Technology evolution to improve the efficiency of PEB
By Edit Team | January 9, 2023 7:16 pm SHARE
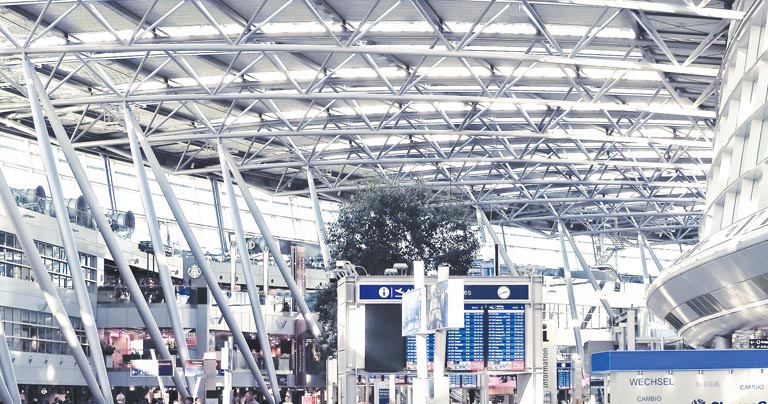
Moving towards innovative technologies
While discussing the necessary technologies for PEB, Ramachandran, Deputy General Manager at Everest Steel Building Solutions, states that quick project execution requires a technology-driven, reliable project management system under our control. This directly increases the effectiveness of the site’s construction. If we are building a warehouse, the materials must arrive at the site precisely when the structure is underway and continue for a while. It does not, however, keep any inventory at a facility. Businesses need help achieving their goals.
Further, there is much room for improvement. Project management that relies heavily on technology makes it much easier to use labour hours directly on the construction site, whether with an erector or a contractor we employ. This ultimately allows us to shorten the total project lifecycle and benefit from significant cost savings.
While emphasising the need for technology, Nikhil Bothra, Director of Epack Group, discusses how we managed projects earlier and how we are managing them today, which have undergone a paradigm shift. Technology-wise, we have seen a wide variety of planning software in different domains. There is a software that helps us design, if the building designs are uploaded it will show the sequence of erection, the required building component, duration for complete of the project, resources needed, manpower required, and so everything will be designed by one software.
These technological advancements support the contractors on-site because, at the moment, neither production nor design presents a challenge because they can all be quickly managed in a controlled environment. The site’s efficient operation and project completion within the budget and time constraints present the only challenges. Many businesses are investing millions of rupees in it. Therefore, there is a lot of assistance provided to the contractors for the project’s execution.
Ramachandran adds that one of the biggest problems we have in this particular sector is that there need to be more skilled workers and few efficient contractors. Maintaining a constant grasp of them is necessary. We must ensure that the materials are delivered on time to reduce the expense of hiring new employees and the cost of their labour, which benefits the business as a whole. As the entire construction process depends on how well, sequentially, and fully we can fill, the construction or erection of a specific structure becomes much more affordable and efficient.
When discussing the investments for PEB, Bothra states that, when comparing the initial and ongoing costs of a building, there are significant differences because a steel building may be constructed in a significantly shorter amount of time than an RCC building when using effective insulation techniques. Revenue from a facility that will generate rentals or other sources of income, such as a school or office building that will be leased out, might be made much sooner. This is one area where the entire cost of the project can be optimised.
Bothra further emphasises that, many people use these structures for 25 to 30 years before deciding to demolish them. At that point, steel prices will have increased due to investments made 30 to 40 years earlier. Therefore, the cost of the steel now would be equal to its scrap value 40–50 years from now. Thus, the initial investment will be repaid at the end of the building’s useful life. As a result, the building’s overall design makes more sense, and more people are becoming aware of it. As a result, overall input or utilisation growth should be present in the coming years.
Impact of the rising cost of steel
While discussing about the rising steel prices Bothra says that, along with the PEB makers, clients have also undergone significant change due to this instability. Before this volatility, whenever we negotiated or spoke with a client, they would always inquire about the tonnage and price. But now, a new issue—the cost of the raw materials—has come to light. Since everyone is aware that we have no idea what the steel prices will be when we finalise the order three months from now, most clients have started to inquire about the steel’s pricing, tonnage, and base price. As a result, the contract now includes one more base pricing point.
There has been a lot of change in terms of the way contracts are now agreed upon and signed. Since the base pricing is now getting fixed slowly, we can see the conversion at the margins, which we used to refer to earlier, getting even slimmer. The steel manufacturers, the government, and their high officials know that steel is an essential component of infrastructure development projects. And the companies that work for the government will not be able to sustain themselves; they will fail.
Speaking of this volatility, Ramachandra adds that it will only last for a while. Before offering an opportunity, people have begun to think somewhat differently. This has changed the perspective of the manufacturer and created opportunities for people. We were examining potential improvement opportunities. We have concluded that this is explosive. This has been exceptionally advantageous because hardship draws the best talent in the field. People are now starting to adjust in the steel industry. And the market is maturing and will do better going forward.
While discussing the fluctuation of prices, Bothra talks about the challenges in the PEB sectors. “It’s a large claim to make about affordability; therefore, it depends on how the building is used, who is purchasing it, for what reason, and what the major goals of the building are.” The PEB building is the most efficient in the eyes of those that prioritise timeframes over costs. They ignore the price, which can be 5–10 percent greater. They know the entire value of the building, its lifespan is currently significantly lower than that of a typical building.
Ramachandran adds in “Residential is one area, especially in this country, where it could be “tap” meaning it’s hard to pick up, but the opportunities are enormous. Once it starts picking up, there will be a significant paradigm shift in the steel-building industry in India. That is where the awareness is increasing. At least in certain metros, awareness can be seen at a higher level. It will take time, but I believe this area has a large market to tap”.
Nikhil Bothra, Director of Epack Group, “The PEB building is the most efficient in the eyes of those that prioritise timeframes over costs”
Ramachandran, Deputy General Manager at Everest Steel Building Solutions,
“Steel building will soon see a paradigm shift as it has enormous opportunities in residential field”
Cookie Consent
We use cookies to personalize your experience. By continuing to visit this website you agree to our Terms & Conditions, Privacy Policy and Cookie Policy.