The durability of reinforced concrete structures for corrosion of rebars
By Edit Team | September 12, 2022 2:04 pm SHARE
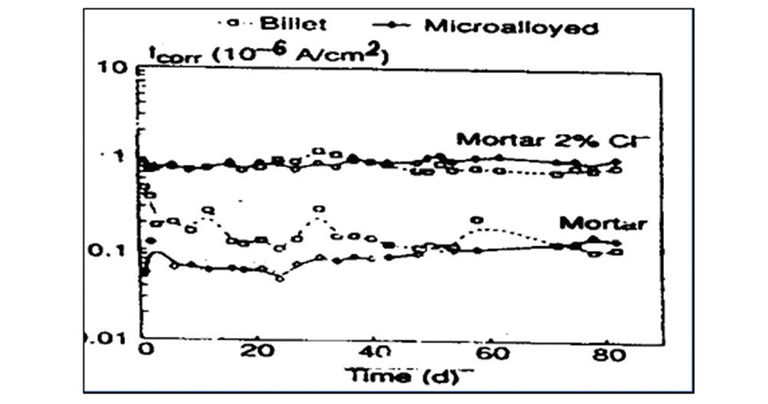
Introduction Reinforcement of steel in concrete enhances the concrete’s tensile strength and helps it sustain seismic activity. The most common material choice for reinforcement is steel. Millions of buildings, structures, and bridges are made using this combination of steel reinforcement and concrete. In the nineties, there was a sudden increase in the deterioration of RCC buildings, especially in the nearby coastal zones or cities with high humidity and pollution. There were initially a few trial methods of modifying steel composition by adding elements such as Cu, Zn, and/or Ni and, secondly, by doing a liquid cement coating over steel bars. Both of these methods were not very effective. Thus, a series of systematic methodologies were proposed:
• Using TMT bars (Thermo mechanically treated bars) per cent).
• Using CECRI Technology’s polymer composite coating (CPCC),
• Liquid Paint Coatings
• Fusion Bond Epoxy Coatings
• Use of Inhibitor Chemicals and/or Volatile Corrosion Inhibitors
• Galvanised steel coatings and CGR (Continuous Galvanised Rebars)
• Stainless steel rebars
• FRP Rebars
TMT bars are being wrongly projected as corrosion protection technology, which is not. The thermo-mechanical treatment (TMT) only removes 5–10 microns of the martensitic hard layer, which has no direct relation to corrosion protection. It is a hard layer that protects the rebar from damage during handling. CRS-Corrosion-resistant steel is a half-backed technology again being wrongly imposed as corrosion-resistant steel by adding 1.5-2.4 wt per cent of elements such as Cr, Ni, Cu, and Mo. Experience has shown that such modifications enhance life by 1 to 1½ times and therefore are not suitable to provide a durable structure lasting more than 30 years or so. These partial modifications initially show a lower corrosion rate. Still, in the long run, they are harmful, as shown in a study (Fig. 1), how an inadequate concentration of alloying elements helps initially to lower corrosion but enhances corrosion at a later date (lower curve), and where the concrete already has some chlorides, there is no effect at all (upper curve).
Fig. 1: Effect of some aspects on the corrosion of steel rebar, which initially appears to protect but in the long run deteriorates the corrosion.
CPCC is not a technology for large-scale, high-volume rebar requirement projects. Moreover, it exploits only a minimal concept of adding a few per cent of acrylic resin to the cement water mixture. Because acrylic is a relatively low corrosion-resistant resin, the technology does not ensure a quality process for large-scale rebar production or long-term protection.
As far as coated steel using liquid paint is concerned, it is again not a viable technology for big buildings and structures as it is a batch and discontinuous process— furthermore, the coating cracks on bending.
Fusion Bond Epoxy, which is applied hot, overcomes the cracking on bending and thus provides perhaps one of the best-coated rebars with all the excellent properties required for a concrete structure and can provide a long-lasting, durable life of 30–60 years or more. The Ministry of Highways approved it as a technology in 1997 and has since coated over 900 structures. Until today, no distress has been reported on any structure, nor has any rehabilitation taken place on any structure. Though this technology has drawbacks such as handling problems and lower bond strength with concrete, experience shows that these can be taken care of. Thus, it is expected to have a life of more than 60 years using FBE technology.
The use of zinc-based galvanised rebar can be another choice. This is also a good technology that overcomes the drawbacks of FBE, which is that it breaks during handling. Another advantage of galvanised bars is that they give dual protection to the rebar: barrier protection and cathodic protection. Using a galvanised bar, it is possible to get a life of 70-75 years. CGR bars are also galvanised bars made continuously by a modified hot melt dip process. When added to concrete cover, certain chemical compounds, such as calcium nitrite and many more, delay the movement of moisture and pollutants to reach the steel/concrete interface, thus delaying the initiation of the corrosion process at the rebar. In the same way, certain specific chemicals, such as volatile chemicals such as DICHAN, can help inhibit and tend to move to the steel surface and create a temporary corrosion layer. This technology is more commonly utilised as an additional technology for coatings and CRS/TMT or for repairing and rehabilitating RCC structures. It can never be a technology for the long-term durability of an RCC structure.
Stainless steel is perhaps the most corrosion-resistant material, which remains un-attacked even in a highly polluted environment. This mainly protects the RCC structure by not initiating a corrosion reaction even if a large concentration of pollutants has reached the concrete/rebar interface. That is why a life of 120–200 years is expected for RCC structures using SS rebars.
FRP rebars are also good. They are very light and have no possibility of corrosion. The other problems include continuous fabrication of various diameters and lengths and storing them. They are prone to moisture, sunlight, and microbial corrosion.
Thus, if we have now compared various rebar protection technologies, they can be best compared using a common model, as shown in Fig. 2.
Model for Estimating the Durability using a reinforced Bar
A simple model for the durability of the reinforced concrete structure can be understood from the following schematic, given in Fig. 2. Rebar is covered with a concrete cover whose density (M40, M60, or M80) decides its capability to permeate moisture or pollutants. Rebar corrosion can occur only if moisture/pollutants enter the concrete cover and reach the concrete/rebar interface “B”. However, the initiation of moisture or pollutants starts from the concrete cover surface “A” and its transportation through the concrete cover.
Fig. 2 Schematic of a concrete reinforced structure
Thus, to enhance the durability of a concrete structure, it is necessary to design it with the following properties:
• Create appropriate barrier protection at the concrete cover to prevent pollutants from entering the concrete cover.
• If a small percentage of moisture or pollutants enter the cover, their diffusion or transportation through the concrete cover is slowed.
• Create a solid natural obstruction on the steel surface so that the pollutants cannot react with steel and form the voluminous corrosion products which cause distress to the structure.
Cookie Consent
We use cookies to personalize your experience. By continuing to visit this website you agree to our Terms & Conditions, Privacy Policy and Cookie Policy.