We aim to use 3DCP technology for sustainable infrastructure projects
By Edit Team | December 14, 2022 12:53 pm SHARE
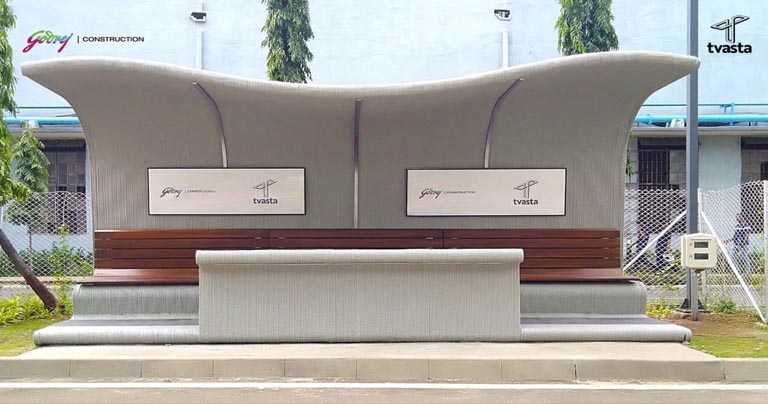
Building information modelling (BIM), construction robotics, modular construction, and the usage of sophisticated building materials are some of the major construction trends that will be widely implemented in the immediate and mid-term, says Abhijeet N Gawde, Head of Business Development & Marketing at Godrej Construction.
How is your organisation complying with the green certification requirements, and what is your overall approach to sustainability in the built environment?
Godrej Construction is a pioneer in adopting sustainable construction practices in India, and we are committed to minimising the impact of construction on the environment. In line with our core values, Godrej Construction (GC) has implemented various initiatives across its lines of business. All our building construction projects are designed using green building principles. Many of our buildings are certified as Platinum- or Gold-rated Green Buildings. Recently, our IT Park in the 02 Godrej Business District (GBD) at Vikhroli, Mumbai, was awarded a Platinum rating for health
and well-being in the built environment by the IGBC.
The 02 GBD IT Park building is a LEED Platinum-rated green building, and the common areas of this building are 100 percent powered by renewable energy. Godrej Construction has received the “Green Pro” certificate from the Indian Green Building Council (IGBC) for their RMC products, such as Enviro TUFF, Xtra TUFF, Easy TUFF, and other construction materials such as TUFF Blocks, AAC, recycled concrete blocks, and pavers, making them beneficial for use in green buildings. Our three RMC plants in the Mumbai-MMR and Pune regions have been commended with the GreenPro Certification by the Indian Green Building Council (IGBC).
Godrej Construction’s (GC) processes are aligned and linked to Godrej & Boyce’s (G&B) Good and Green Policy, which aims to innovate for Good and Green Products (socially and environmentally beneficial products) to have one-third of the business portfolio revenues comprised of Good and Green Products and Services. By implementing circular economy principles in our Construction Materials line of business, we have recycled over 28,000 metric tonnes of concrete debris. The recycled concrete materials from this plant are also used for constructing customised prefabricated concrete products such as box culverts, ducts, and drain covers, which are being used for major infrastructure projects in Mumbai. Because of the locally sourced and higher recycled content of the raw material used, the imbibed efficiency in production, responsible management of water and waste during manufacturing, ensuring zero discharge from the facility, and the high recyclability of the waste product, the manufacturing of these blocks and their product properties are inherently greener than normal concrete or building blocks, effectively reducing the overall negative impact on the environment by use.
We have made an early start to demonstrating our commitment towards sustainable development. We hope many others in the industry will follow in the endeavour to build more sustainable construction products for the benefit of future generations. The industry’s mindset needs to change towards cleaner production of raw materials and better circular construction methods to help reduce the energy intensity and environmental footprint of the construction sector.
What are the procurement challenges faced by the RMC companies, especially while obtaining raw materials?
Cement prices have recently experienced high volatility. An increase in the prices of the raw materials is expected to create margin pressure for the organised RMC players in the market. However, we would continue to provide customer-centric solutions and value-added services. Globally, the construction sector is among the largest consumers of natural raw materials. For an industry vulnerable to problems with raw material supply and price volatility, it does make sense to focus on resource efficiency and the reuse of materials. With construction work on the rise of new buildings and infrastructure projects, the demand for building materials is expected to increase. However, a crisis looms in the construction sector as there is a growing shortage of building materials. Globally, it is now established that adopting an improved construction process could reduce the adverse impacts on the environment and that reusing C&D waste is a viable alternative. Using recycled concrete materials helps reduce the demand for quarrying stone aggregates and natural river sand. Recycling materials and using them in the construction sector can help address
cost escalations as the government embarks on ambitious infrastructure development. As responsible industry players, we make every effort to help minimise the adverse impact of our business
operations on the environment.
At Godrej Construction, we are implementing the principles of “Recover, Recycle and Rebuild” to work for recycling concrete debris to produce prefabricated concrete products such as building blocks, pavers, culverts, ducts, and other customised precast concrete products. AAC blocks, recycled concrete blocks, and pavers offered by Godrej Construction are IGBC Green Pro certified.
What innovations are happening in the design of structures for fast and efficient construction?
The construction industry is leveraging technology to make construction management and site operations more efficient and sustainable. The major construction industry trends that are expected to witness increased adoption in the near to medium term are building information modelling (BIM), construction robotics, modular construction, and the use of advanced building materials. Hence, start-ups and scale-ups are increasingly developing innovative solutions around prefabrication, worker safety, and construction robotics. Construction 3D printing and green building solutions have the potential to significantly reduce the adverse impact of construction on the built environment. Construction 3D printing (3DCP) can enable the faster and more precise creation of complicated and bespoke structures and objects. 3DCP technology could optimise the design of buildings and infrastructure to use fewer raw materials while decreasing labour costs.
Addressing the growing need for improving productivity and sustainability within the real estate and infrastructure sectors, Godrej Construction recently partnered with Tvasta, an indigenous start-up founded by IIT-Madras alumni, to develop a Bus Shelter using 3D printing technology. The bus Shelter was 3D printed within 32 hours and assembled on site within 8 hours, thereby speeding up the construction process that would otherwise take weeks to execute using traditional construction methods. To promote the adoption of circular economy principles in the construction industry, Godrej Construction, along with Tvasta, has developed for the first time a very sustainable concrete mix design comprising approximately 30 percent recycled concrete aggregates(RCA), sourced from concrete waste debris, recycled at the Godrej Recycled Concrete Plant in Vikhroli, Mumbai. In the future, Godrej Construction and Tvasta aim to pioneer 3DCP technology to develop appropriate sustainable infrastructure projects, housing solutions, disaster relief structures, national defence-related applications, and other public amenities in India and globally.
Cookie Consent
We use cookies to personalize your experience. By continuing to visit this website you agree to our Terms & Conditions, Privacy Policy and Cookie Policy.