Ammann asphalt plants cater from small PMGSY project to green expressways
By Edit Team | September 7, 2020 9:32 am SHARE
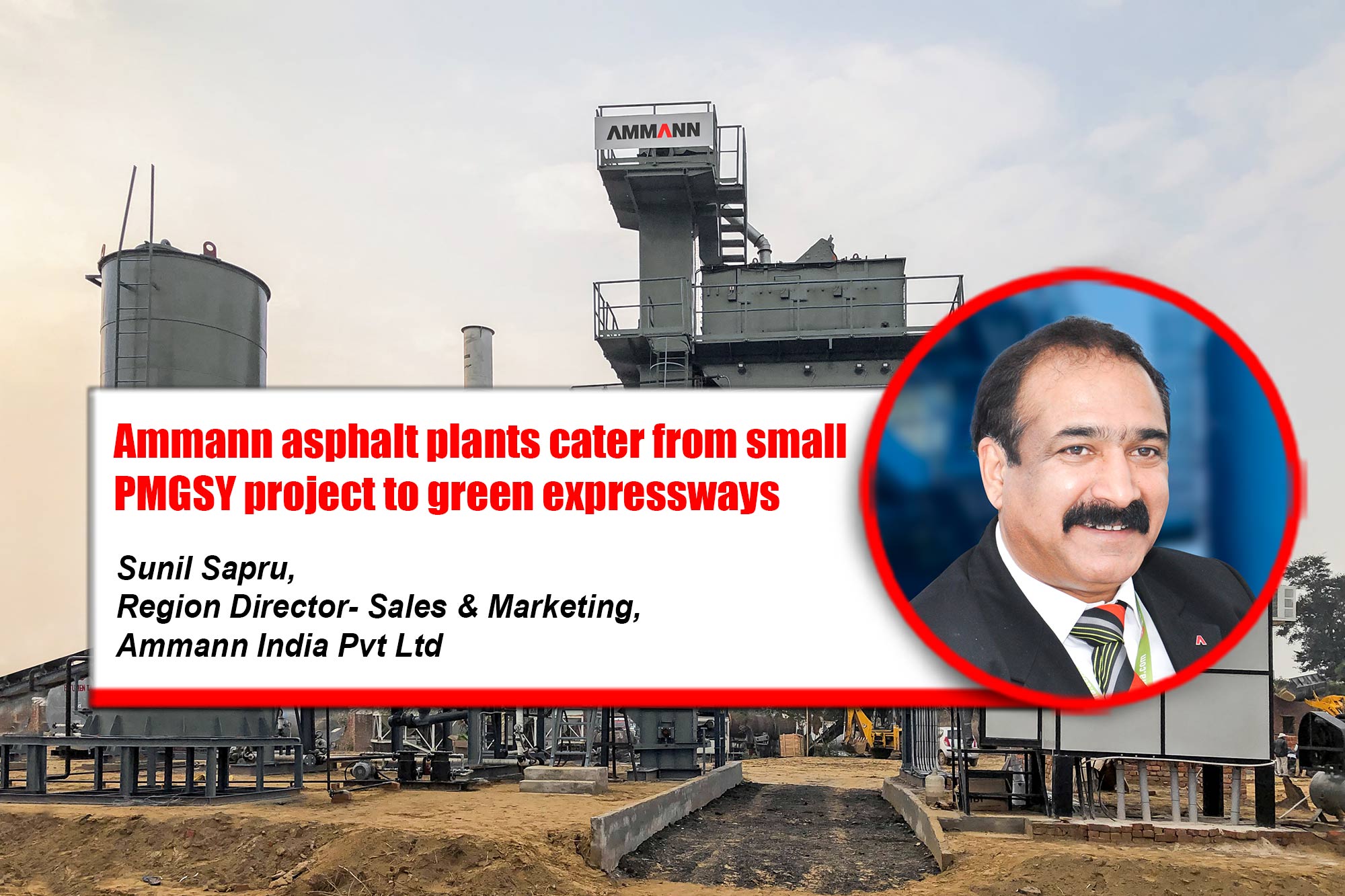
All plants are equipped with advance software operating system, which keeps a tab on high quality precision, data management, print out of each batch, aggregate, bitumen and fuel consumption says Sunil Sapru, Region Director- Sales & Marketing, Ammann India Pvt Ltd.
When it comes to energy efficiency in the process of making hot asphalt, are drum mix plants better suited or do batch plants lead the way?
Given the same site condition for both type of plants and considering the common parameters like aggregate moisture content, final hot mix temperature, heat transfer method inside the drum drive (For example, special design in Ammann plants). The batch mix leads the way in energy efficiency.
When it comes to cost vs capacity, which one is a better choice?
First of all, we have to consider the asphalt mix quality before arriving at the cost and capacity conclusion. Drum Mix plants are usually based on parallel flow heat processing method wherein 70 per cent of the drum is used for aggregate drying and heating, and rest is used for asphalt mixing by injection the bitumen. So, the quality of the asphalt mix is completely governed by the way we control our mix recipe from our feed end. This works on the basis of “good quality in good quality out, garbage in garbage out” whereas in asphalt batch plants the heat process is based on counterflow principle here drum is used only for drying and heating of aggregates, followed by vibrating screen to segregate the required aggregate as per the recipe, each component that is aggregate, bitumen and filler is weighed separately through weighing hopper mounted on the load cells and mix it in the mixer or the pug mill to have consistent mix quality.
Quality-wise, we cannot compare drum mix plant with a batch plant as the batch plant will always stand out not only in asphalt mix quality but also in pollution control, energy conservation, carbon footprints, and complete control on final asphalt mix. (Ammann plants are known for their high quality asphalt mix, the reasonable capital cost with 98 per cent capacity of the plant subjected to site condition).
What are some measures that can be taken for effective energy management in asphalt plants?
Ammann’s state-of-the-art asphalt batch plants’ energy management system is based on three main components of plant i.e. dryer drum and burner, bag-house and exhauster fan. To save energy, all these three units have to work in tandem to create carbon-free aggregate heating which is based on conduction, convection and radiation principle, the suction of right amount and size of filler to baghouse to control the pollution from the plant as these plants are based on green technology and achieve low asphalt mix production cost per ton.
Tell us about your product range, what are the energy saving features of your asphalt plant?
Ammann is the only asphalt plant company in India which has a wide range of asphalt plants which caters right from small Pradhan Mantri Gram Sadak Yojana (PMGSY) project to green expressways. We also have super quick portable plants which could be transported to any part of the country including hilly terrain etc. ready to use in with minimum installation time. All plants are equipped with advance software operating system, which keeps a tab on high quality precision, data management, print out of each batch, aggregate, bitumen and fuel consumption and these plants works on low maintenance and low fuel consumption cost per ton.
Cookie Consent
We use cookies to personalize your experience. By continuing to visit this website you agree to our Terms & Conditions, Privacy Policy and Cookie Policy.