Discover how Bajaj Steel Industries Ltd. melds a rich history of technological advancement with modern Pre-Engineered Building solutions. From earthquake-resistant designs to eco-friendly materials, BSIL is shaping the future of infrastructure with unmatched dedication and excellence.
What inspired Bajaj Steel Industries to become a pioneer in Cotton Ginning and Pressing technology, and how has the infrastructure division evolved to meet diverse industry needs?
Bajaj Steel Industries is the pioneer in Cotton Ginning and Pressing technology in India and is one of the largest manufacturers of Cotton Ginning and Pressing machines across the globe, with exports to more than 60 countries covering almost every cotton-producing country. This growth and position could not be achieved by mere longevity. We have invested heavily in technology upgrades and modernisation and consistent and meticulous monitoring of our product, process, and service quality.
The BSIL Infrastructure division, a backward integration product for our machine lines, is the same in its approach to work ethics. We never compromise on the quality of material, process, and service. We endeavour to provide our customers with outstanding quality products comparable to the best in the world. A testament to this is that our PEB structures stand tall in geographies across Africa, Latin America, and Europe apart from covering most states in India.
The infrastructure division, which initially started with Cotton ginning sheds, has erected sheds for the pharmaceutical, chemical, and oil and gas industries, sheds for the food and beverage industries, packaged food products for exports, indoor sports complexes, multi-floor cold storage, and high-rise buildings, to name a few.
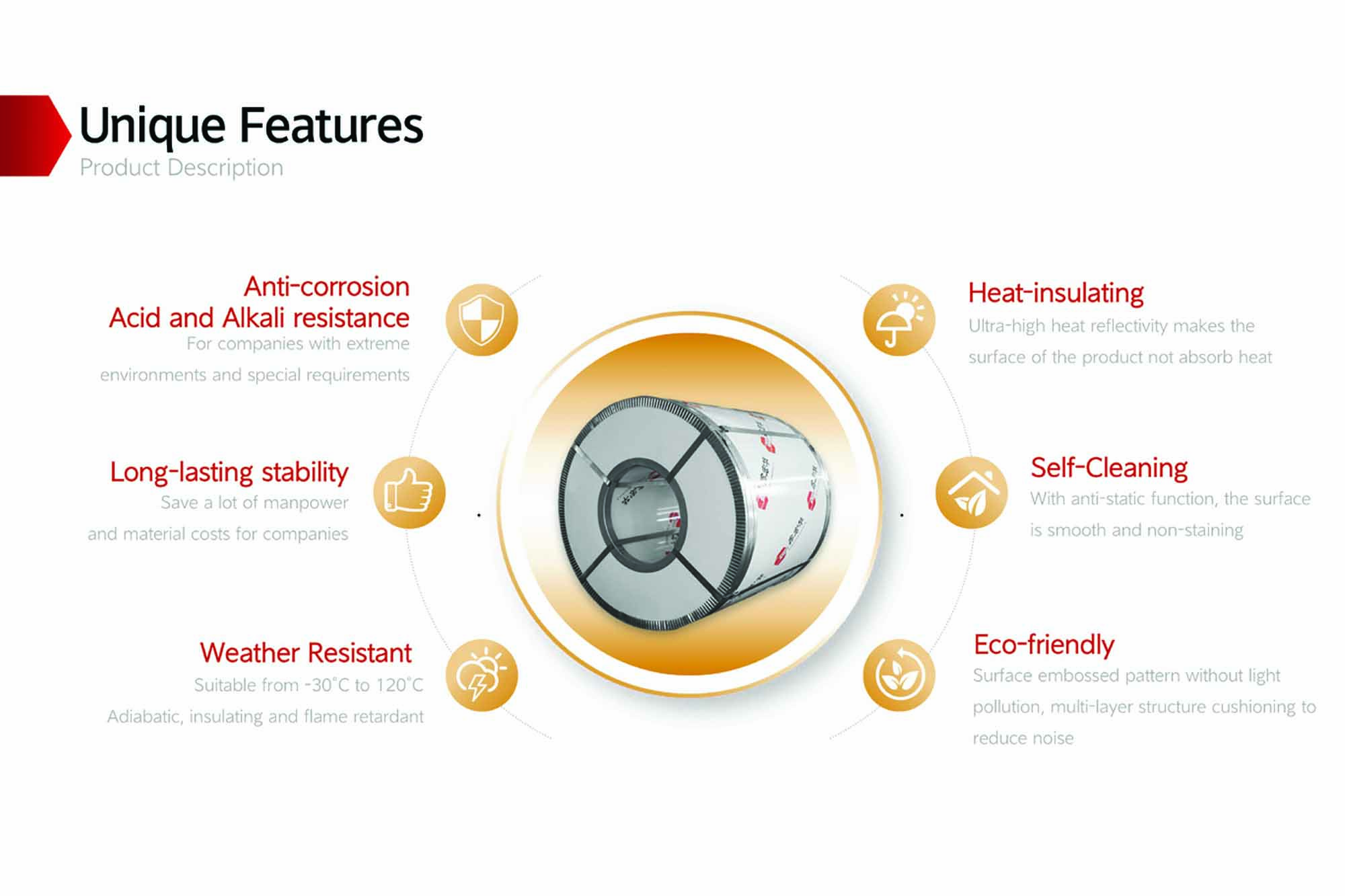
How do your PEB designs cater to the structural challenges of seismic activity and high wind zones?
We use the latest and most sophisticated design solution software, such as MBS2021, Staad Pro, and the like. All aspects of seismic conditions and wind speeds are considered before design is initiated. These are available as per Indian Standards for buildings in India and internationally. We refer to the relevant local standards and available data. No presumptive assumptions are ever made for the design of buildings.
We are proud that all our over 1,000 projects in the last 14 years have remained stable and continue to provide the intended utility to our esteemed customers.
As an environmentally conscious organisation, how do you ensure that your PEB designs and production processes contribute to sustainability?
Our PEB building is a bright example of a green building that can be relocated, reused, modified, and recycled if necessary. On the production aspect, BSIL uses CNC machines that can be directly programmed from the design and detailing software to provide optimum material use and reduce wastage. End pieces are utilised as stiffeners wherever possible. This ensures the use of high-grade tensile steel of E350 grade instead of the commercially used E250 grade and reduces wastage.
BSIL utilises solar power to reduce dependence on fossil fuel-generated power, reduce its carbon footprint, and utilise green energy. Lately, we have started our own Solar Panels and Power division, which helps our customers take advantage of our green energy solutions further to reduce their carbon footprint during the product life.
We have installed a low-friction trolly system for the movement of material, thereby drastically reducing the usage of power for cranes for lifting and moving goods, as well as diesel for hydra and other machinery.
What advanced materials enhance durability in your PEB solutions, and what steel, coatings, or insulation innovations improve building performance?
Only mill-grade prime materials from renowned sources like TATA Steel, JSW, and SAIL are used for all our products, be it machinery, building panels, or doors. We strictly forbid the use of local material or rerolled material. Using prime and virgin material reduces the cost of processing, improves the quality of the product, and gives a longer product life.
We recently introduced a unique sheeting solution in India, “XHH Nano Anti Corrosion Steel Aluminium Composite Cladding Material, ” especially for corrosive atmospheres like chemical plants with highly acidic and alkaline fumes and marine atmospheres. This is an imported product we intend to manufacture in-house in the future. This product is a patented six-layer coated process, with the outermost layer being PET, which helps reduce corrosion of the sheeting material, giving vital extra life and providing high thermal insulation up to 10-12 degrees centigrade.
The new material is designed to withstand extremely corrosive environments where regular PPGI and PPGL sheets wear off quickly. It can withstand salt spray tests for up to 1200 hours, AquaRegia corrosion tests for up to 30 minutes, and Hydrochloric Acid immersion tests for up to 45 minutes. This material is designed for a better life, better heat reflection, and greater anti-corrosion properties.
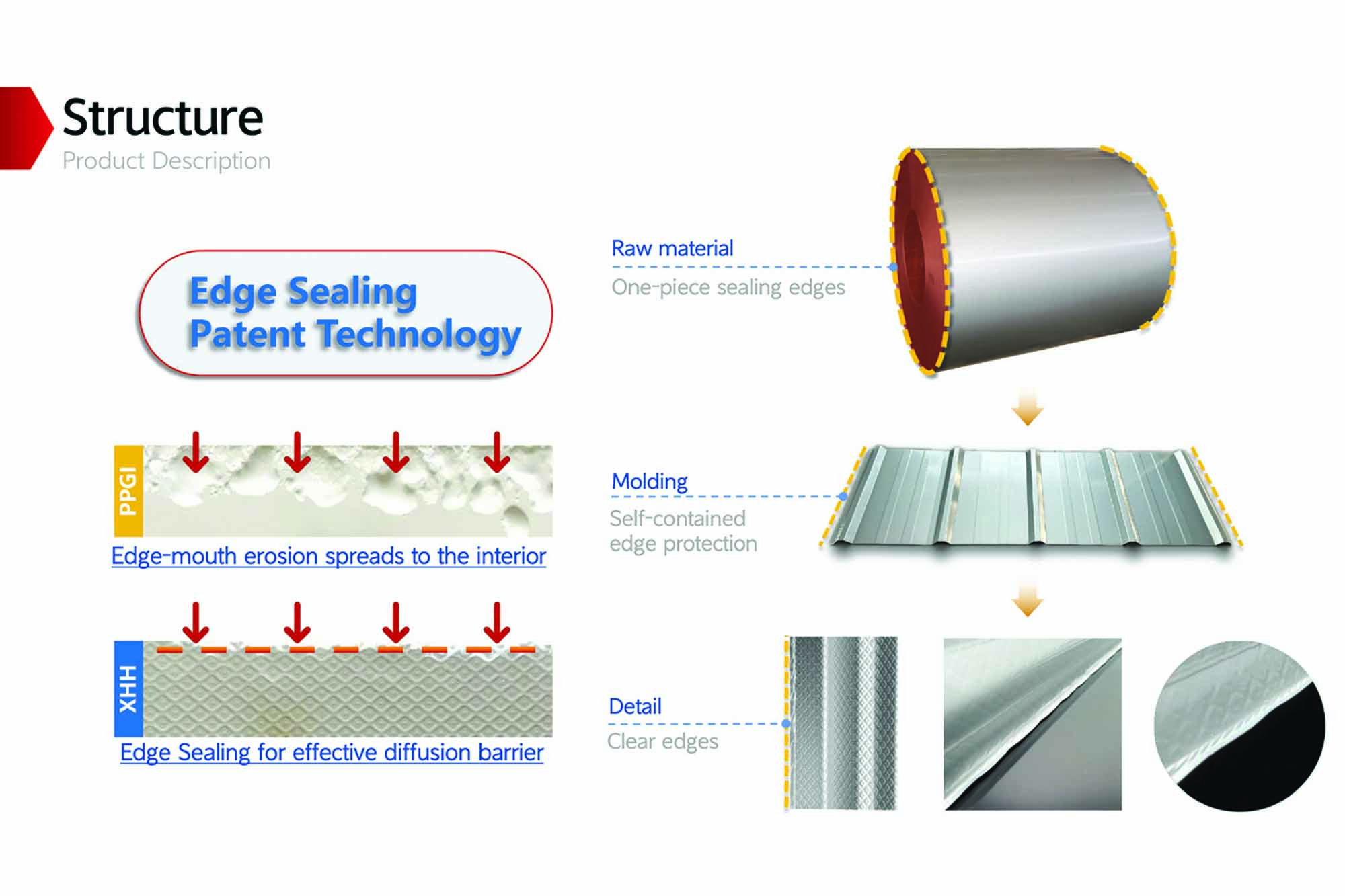
Could you explain the role of advanced technology in your PEB projects, such as BIM, 3D modelling, and automation in CNC fabrication?
As part of our transition to newer technology, we have started implementing BIM in some critical projects for seamless interactions and feedback from different stakeholders. While in its nascence with BSIL, we realise the immense potential that BIM offers and understand that this is the way forward.
Most of the production activities, except for minor fabrication work in the primary members of the buildings, are done on CNC machines, ensuring higher accuracy and minimal manual intervention. The secondary, sheeting, and accessories manufacturing are all based on fully CNC production lines. We are also actively working on setting up an automatic material handling system.
What trends are driving the shift towards pre-engineered buildings in the infrastructure industry, and how do they address rising costs and time constraints?
Pre-engineered buildings are the future of the infrastructure industry. We have seen the scope of PEB increase from industrial and warehouse sheds in the initial days to present high-rise multi-floor structures, hospitals, hangers, residential and commercial spaces, special application products like sports complexes, space and aviation, and many more.
With land prices and the cost of conventional RCC construction rising, in addition to the time constraints, there is a definite shift in infrastructure projects to rely more and more on pre-engineered structures.
This has gotten a further boost, with the government focusing largely on ensuring last-mile availability of goods and essentials to the remotest corners, giving a major fillip to the warehousing sector. The urban infrastructure sector has become cost-conscious and faces massive time constraints, effectively addressed by the PEB sector. Most PEB manufacturers who produce quality products with the desired standards for material and processes are all growing with a healthy CAGR rate in double digits.
For more information, visit: https://bajajngp.com/
Cookie Consent
We use cookies to personalize your experience. By continuing to visit this website you agree to our Terms & Conditions, Privacy Policy and Cookie Policy.