Schmalz’s Lightweight Layer Gripper ZLW revolutionising material handling
By Staff Report | March 25, 2025 7:21 pm SHARE
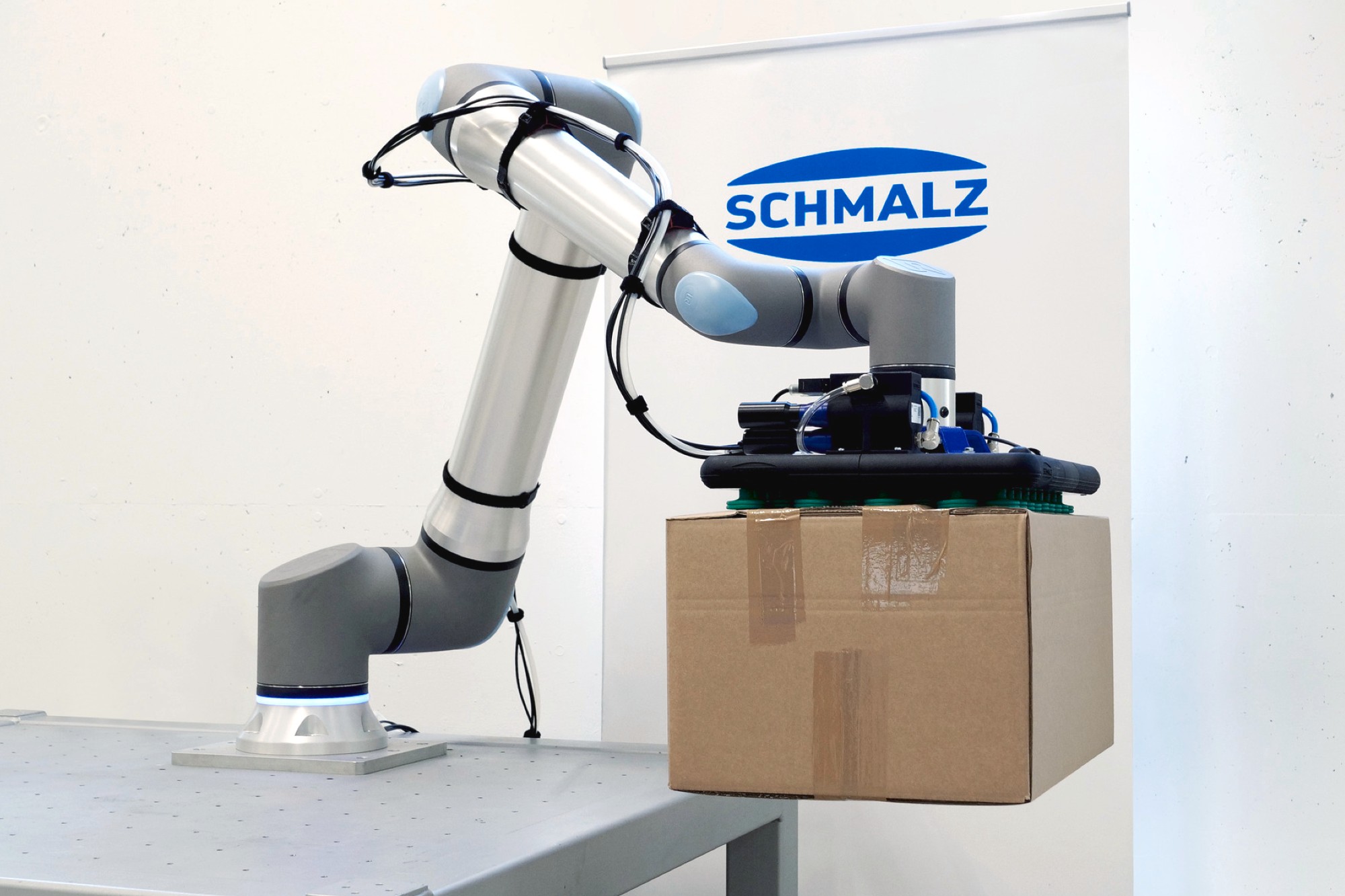
Material handling is becoming more efficient and precise as companies adopt automation, robotics, and AI. India’s fast adoption of smart technologies is fuelling innovations such as Schmalz’s Lightweight Layer Gripper ZLW, which optimises palletising, depalletizing, and logistics through seamless integration and adaptability.
The global manufacturing landscape is undergoing a transformation, fuelled by automation and smart technologies. Industries are increasingly using robotic solutions to improve efficiency, precision, and scalability. Automated systems improve production efficiency, reduce the need for manual labour, and ensure quality consistency. With the rise of Industry 4.0, manufacturing companies are integrating robotics, IoT, and AI-powered technologies to create connected and intelligent processes.
India, one of the world’s fastest-growing industrial economies, is rapidly adopting automation. The push for smart factories and digital transformation is being driven by factors such as rising labour costs, increased productivity, and the need for error-free production. Automotive, pharmaceuticals, food and beverage, electronics, and logistics industries are actively investing in robotic automation to remain competitive. Palletising, depalletizing, material handling, and packaging are some of the key processes being automated to boost operational efficiency.
How automation transforms manufacturing
Integrating automation into manufacturing workflows provides numerous benefits. Increased production speed enables businesses to meet growing market demands while maintaining quality. Reduced labour dependency helps to alleviate workforce shortages and reduce fatigue-related inefficiencies. Enhanced workplace safety ensures that employees are not exposed to hazardous lifting tasks, thereby reducing workplace injuries. Furthermore, automation helps to cut costs by reducing material waste, optimising energy consumption, and lowering operational expenses.
However, automation refers to robots replacing manual activities and improving human-machine collaboration. Human-Robot Collaboration is becoming an increasingly important part of modern manufacturing, as lightweight robots and collaborative automation tools assist workers with repetitive and physically demanding jobs. This is where innovative gripping solutions come into play, helping to optimise material movement across production processes.
Introducing the Lightweight Layer Gripper ZLW: A Smart Handling Solution
To fully realise the benefits of automation, firms need versatile and efficient material handling tools. Schmalz’s Lightweight Layer Gripper ZLW is designed to optimise palletising, depalletizing, and other intra-logistics activities with great precision and low effort. Its modular and lightweight design makes it perfect for cobots and smaller robotic systems, providing a smooth integration into automated workflows.
This unique gripper is useful for various production and packing applications in addition to palletisation. It is crucial in logistics and warehousing because it automates depalletizing and the flow of items between packaging and distribution stages. In the food and beverage industry, it effectively transports packaged items such as cartons, jars, cans, and plastic-wrapped products while guaranteeing hygienic conditions. The pharmaceutical business benefits from its precision in handling medicine boxes, vials, and sterile packaged items while adhering to tight cleanliness and safety regulations. It also improves consumer products packaging with pick-and-place applications, which move things from production lines to final packaging. The gripper is useful in automotive and manufacturing for facilitating line changes, transferring components between workstations, and placing finished goods into storage or final packing.
It is intended to meet various handling needs and comes in different sizes, making it suitable for multiple applications. Its lightweight aluminium design reduces the stress on robots, increasing efficiency. The gripper has a variable load capacity, making it suited for small and medium-sized workpieces while keeping a secure grip on various materials. Customisation possibilities enable adaptation to unique industry needs. The sealing elements come in two types: plug-in suction cups, which are suitable for homogeneous and sturdy surfaces, and sealing foam, which provides a secure grip on irregular or delicate materials. An optional floating flange compensates for height differences within a layer, resulting in constant performance. The vacuum system can be customised to meet individual operational needs, including external vacuum connections for high-power applications and an integrated vacuum generator for a compact, self-contained arrangement. Furthermore, an optional rounded safety frame improves protection in human-robot collaboration settings.
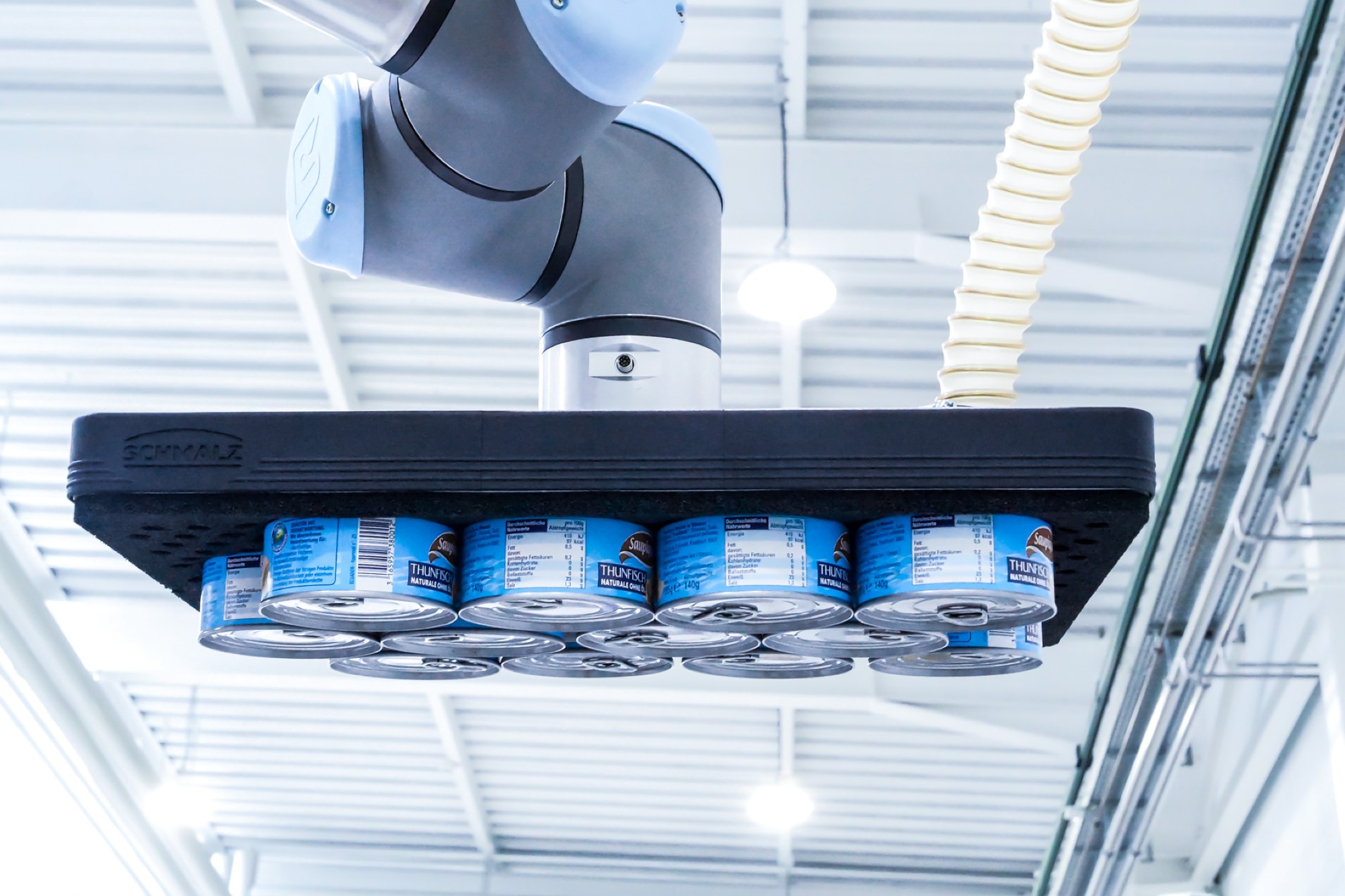
Handling capabilities and workpiece variability
One of the primary benefits of this technology is its capacity to handle different workpieces. It easily handles cardboard boxes, shrink-wrapped goods, plastic containers, metal cans, glass jars, and oddly shaped items. The versatile sealing choices enable a tight grip on both smooth and uneven surfaces, making it appropriate for both delicate and tough materials. This adaptability removes the need for frequent tool changes, hence improving efficiency and production.
How it works
The gripper uses innovative vacuum technology to precisely secure and carry workpieces. Once attached to a robot or gantry system, it aligns itself over the target layer. The Hoover mechanism engages, creating negative pressure to provide a firm grasp. If a floating flange is incorporated, it will automatically adjust to height differences to ensure a uniform gripping force. Once secured, the system seamlessly moves the workpieces to the desired place, whether for palletising, line transitions, packaging, or production mobility. The hoover is then released effectively, allowing for easy integration into automated procedures.
Optimising material handling beyond palletising
While frequently employed in palletising and depalletizing, this gripper has major advantages in production line transitions, where it aids in the movement of products between workstations during line changeovers. It also plays an important role in delivering finished goods to packing stations, guaranteeing a smooth workflow during the last stages of manufacturing. It also makes it easier to handle commodities for packaging, allowing objects to be moved more quickly into cartons, crates, or wrapping machines. These features make it an essential tool for modern automated production and logistical operations.
Key advantages
This technology has numerous benefits that improve usability and productivity. Its lightweight design minimises cargo requirements, making it perfect for collaborative robotics and compact automation systems. The modular design enables users to tailor the gripper to specific handling requirements, whether through changing sealing parts, hoover sources or safety features. Energy efficiency is a prominent feature, with optimised hoover production that reduces power usage while maintaining great gripping performance. Furthermore, the high interoperability guarantees easy integration with various robotic and automated systems, while the safety-enhanced operation makes it appropriate for HRC applications without jeopardising workplace safety.
This lightweight gripper, with its flexibility, efficiency, and precision, improves material handling in production, packaging, and logistics. Its versatility and customisation improve automation, resulting in increased productivity, safety, and process reliability.
For more information, visit: https://www.schmalz.com/en-us/
Cookie Consent
We use cookies to personalize your experience. By continuing to visit this website you agree to our Terms & Conditions, Privacy Policy and Cookie Policy.