Any link failure can cause significant losses in mining operations
By Edit Team | November 10, 2022 12:46 pm SHARE
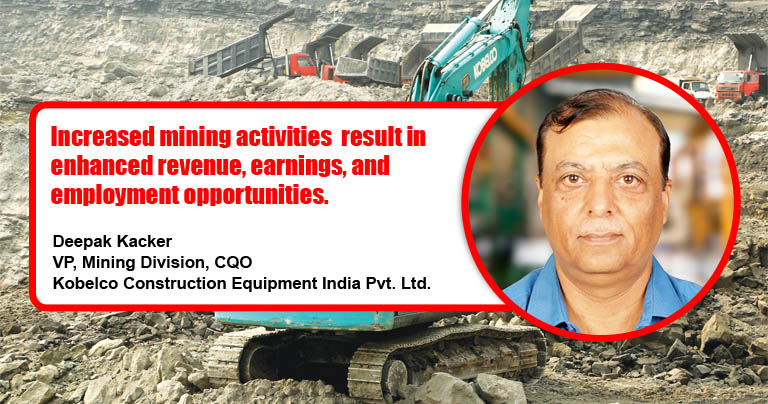
Increased mining activities result in enhanced revenue, earnings, and employment opportunities.
All high-end equipment manufacturers, like Kobelco, are producing sophisticated equipment with such technology and also providing solutions to the industry, says Deepak Kacker, VP – of Mining Division and CQO, Kobelco.
How is the mining sector changing in response to the current infrastructure demand?
Infrastructure demand is at its own pace, but the mining sector is somehow independent and not directly related to the infrastructure development if the logistic and power sectors are kept aside. Coal, cement, iron, and other minerals are major contributors to the mining sector. The infrastructure changes demand more impact on limestone and iron, and expansion to increase cement and steel production is the result, which we have acknowledged since our inception.
Coal is more of an independent sector if we foresee the demand. Since the government took the initiative for mining policy reforms, there has been a noticeable shift in the mining industry, like relaxing mineral exploration norms. The Mines and Minerals Amendment Bill (2015–2021) has introduced various reforms and developments in the mining sector. Changes in technology approach to sustainable business and a changing workforce are all impacting the mining industry. The mining sector will be a key driver of economic development. Increased mining activities result in enhanced revenue, earnings, and employment opportunities. In rural areas, this can also result in increased infrastructure development.
Further, the overall GOI self-reliance approach and initiatives are encouraging. As per our PM’s statement concerning driving the mining economy, “Self-reliance is not possible without a strong
mining and mineral sector because minerals and mining are important pillars of our economy.”
What innovative equipment is used at mining sites to improve operations while protecting the environment?
Innovation starts when you start thinking beyond the possible ways, and we have learned a lot after the COVID pandemic. Earlier electric CEVs were dominant in coal mining sites, with considerable focus on safety. With the abundance of fossil fuels and their ease of usage, such equipment needed to be more consistent. Now, with a focus on emission controls, diesel engines
compatible with green or biofuels and hybrid technology are being discussed.
Currently, unlike the passenger or commercial vehicle industry, the mining equipment industry is not much inclined towards environmental protection, as the GOI has yet to put any strict regulations in place. Still, a few OEMs like Kobelco and other Japanese, US, and European-based manufacturers are committed to environmental health and are focusing on reducing CO2 emissions. Kobelco’s excavators (a subsidiary of Kobelco, Japan) are equipped with Japanese engines and other advanced technologies that are globally proven for fuel savings and low noise and vibration—a kind of operation that maintains a pleasant environment for the operators and the surroundings. SCR, biofuels, and hybrid technologies are also available with Kobelco, Japan.
What are the procurement issues in this industry? How do procurement experts and equipment managers handle them?
Procurement in the mining sector offers unique aspects due to the locations, legislation, mines’ lifecycle, project cost, guaranteed production, and a limited and specified supplier market. Procurement in mining has a multi-directional approach. For cement and minerals, which big corporations and the government primarily operate, procurement actions happen systematically and professionally. All issues are well addressed and curbed by establishing resources and better clarity on various clearances. The government is also keenly examining the environmental implications of coal and mineral exploration while ensuring that the rich mineral resources are exploited adequately for the region’s benefit, boosting their procurement actions. The Ministry of Mines recently stated that the Ministry is focused on increasing the pace of exploration of minerals in the country and on the auction of mineral blocks.
In those sectors where mining is allowed to be given on a sublet basis, like in the coal sector where the removal of coal OB is subject to an extremely competitive atmosphere, finance plays an important role. Issues lie here with the funding to the sub-contractors for the limited-period projects with guaranteed outputs. However, the successful and timely auctioning of the blocks acts as a catalyst to bring other financing sources to the region.
How does downtime of mining equipment impact operations?
Most mining operations are cyclic, and any link failure can cause significant losses as all the links must perform collectively. Like an excavator manufacturer, Kobelco is committed to giving the best performance and consistent and sustainable output. So we have come as a solution provider to keep the equipment in running order. So, such failures are an independent cause, but mining operators consider them essential factors in fleet selection.
What are the preventative and predictive maintenance solutions for mining equipment available?
Predictive maintenance is essential, where machines run almost 80 percent of the day. It predicts failures, one of the industry’s relevant demands because of the cost and value involved. It saves
money and determines the ideal time for performing maintenance activities on equipment to minimise the maintenance frequency and maximise the machine’s reliability.
Everyone would like to work efficiently, and it is possible if you are equipped with the right tools and skills. Currently, with the help of AI and the use of sensors and sophisticated analysis techniques for condition monitoring of equipment fleets, the chances of any failure are minimised. Like Kobelco, all high-end equipment manufacturers produce equipment with such technology and provide industry solutions.
Preventing failures via regular maintenance actions and part replacements in advance is cheaper than repairing unexpected failures, which is breakdown maintenance. But the cost and effectiveness of such an approach to maintenance can be optimised by adopting a predictive maintenance approach. Under this approach, failures are predicted before they happen by analysing equipment data, typically collected via wirelessly connected sensors.
For example, fuel consumption is monitored daily in the Kobelco SK520 (a mining excavator). Suppose a little higher fuel consumption is observed through preventative maintenance undertaken at regular intervals. In that case, the remote analysis of data collected via sensors on the machine vehicle, including the fuel gauge, injection amount, pump regulator response, and its flow and pressure characteristics, can help identify the specific reason for increased fuel consumption. And corrective action is
planned to rectify this during the regular maintenance period.
For a large mine, this translates into lakhs of rupees in savings. The availability of such mining assets directly affects the planning of production capacity. In other words, asset availability has a direct relationship with production capacity. Hence, adopting and executing the correct maintenance strategy has become critical to the success of mining companies today.
What is the state of underground mining in India? What are the most recent underground mining equipment trends?
Statistically, concerning coal, available on the CIL official site, coal mining comprises nearly 75–80 precent of India’s mining activity, and other minerals and metals are limestones, iron, zinc, lead, copper, bauxite, uranium, etc. Out of the total 352 active coal mines, underground mines account for 158, contributing only 7 precent of total output (as of 2020). There may be a lot of factors like safety, DGMS regulations, limited equipment suppliers, etc., due to which it contributes a much lower output compared with the global standard.
If we talk about the underground mining equipment being used, they are universal drilling machines, road headers, miners, haulage, SDL and LHD (loaders), and man-mounted systems.
What are your thoughts on the change from fuel-powered to battery-powered or electrical mining equipment?
It is still under discussion with the Indian government via ICEMA. Manufacturers like Kobelco have the technology available and are just waiting for the guidelines to be put in place by the government.
Cookie Consent
We use cookies to personalize your experience. By continuing to visit this website you agree to our Terms & Conditions, Privacy Policy and Cookie Policy.