We deliver what we commit: Sandvik
By Edit Team | April 14, 2018 6:44 am SHARE
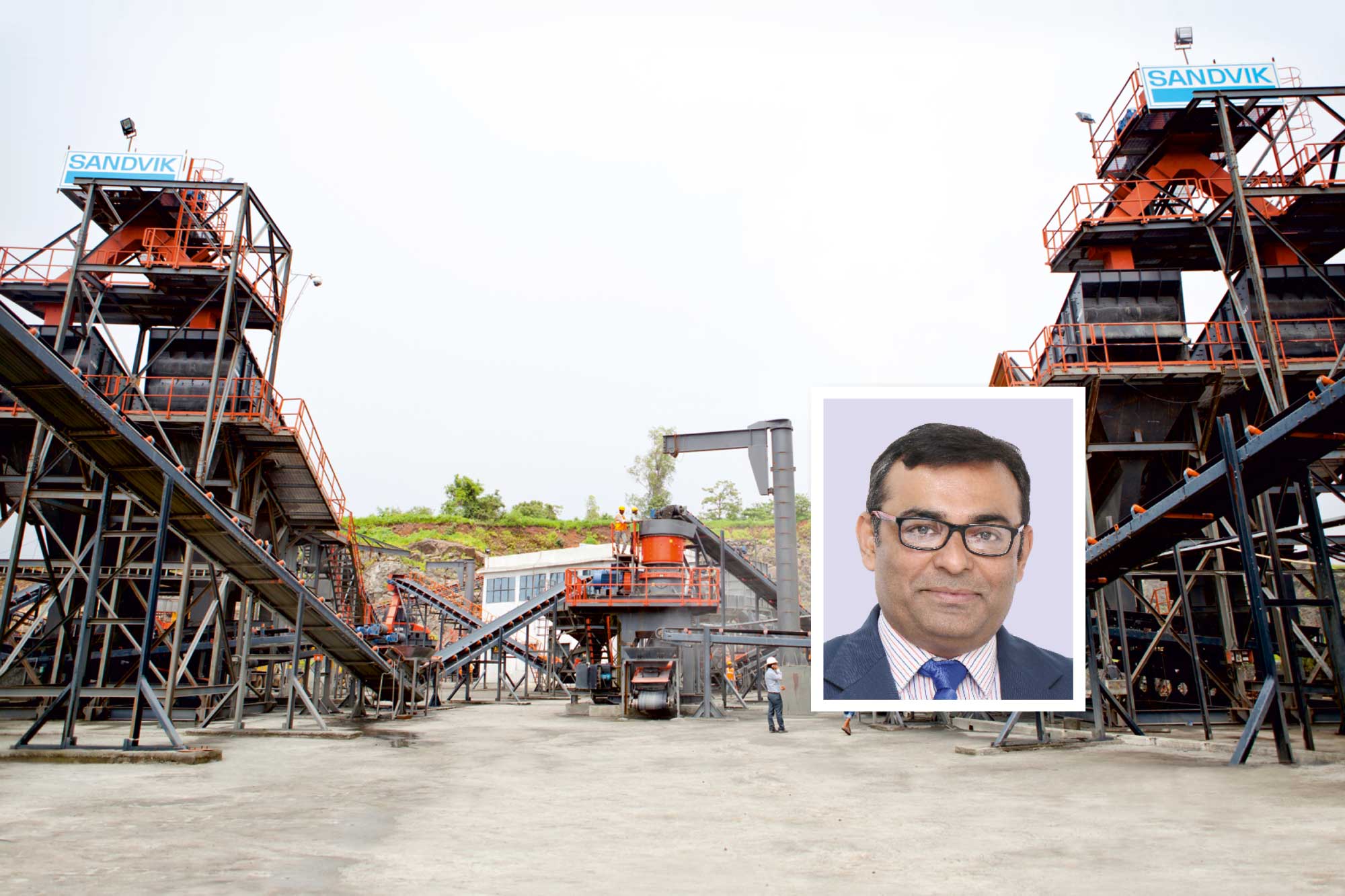
We understand that automation and safety with productivity is going to be future in mining.
Ashoktaru Chattopadhyaya,
Business Line Manager- Crushing and Screening,
Sandvik Mining and Rock Technology
Why is it necessary to embrace tomorrow’s technology for mines of the future?
Sandvik has always been synonymous with high quality and reliable process solution and equipment supply. We deliver what we commit. Excellent technical solution combined with high speed delivery is one of the biggest strength of ours. The focussed solution with reduced cost per tonne of production gives us an edge. We understand that automation and safety with productivity is going to be future in mining. Sandvik has crushers with the latest generation of automations incorporated, thereby making the product safer and maximising their utilisation.
What is your most advanced offering for tomorrow’s mines?
Sandvik has a wide range of crushers for versatile crushing needs in both mining and aggregate sector. Sandvik was the pioneer to introduce Horizontal Shaft Impactors (HSI), in stationary as well as wheel-mounted application which is fully manufactured at our Pune facility.
Leveraging the upsurge in iron ore mining, Sandvik has geared up its state-of-the-art equipment offerings in this sector. We have already developed and started manufacturing the track mounted crushing units in India and the field results are overwhelming. Furthermore, we are geared up to replace the old era big crushers with our latest as well as fully automated CH800 series cones.
Additionally, one of our key contribution in sustainability and advancement, is our state-of-the-art solutions for sand manufacturing and Iron ore fines (beneficiation or palletisation application), we have introduced the latest technology and high powered 500 series crusher models like CH550, CH540, etc. We have maintained our dominance in this sector and see significant opportunities in the coming years.
How to achieve cost-effective crushing and screening?
The key is to analyse the problems together and refer them to dedicated specialists. This approach will lead to improved productivity, lower cost, improved energy efficiency and eventually better profitability.
The challenge to lower the cost per tonne of finished products requires a thorough knowledge of the whole quarrying process, combined with the best equipment, service, support and consumables. Our newly introduced “lifecycle approach” together with innovative “Opti-Agg” software solution has enabled us to maximise the production with required gradation and quality. This has ensured the optimum productivity and customers’ peace of mind till the life of the equipment.
For example, Sandvik VSI unit is unique and has made sand processing possible in three stages of crushing with the introduction of Sandvik CH550 in stationary and mobile applications.
There are several integrated strategies which can improve efficiencies and reduce energy use. Selective blast design, ore sorting, waste removal, advances in modelling and new grinding technologies are just some of the approaches companies are adopting to improve ore grades and cut energy costs.
Thus, the collective usage of the modern mechanised techniques will be of great help to the crushing and screening segment thereby achieving cost and energy efficiency.
What are your best offering in this sector?
Sandvik’s crushing and screening equipment offers the market’s most advanced and complete product range with solution-based approach. This contributes to increased performance and productivity for our customers.
Our partnership concept basically means that our customers will always find us available to discuss their challenges and opportunities.
We are the industry leaders in full plant solution of various range (200 TPH to 500 TPH) which is of great attraction and well accepted in the market. Furthermore, the Gyratory crushers, medium and bigger cone crushers, PriSec range of crusher, Sizers have been well appreciated in the Indian Construction and Mining market. Capacity range starts with 100 TPH and can go up to 3,500 TPH. We have successfully commissioned such plants both for the aggregate industry and mining sector.
Our VSI crushers can produce 100 per cent down <2.36 mm sand known as plaster sand which is a high-quality product. Our HSI can produce from 1000 mm feed size to 100 mm product in single stage for soft rock minerals like coal and bauxite.
Our HSI known as PriSec has unique patented feature which means the primary can be converted to secondary within 3-4 hours on site without additional expenditure. We are the technology leaders and continuously develop enhanced products to meet the growing needs of the industry.
Cookie Consent
We use cookies to personalize your experience. By continuing to visit this website you agree to our Terms & Conditions, Privacy Policy and Cookie Policy.