Up to 70 percent less rework: pulse welding with Fronius TransSteel Pulse
By Edit Team | November 13, 2020 5:59 pm SHARE
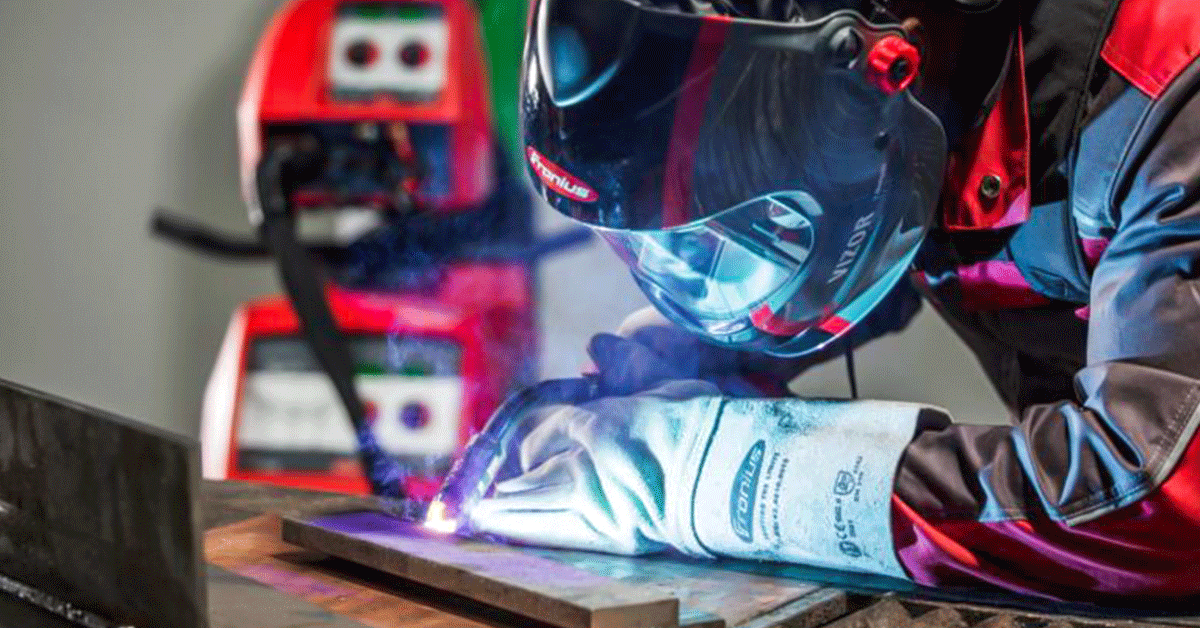
Fronius is upgrading its TransSteel series with the addition of the pulse function. Not only does the pulsed arc allow faster welding speeds on thicker materials, but rework is reduced as the pulsed arc causes less welding spatter.
The pulse mode makes it possible to bypass the intermediate arc, which is difficult to control and prone to spatter. The resulting reduction in spattering leads to up to 70 percent less rework. Furthermore, the pulsed arc allows welding speeds that are up to 30 per cent higher to be achieved. All these advantages are now also available from the Fronius TransSteel 3000 compact as well as the TransSteel 4000 and 5000.
Pulse Tacking To Avoid Distortion
The TransSteel devices were developed especially for use on steel. The addition of the pulse function now makes these power sources true all-rounders, as a wide range of functions supports the welder in various applications. With the help of the spot function, even and consistent welding spots can be produced – ideal for tacking workpieces. Interval welding not only produces a rippled seam appearance, but the lower heat input also reduces the possibility of material distortion on light gage sheets.
Special characteristics ensure the user has the ideal arc properties at their disposal. The “Steel” universal characteristics are particularly suitable for simple and fast welding applications. “Steel Root” has been developed for root welding and also provides a soft and stable dip transfer arc for good gap-bridging ability over wide gaps. The “Steel Dynamic” welding program, on the other hand, produces a particularly hard and concentrated arc, thus achieving high welding speeds and deep penetration.
Where minimal spattering and deep penetration are the order of the day, the TransSteel Pulse models with “Pulse Controlled Spray Arc” provide the perfect settings. With the “SynchroPulse”, the welding power alternates between two operating points at a frequency of up to 5 Hertz. As the change between high and low current facilitates welding in a vertical up position, for example, it is possible to produce a pronounced seam rippling on aluminium alloys.
Three Power Categories, Two Models, One Solution
The intuitive operating concept of the TransSteel allows immediate commissioning of the device without any previous knowledge. All the necessary welding parameters can be set on the front panel. A simple option for documenting the welding data completes the device concept. A USB thumb drive can be connected to the rear of the power source to store all important data – including time and device-related data, but also the parameters used such as current, voltage, and wire speed.
Fronius has added the pulse function to three models. The TransSteel 3000 compact Pulse is a multiprocess device that masters all three welding processes to the same high degree. The compact unit is ideal for a wide range of welding tasks on the construction site, in the workshop, or for repair work. For recurring welding tasks or in small series production, the pulse function on the TransSteel 4000 Pulse and TransSteel 5000 Pulse brings more options and speed. In contrast to the Compact version, these higher-power units have a separate wirefeeder.
For more information, visit:
www.fronius.com
Cookie Consent
We use cookies to personalize your experience. By continuing to visit this website you agree to our Terms & Conditions, Privacy Policy and Cookie Policy.