Steel and metal structures: Fortifying resilience and longevity
By Edit Team | April 12, 2024 11:53 am SHARE
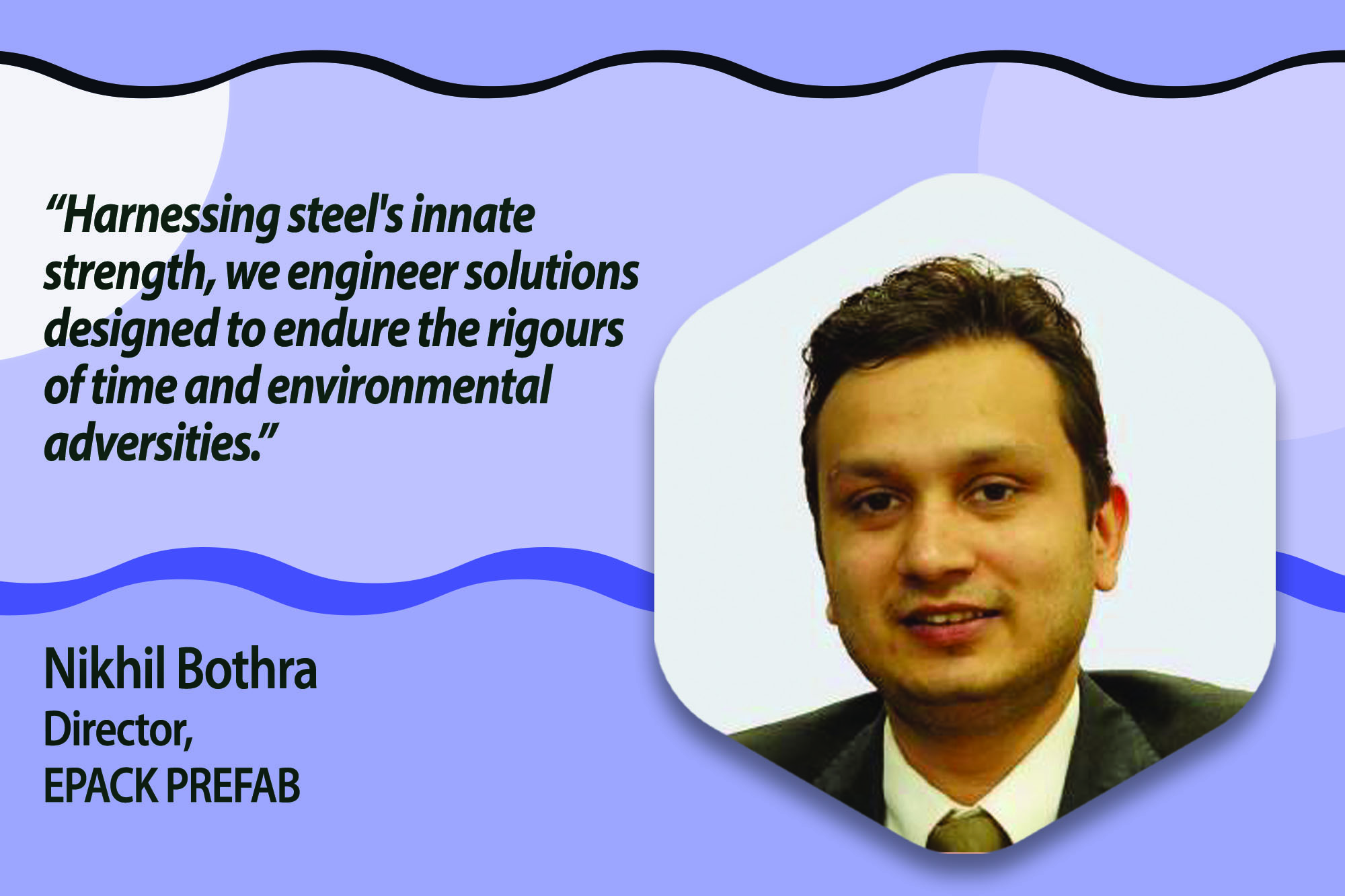
In this interview, we review how EPACK PREFAB uses steel and metal structures to improve the resilience and longevity of modern buildings and infrastructure projects.
How does your company leverage steel and metal structures to enhance the resilience and longevity of modern buildings and infrastructure projects?
At EPACK PREFAB, we recognise the indispensable contribution of steel and metal structures to fortifying the resilience and durability of contemporary buildings and infrastructure endeavours. Harnessing steel’s innate strength, we engineer solutions designed to endure the rigours of time and environmental adversities. By applying cutting-edge steel fabrication methodologies and premium-grade materials, we guarantee that our structures exhibit exceptional robustness and unparalleled resistance to corrosion, fire, and severe weather phenomena. This steadfast commitment ensures that our buildings and infrastructure projects remain steadfast and enduring across generations.
Can you discuss recent advancements in steel fabrication techniques or alloy compositions that improve structural performance and reduce environmental impact?
In recent years, significant strides have been made in steel fabrication techniques and alloy compositions to enhance structural performance and minimise environmental impact within pre-engineered steel building construction. One notable advancement involves the emergence of high-speed low alloy (HSLA) steels, engineered to offer heightened strength while improving weldability and formability compared to conventional carbon steels. The utilisation of HSLA steels enables the incorporation of lighter sections while upholding structural integrity, consequently reducing material consumption and the overall weight of the building.
Moreover, innovations in welding techniques have ushered in a new era of efficiency and quality in steel fabrication. Techniques such as robotic welding, laser welding, and friction stir welding have revolutionised the welding process, significantly reducing material waste, enhancing productivity, and fortifying buildings’ structural integrity.
Another noteworthy advancement is in corrosion-resistant coatings. Developing advanced coatings and surface treatments, including the Shot Blast Technique, Galvanising, Zinc-Aluminum Alloys, and Organic Coatings, offers robust protection against corrosion, prolonging steel structures’ service life and diminishing maintenance requirements.
These advancements represent a pivotal shift towards more sustainable and efficient practices within pre-engineered steel building construction. By embracing these cutting-edge techniques and materials, the industry aligns with the growing imperative of environmental stewardship and resource efficiency in construction, fostering a future characterised by resilient and eco-friendly infrastructure solutions.
How do you collaborate with architects and engineers to push the boundaries of design possibilities using steel and metal structures?
Collaboration serves as the cornerstone of our approach. We prioritise close partnerships with architects and engineers to explore the full spectrum of design possibilities using PEB steel structures. By amalgamating our proficiency in prefabrication with their creative insight and technical expertise, we transform innovative concepts into tangible solutions. Through transparent communication and mutual respect, we cultivate an environment conducive to exceeding our client’s expectations while pushing the boundaries of architectural excellence.
Furthermore, we actively organise and participate in events and brainstorming sessions where architects, engineers, and PEB experts converge to exchange ideas, explore novel approaches, and challenge conventional design norms. This collaborative forum fosters an environment ripe for breakthroughs in design innovation, enabling us to continuously shape the future of construction.
In what ways do your products and solutions address the need for lightweight yet durable structural components, particularly in high-rise construction and seismic zones?
EPACK PREFAB’s Pre-Engineered Buildings (PEBs) effectively address the demand for lightweight yet durable structural components essential for high-rise construction and seismic zones, offering a blend of cost-effectiveness, speed, safety, and adaptability. Firstly, PEBs stand out for their lightweight construction, surpassing conventional materials like concrete and masonry. This reduced mass translates to lower inertia forces during seismic events, consequently minimising structural demands and enhancing seismic performance.
PEB structures boast high flexibility, allowing them to undergo substantial deformations without catastrophic failure during earthquakes. This inherent flexibility enables the building to absorb seismic energy and dissipate it harmlessly, ensuring the safety of occupants. Additionally, PEB buildings incorporate bolted connections and flexible framing systems, facilitating efficient distribution of seismic forces and reducing stress concentrations, thereby enhancing earthquake resistance.
Thorough seismic analysis and design are integral components of PEB construction. Advanced computer simulations meticulously model earthquake loads and assess the building’s response, ensuring compliance with required seismic standards and optimal performance during seismic events. Finally, PEBs offer significant advantages over conventional steel structures, including cost-effectiveness, expedited construction timelines, low maintenance requirements, consistent span, and the capacity to provide column-free areas, further emphasising their suitability for seismic zones.
Could you elaborate on any prefabrication or modular construction techniques your company employs to streamline installation and reduce construction time?
At EPACK PREFAB, we implement various techniques to streamline installation and reduce construction time. One critical approach is modular construction, where we prefabricate building sections off-site, facilitating faster assembly on-site. Additionally, we harness advanced manufacturing technologies such as CAD, BIM, and automated assembly lines to enhance efficiency and precision in our prefabrication processes.
Ensuring on-time delivery is another crucial aspect of our strategy. We adhere to a rigorous logistics management system to ensure prompt delivery of building materials to the construction site, thereby minimising storage requirements and clutter. Furthermore, we prioritise collaborative design and construction practices, involving stakeholders early in the design process. This collaboration allows us to tailor prefabrication solutions to meet specific client requirements, further optimising construction timelines.
By integrating these techniques into our approach, we can expedite installation processes, reduce construction durations, and deliver high-quality projects efficiently to our clients.
How does your company ensure strict quality control and compliance with industry standards throughout manufacturing, ensuring safety and reliability in steel and metal structures?
Quality control and compliance with industry standards are non-negotiable aspects of our manufacturing process at EPACK PREFAB. We adhere to stringent quality control measures, from material selection to final inspection, at every production stage. Our state-of-the-art facilities are equipped with advanced testing equipment and staffed by highly skilled professionals who ensure that every product meets the highest safety and reliability standards. Additionally, we stay up-to-date with industry regulations and certifications, ensuring that our structures meet and exceed all relevant standards and codes. At EPACK PREFAB, quality and safety are ingrained in everything we do, and before the dispatch of any material, 180 quality checks are done by our expert team.
Cookie Consent
We use cookies to personalize your experience. By continuing to visit this website you agree to our Terms & Conditions, Privacy Policy and Cookie Policy.