3D construction printing: The synergy between technological innovation and sustainability
By Edit Team | April 6, 2024 12:20 pm SHARE
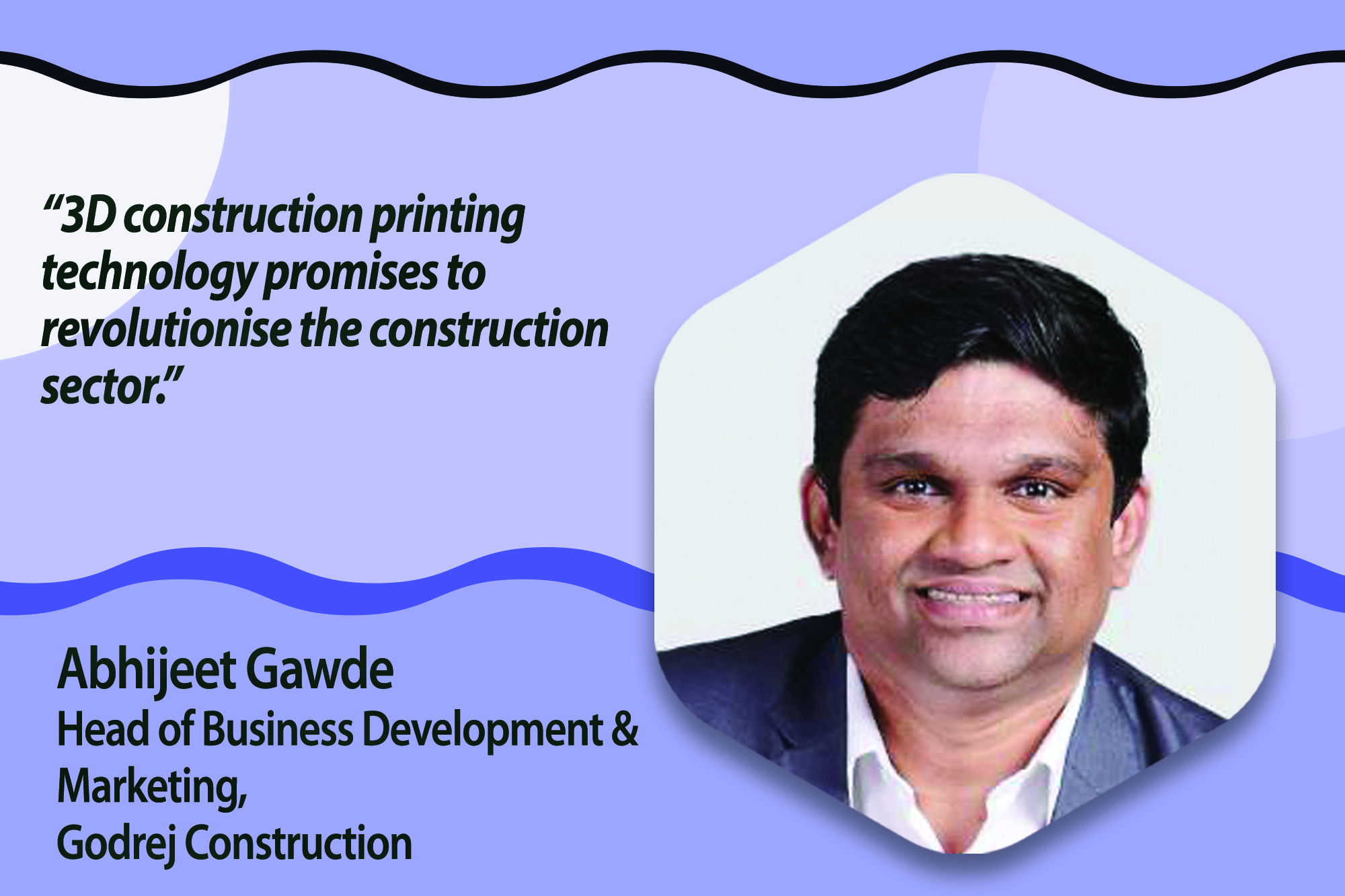
As the construction industry embraces a digital revolution, the emergence of 3D printing technology is reshaping traditional methodologies. With its potential to optimise resource utilisation and minimise environmental impact, 3D printing represents a paradigm shift toward sustainable construction practices.
Technological advancements continue to shape the way we build our world. The industry is strategically pivoting towards innovative materials and state-of-the-art technologies, emphasising elevating construction process quality and outcomes. This strategic shift revolves around key factors such as enhancing efficiency, ensuring cost-effectiveness, and mitigating environmental impact.
The construction sector contributes approximately 20 percent of India’s annual carbon emissions. Recognising this environmental challenge, a concerted effort exists to explore sustainable and alternative construction materials to significantly reduce the sector’s carbon footprint. The Indian construction sector is actively embracing a technological transformation to improve operational efficiency and bolster sustainability. The drive towards innovative materials and cutting-edge technologies signifies a forward-thinking approach that addresses the immediate challenges and long-term environmental concerns associated with construction activities.
3D construction printing technology & collaborative tools
3D construction printing technology holds the promise to revolutionise the construction sector. This innovative technology, also known as additive manufacturing, transforms how we design and construct our built environment, promising a future where architectural designs are only limited by the bounds of our imagination.
3D construction printing technology, combined with collaborative tools like BIM and Lean principles, has the potential to optimise the construction process. We at Godrej Construction recently installed a fully functional office within 40 hours using 3D Construction Printing Technology at the under-development Godrej & Boyce’s Industrial Campus at Khalapur. This was enabled through effective team collaboration integrated with project planning tools like Building Information Modelling (BIM) and Lean Construction methods.
One key advantage of 3D construction printing is its ability to optimise resource use and reduce environmental impact. For instance, in our Khalapur project, we utilised a concrete mix design incorporating up to 20 percent Recycled Concrete Aggregates (RCA) sourced from our own recycling facility at Vikhroli, Mumbai. This not only reduced waste but also addressed concerns about embodied carbon in construction.
3D construction printing eliminates traditional building formwork, allowing for the rapid and cost-effective realisation of concrete structures. Automation and robotics play a crucial role in this process, enabling the precision and efficiency of constructing complex geometries. The resulting structures boast intricate designs and textures that would be impractical to achieve using traditional methods.
We have installed an innovative Solar Tree structure that resembles a tree, generating solar energy during the day using photovoltaic (PV) panels. These solar trees require less space due to their design, allowing for greater power generation per unit area and being ideal for supporting off-grid structures. Additionally, the surrounding area of Cocoon features reed beds, a wastewater treatment system that utilises wetland plants to effectively clean effluent before discharging it back into the environment.
These projects showcase how the combination of Construction 3D printing technology, effective planning tools, and sustainable practices can revolutionise construction methods and contribute to circularity in construction. They offer rapid, cost-effective solutions for areas with significant housing needs and promote eco-friendly commercial establishments. 3D Construction Printing Technology represents a significant step towards creating environmentally conscious structures by reducing waste and incorporating recycled materials.
Industry stakeholders, including developers, are strategically navigating the future by embracing progressive concepts. They are also leveraging the efficiencies of industrialised construction through pre-fab and modular techniques. These measures aim to strengthen projects against future challenges, focusing on sustainability and long-term viability.
Cookie Consent
We use cookies to personalize your experience. By continuing to visit this website you agree to our Terms & Conditions, Privacy Policy and Cookie Policy.