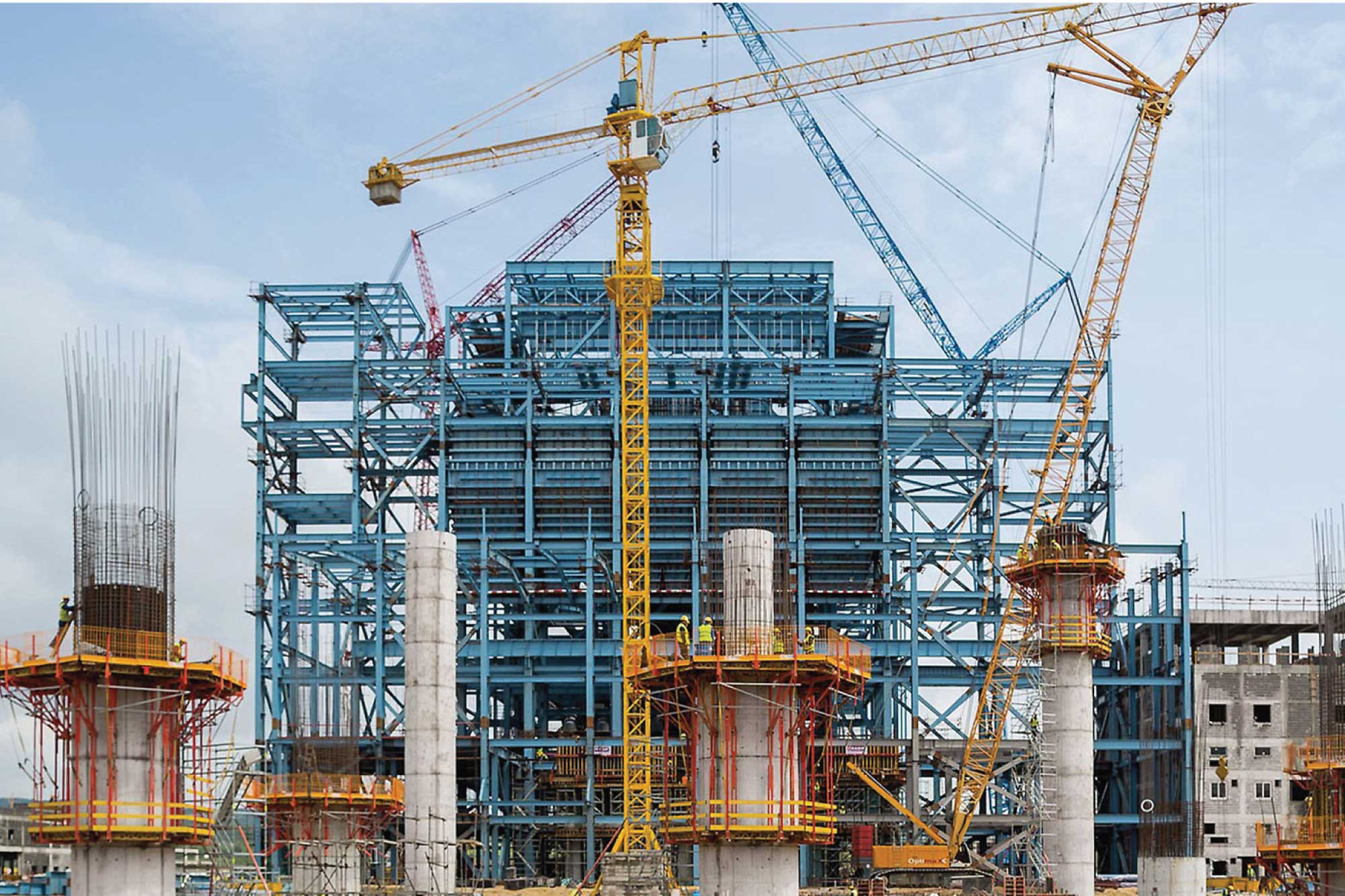
A review on the right scaffolding and formwork that can be used for power plant execution
Formwork and scaffolding play very important role in the construction of power plant. As time and safety are essence of power plant projects which demands planned usage of scaffolding and formwork material. Depending on the site conditions, timeline and sequence of construction type and optimum quantity of scaffolding is designed. It should be ensured that usage of scaffolding and formwork equipment should be done in a way it is designed for. This ensures achievement of planned progress with quality deliverables and safety.
Producing energy at the earliest is the prime goal of power station construction. Main challenges to achieve this include special stipulations made regarding the concrete and co-ordinated timing for different steps and suppliers apart from the different geological and topographic conditions. Massive components with a high degree of reinforcement and weight as well as great heights are also challenges faced for the construction of power plants.
Scaffolding and formwork are of prime importance for the power plant construction as it has maximum loading capacity, high level of flexibility in the application and carrying large amounts of material within the shortest construction time. Formwork and scaffolding required for the construction of power plant execution has to be individually developed and dimensioned. This is also the case for the Stanari coal fired power plant in Bosnia Herzegovina – the first power station in this region. It was supplied with formwork and scaffolding systems for two areas of the structure – a climbing formwork solution for the piers of the platform for the condenser as well as a combination consisting of stable shoring and complex arched slab formwork for the turbine building of the power plant.
MD Peri Company built a massive platform which was designed to carry the air cooled condenser for the power plant. A steel construction was positioned on a total of 9 circular concrete piers with external diameters of 3.60 m and with a wall thickness of 40 cm. Each pier is formed by means of 9 concreting cycles respectively, each cycle 3.00 m high. The massive, 2 m thick pier heads were constructed with the last cycle.
On each pier, 12 brackets of the CB 240 climbing system support the project specific VARIO GT 24 wall formwork elements. The finishing platforms were equipped with ladders which ensure quick access to the wall itself. The fact that the climbing brackets and formwork can be moved as a single unit by crane from concreting cycle to concreting cycle accelerates the construction progress.
On the inside of the piers, the BR shaft platform provides tailor made support for the wall formwork. For supporting the platform by means of gravity pivot plates, bearing boxes are mounted on the walls accordingly which simply remain in the wall after the platform beams are moved.
With a base area of 30.50 m x 12.00 m and a total height of 16.90 m, a very substantial structure subsequently housed the turbines. The entire turbine structure was characterised by impressive dimensions: the columns required crossed sections reaching up to 1.40 m x 2.10 m whilst the beams measure up to 2.10 m x 5.30 m, up to 5.30 m thick slab also featured arched sections in some areas. Only five months was made available for the GP Gradip AD construction team to complete the concreting work.
For the execution, a shoring solution was developed by PERI engineers on the basis of PERI UP modular scaffold that is designed to support the project specific formwork. The leg spacings of the 11.60 m high shoring vary between 25 cm and 150 cm – in this way the supporting structure is optimally adapted to suit the load requirements found in the different areas. For the flat slabs, MULTIFLEX girder slab formwork provides the necessary versatility to accommodate the high loads generated in the construction. With GT 24 formwork girder spacings of 30 cm, the construction can comfortably carry the high concreting loads.
For the arched construction, a supporting structure was developed by PERI design engineers, comprised of rentable system components: the construction features SLS heavy duty spindles, RCS rails and tubular steel slab props, covered with proven GT 24 formwork girders – and thus provides sufficient stability for the more than 5.00 m thick slab.
RWE Power AG built a power station at Eemshaven in the Netherlands. The anthracite-fired power station was built as a twin-unit plant to generate electricity in baseload operation. The entire project was completed in duration of 24 months.
Many types of formwork and scaffolding were used for the construction. Framax Xlife by Doka is the framed formwork system that uses few different panel formats to achieve a consistent 15 cm increment grid, whether the panels are stood upright or on their sides. All the connectors and accessories fit seamlessly into this grid making for fast forming times and high efficiency.
Edge protection system XP is the safety solution for all edge protection needs. It fits well with Doka systems, be it the wall or floor-slab formwork for safe guarding slab edges on the structure shell. Doka folding platforms K are preassembled, work-ready scaffold platforms with standardised system components for all usage situations.
Load-bearing tower Staxo 100, with its rugged steel frames, Staxo 100 is designed for large shoring-heights and high loads. It unites high load capacity and safety in every situation. Dam formwork is used for forming one-sided construction projects, such as dams, barrages, river power stations or pylons without formwork ties. The climbing tower will transfer all pouring loads into the previous pouring section. Different system variants D12, D15, D22 and D35 facilitate economic adaptation to various project-specific block dimensions.
The guided climbing formwork Xclimb 60 is a system that is guided on vertical profiles fixed to the structure, even during repositioning. The entire climbing unit is safely and easily repositioned in a single crane cycle, even during high winds. The construction of power station at Eemshaven was completed in the year 2012 with the usage of these systems and many more.
“Selection of right scaffolding and formwork is decided by various factors like the time taken to finish a project, sequence of construction, the condition of the site and the availability of the resources, availability of required man power for proper usage and safety of the workers,” informs Rohitt Sharma, Director, MFS Formwork Systems Pvt Ltd.
MFS Aluminium Formwork Systems and MFS Steel Scaffolding Systems offer formwork solutions and services for power plant construction which is part of infrastructure development and are known as complete solution provider in the related industries. It includes basic to advanced aspects of formwork and scaffolding components which can cater the need of forming any modern structure. Aluminium formwork systems, steel scaffolding systems and access scaffolding are the front line products.
Customer is more interested in opting for formwork solutions which are user friendly, with in – built safety features enabling speedy construction which make the project more viable and cost effective. Due to time constraints, user prefers suppliers with technical team who can offer end to end solutions i.e. designing with the use of latest software, manufacturing with automatic facilities with robotic concept, hassle free logistics and best onsite support followed by after sales services on single call.
MFS offers complete designing of formwork system, training, supervision, inspection of formwork at site besides supply of formwork systems.
“Accidents involving formwork and scaffolding often occur when formwork system or its components are not being used as per the user manual provided by the formwork associate. Contractor to ease his working starts using the components at places for which they are not designed for or some accessories are not placed as per the requirement. To avoid that, we provide proper training and education to site staff for proper usage of the system to avoid accidents,” concludes Sharma.
Cookie Consent
We use cookies to personalize your experience. By continuing to visit this website you agree to our Terms & Conditions, Privacy Policy and Cookie Policy.