Standing Seam Roofing System provides protection in all weather conditions
By Edit Team | January 25, 2016 12:01 pm SHARE
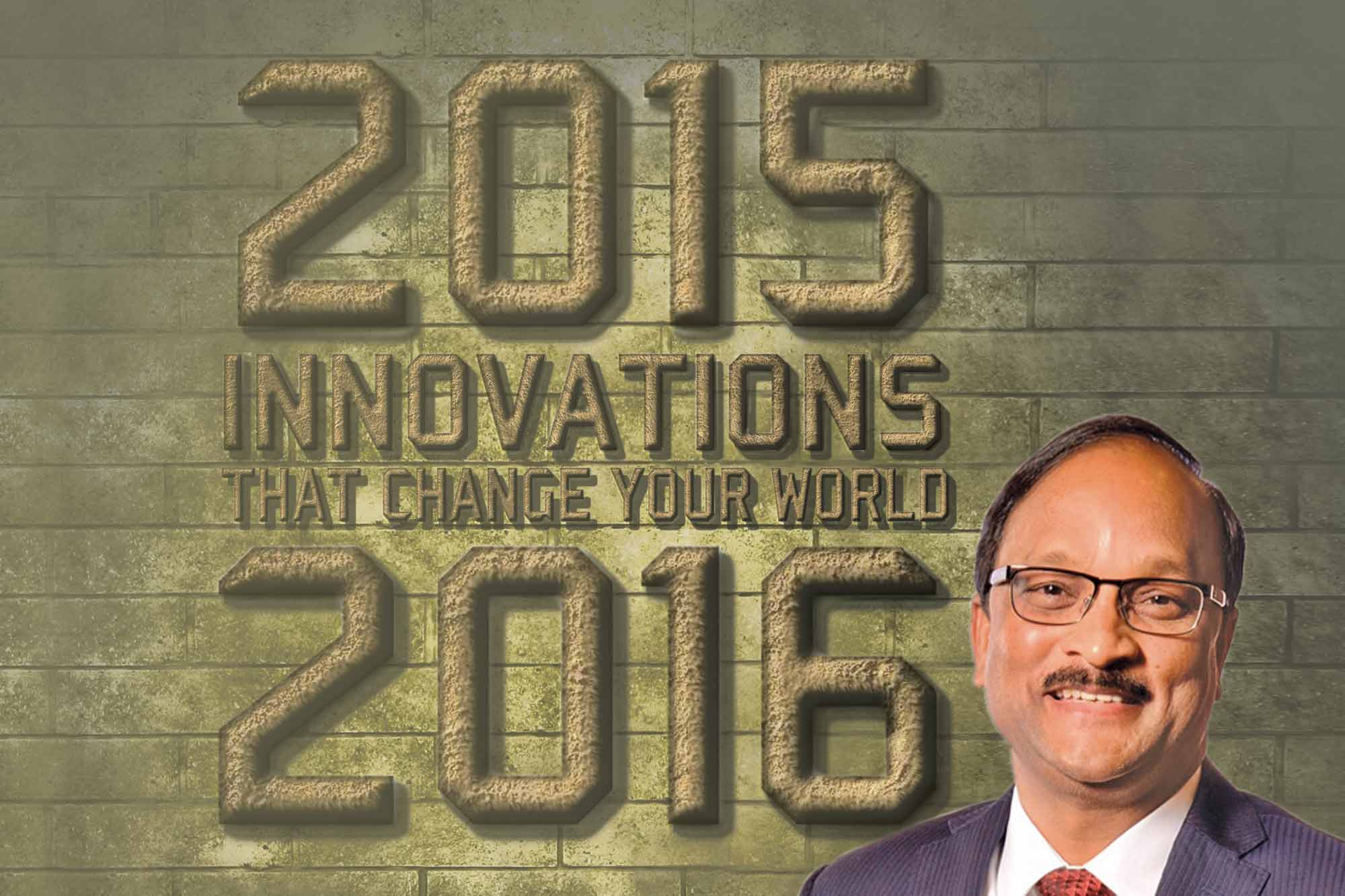
The usage of standing seam roofing system is rapidly increasing in India as most of the customers are demanding leak proof buildings.
Kirby India has introduced Standing Seam Roofing System, named as KSS-600 in India. Kirby Standing Seam Panel systems (KSS-600) is 100 per cent leak proof, has 360 degrees double lock standing seam ends, eliminates the risk of roof leakage at fasteners and side and end laps due to the concealed fastening system and provides protection in all weather conditions.
“Kirby is the first PEB manufacturer in India to achieve FM Global accreditation for its Standing Seam Roofing System. The usage of this standing seam roofing system is rapidly increasing in India as most of the customers are demanding leak proof buildings with Kirby India having already installed more than 15 lakh sq.m. of Kirby Standing Seam roofing system in the past 7 years,” claims D Raju, MD, Kirby Building Systems India Pvt Ltd.
The PEB industry has evolved from catering to applications such as warehouses and simple industrial buildings to constructing highly complex buildings such as high rise buildings, power plants, steel plants, shipyards and metro stations. These applications require much specialised design, manufacturing and installation skills to provide custom quality steel products for the structural steel industry.
Kirby is one of the few companies who are at forefront of this technology innovation with the concept of composite beam design being one of the breakthrough technology by which one could enter the high rise steel buildings segment. Kirby has commissioned many multi-storeyed commercial residential and commercial buildings (G+7 onwards to G+13 structures) in India and overseas. This required most advanced and integrated engineering software to manage design and detailing along with fabrication and erection.
“Kirby‘s PEB technology, with its specialised design software packages such as X-Steel, Bocad, ETABS and construction methodology with experienced project engineers, ensured that all our multi-storeyed buildings are completed in a short span of 6-8 months which is not possible with traditional RCC construction,” says Raju. Erection of high rise buildings also requires specialised and latest equipment such as mobile elevating working platforms and tower cranes which are used to lift loads to great heights and to facilitate the erection of steel building frames.
Kirby has also started doing open web trussed frames of triangular or trapezoidal cross sections for large free span structures to achieve economical weights and is currently executing an exhibition centre with tubular sections in Bengaluru.
Positive impacts
PEB technology ensures factory controlled quality environment and overcomes site constraints through reduced site construction time and elimination of site welding. In early 2000, nearly 4 mn sq.ft. of PEB was constructed for the first time in India, when PEB steel structures were used in Delhi Metro project. Nearly 13,000 tonnes of PEB structures for 23 metro stations in as many as 700 trailers were transported all the way from Hyderabad to Delhi. Since then, Kirby was also associated in executing buildings for other railway metro projects such as Bangalore Metro and Hyderabad Metro. Kirby has also introduced pre-engineered components in bridges and flyovers and has already executed Nandangiri flyover in Delhi for Commonwealth Games comprising of approximately 2,150 tonnes of steel.
Also, Kirby has commissioned many state-of-the-art power plant structures, some of them for global players in electricity generation and shipyards in India. Its installations include Pipavav Shipyard, India’s largest private shipyard along with Garden Reach Shipbuilders and Engineers Ltd and L&T Shipyard.
Cookie Consent
We use cookies to personalize your experience. By continuing to visit this website you agree to our Terms & Conditions, Privacy Policy and Cookie Policy.