Tarmat and Ammann India reconstruct Cochin Airport runway
By Edit Team | June 22, 2020 5:47 am SHARE
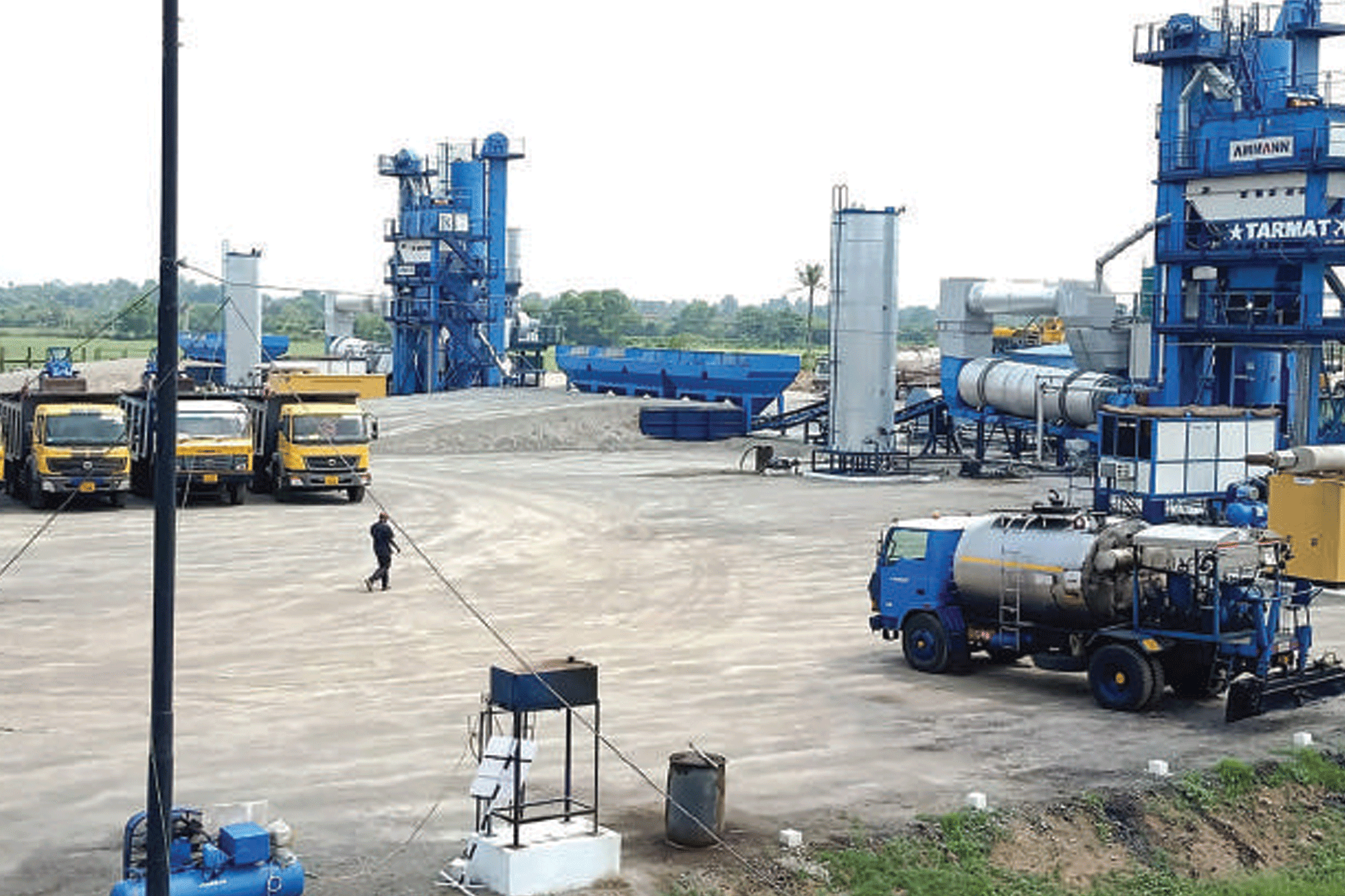
Tarmat Ltd addressed the challenges of the reconstruction of the Cochin Airport runway using key Ammann products.
Tarmat was established in 1986 and is an infrastructure construction company that often engages in the building of highways and runways. The company is headquartered in Mumbai with operations spread India.
Tarmat has mainly provided engineering, procurement and construction services for infrastructure projects sponsored by the central and state governments. Some of noteworthy projects of the company are the MES Arakkonam Naval airport, which has one of the longest runways in India; Jamnagar Airport; AAI Mumbai International Airport and Delhi IGI International Airport.
“There is no greater test of men and machines than an active runway construction,” said Jerry Varghese, the founder of Tarmat, which is based in Mumbai. “It is tough, demanding work that requires meticulous planning and timely execution with stringent quality assurance.”
The project required 3,000 tons of asphalt mix to be placed daily and in a five-hour working window. The resurfacing also included a profile correction of the runway at the airport located in the city of Kochi in the state of Kerala, India.
“We were issued a timeframe of eight months to complete the project, but have managed to execute over 90 per cent of the work in four months,” Varghese said.
The crew must be productive to accomplish so much in such a tight timeframe. Varghese pointed to plant and machine uptime as the force behind the productivity.
“One of the key success factors is that we did not miss out on our productive hours by even a minute,” Varghese said. “I would attribute this high productivity, which was instrumental to our success on the Cochin Airport runway project to Ammann India and its employees.”
Tarmatutilised several key Ammann products on the project, including two Ammann ABC 140 ValueTec Asphalt-Mixing Plants and an Ammann sprayer.
Varghese further stated that people make all the difference and Ammann team offered help in some specific ways during the project and they are as follows.
- Customer support – The Ammann customer support team has been cordial and co-operative in extending on-site parts support.
- Training – Ammann India deployed trained operators and technicians at the site, which helped significantly in becoming productive.
- Monitoring – Ammann engineers have been monitoring the condition of ABC ValueTec batch plants and machines on a regular basis.
- Maintenance – The plants and machineries were maintained proactively, which ensured zero breakdowns.
- Scheduling – The maintenance routines were scheduled by Ammann India in such a way that our productive hours were not impacted at all. The suggestions given by Ammann India towards proactive maintenance were very helpful and gave our team a new perspective on how to achieve more with Ammann products.
Cookie Consent
We use cookies to personalize your experience. By continuing to visit this website you agree to our Terms & Conditions, Privacy Policy and Cookie Policy.