Tech Trends: Bulk MHE for coal mines
By Edit Team | August 24, 2017 12:47 pm SHARE
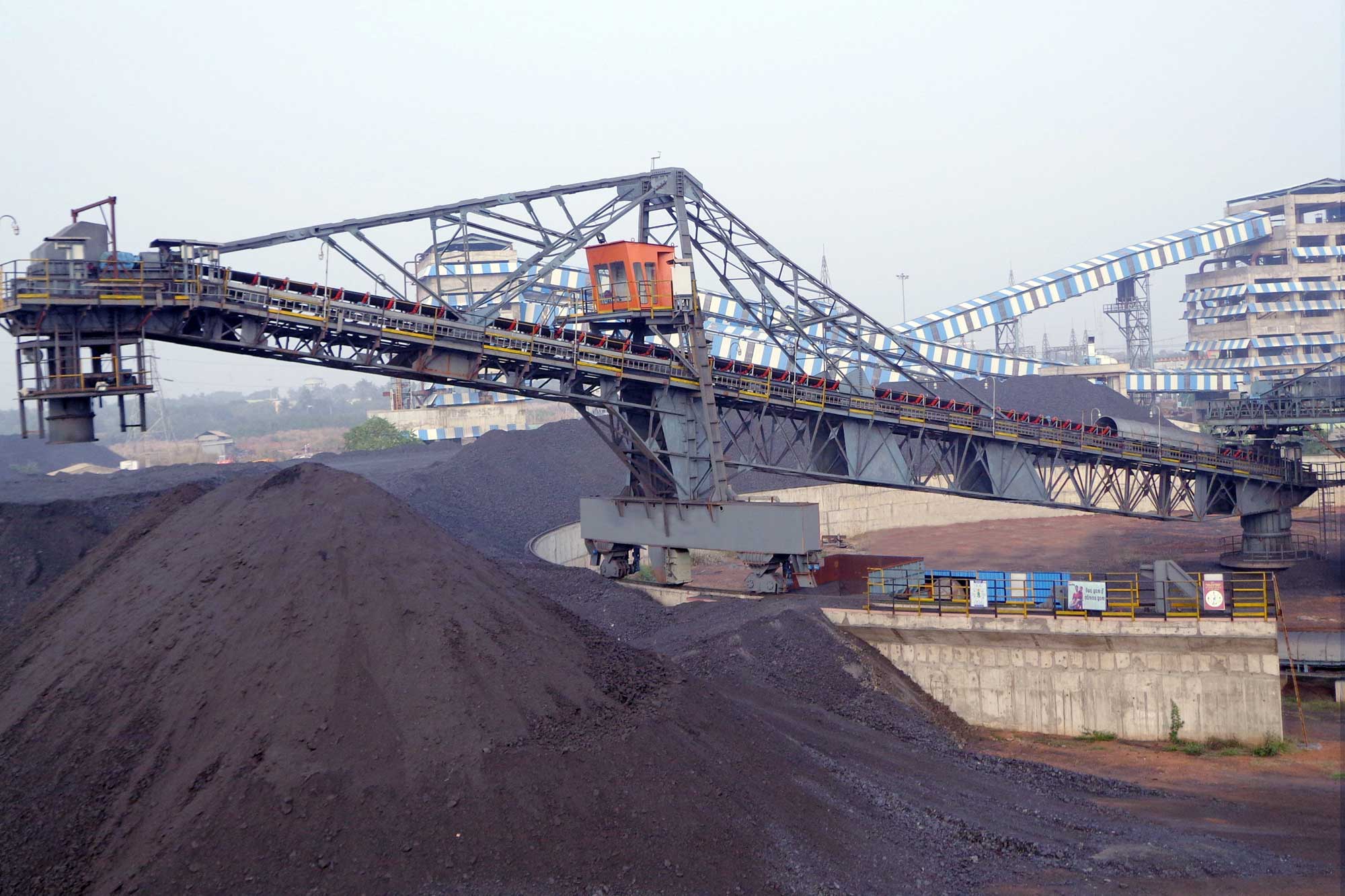
Advanced features of a few bulk material handling equipment used for coal mines.
Bulk material handling plays a vital role in the handling of dry materials such as ores, coal, cereals, wood chips and sand. Bulk material handling systems are composed of stationary machinery such as conveyor belts, stackers, screw conveyors, tubular drag conveyors, moving floors, toploaders etc. Advanced bulk material handling systems feature integrated bulk storage, conveying, and discharge.
The main purpose of a bulk material handling system is to transport material from one location to several locations. It also provides storage and inventory control, material blending as part of a bulk material handling system too. Here we feature few bulk materials handling equipment used for coal mines.
Turnkey solutions and project execution
Bevcon Wayors is two decades old organisation and one of the leading material handling systems or Equipment engineering and manufacturing firms based in Hyderabad with Pan India presence. “We provide concept to commissioning solutions and execute turnkey or EPC projects for all material handling applications for all sectors and establish ourselves as a reliable brand in bulk material handling industry,” says Y. Srinivas Reddy, Founder and Managing Director, Bevcon Wayors Pvt Ltd.
Sandwich belt high angle conveyor
For vertical conveying application which is revolutionary concept; Bevcon’s technology tie-up with Dos Santos intl. USA, a global major on high angle conveyor applications and design of sandwich belt type high angle conveyors for open pit mine and In-pit crushing conveying, which is breakthrough concept of conveying any mineral from pit bottom to the surface by totally eliminating use of conventional trucks. It also minimises the environmental degradation; flexibility of conveying profiles makes it one of the unique materials handling equipment of current generation and brings down the operational cost drastically and enhances productivity by retaining product quality. Its unique concept ever tried in Indian mining industry. These high angle conveyors are not new at all, but have not found wide use in IPCC systems where they can realise the greatest advantage.
Overland Pipe Conveyor
Modern and environmentally friendly overland pipe conveyor transport system overcomes numerous challenges associated with conventional conveyor systems. Pipe conveyors have best capabilities of transferring materials between two points managing both horizontal and vertical curves which are difficult in case of trough conveyors. It eliminates multiple transfer points and exposure of material to atmosphere.
Overland Troughed Conveyor
Overland troughed belt conveyors are designed to carry high tonnage loads over long distances. Bevcon’s long distance conveyor design ensures lowest power consumption per ton of conveying. Overland belt conveyors have been proven to be an efficient method of transporting bulk material over long distances and costs are often lower than with truck transportation.
Stockyard System
Bevcon brings the vast experience of their technology partner FMK, Poland, in design and development of wide range of stockyard equipment like stacker, reclaimer, stacker cum reclaimers, full and semi-portal scrapper reclaimer, side scraper and belt conveyor system for maximising the space utilisation to meet the expectations of project.
Flip Flow Screen
Introduction of high efficient ‘Flip-Flow Screens’ for screening of very high moisture materials more specifically ‘Coal’ has changed the philosophy of conventional screening methods in power and mining sector. India coal is most sought after fuel for thermal power units and most of the time either coal will be imported or mined from open cast mines and stored in open areas leading to high moisture absorption. The high moisture levels in the coal will be crushed and screened before it goes for boiler firing the challenge lies in screening ‘high moisture coal’ conventional screening methods used will not able to productive and meet the demands of the plant. Introduction of Flip Flow Screen has ability to screen coal with moisture of 40 per cent and efficient enough to the levels of 90 per cent screening.
In-pit crushing and screening
Bevcon has expertise in providing solutions to the in-pit crushing and screening application.
Idlers and pulleys
Bevcon has state-of-the-art manufacturing facility which manufactures Idlers and pulleys to meet underground coal mine safety and operating standards.
Most preferred crushing equipment is ‘sizer’
Sudhir Kumar, Manager, TRF Ltd says, “With Government of India’s focus on making the country self-reliant in power generation, an additional generation capacity of 66,600 MW will be made in 12th Five-Year Plan. As coal mining is a progressive process, the desired crushing and handling system for mined coal is semi mobile, preferably skid mounted. As the estimated HGI value of coal is 45 to 55 and the input size varies from 1000 mm to 1400 mm, the most preferred crushing equipment is sizer. To meet the growing demand for coal, TRF has developed sizers. All the components used in this equipment are developed/ procured indigenously.
Advantages or salient features
• Compact and flat design resulting in a low/reduced overall height of the crushing plant.
• Minimum fines generation in the final product due to low circumferential speed and special tooth configuration.
• Low dust burden resulting in small pollution control system required.
• Easy replacement of crushing segments picks and comb plates.
• Inclination of feed side walls is adjustable to improve material feed and intake of larger feed lumps.
• In most cases pre-screening is not necessary, as the fines contained in the final product can smoothly pass through the crushing zone.
• High throughput capacities (up to 5000 t/h) at low operating costs.
• Low specific wear rate due to slow circumferential speeds.
• Insensitivity to smeary, ductile, wet and sticky feed materials.
Working Principle
Kumar further highlights the working principle i.e. large teeth; small diameter shaft and low speed of the rotor give three-stage breaking action.
First stage
The large rotor teeth grip the material at multiple points, which induces stress and flaw lines and enables crushing of lump with lower energy.
Second stage
Secondary breaking takes place where three-point loading is created between the top face of tooth on one rotor and the top of two opposite teeth on the other rotor, inducing tensile stress in the lump. As the tensile strength is much lower than the compressive strength, it reduces power requirement for crushing.
Third stage
Breaker bar below the centre line of the rotors allows any oversize lumps carried by the scroll through the rotors, again exploiting the weaker tensile strength of the material. The breaker bar which forms a comb through which the rotor teeth has to pass, can be adjusted up or down to achieve the desired product size.
In conclusion Kumar says, “TRF machines have fully fabricated housing, stress relieved and close tolerance. These are fully doweled assembled and bored, housed with carburised and ground gears in case of single drive. The company is capable of designing machines with both, single or double drive.”
Cookie Consent
We use cookies to personalize your experience. By continuing to visit this website you agree to our Terms & Conditions, Privacy Policy and Cookie Policy.