Kennametal’s “Digital Twin” solution revolutionises manufacturing by offering virtual models for pre-production testing. This allows early issue resolution and access to advanced CNC programs, enhancing efficiency.
We live in a fast-paced world where new technologies are adopted faster than ever. In manufacturing, specifically in in-part production, we’re observing a transformation due to the ever-increasing use of cloud-enabled, connected data platforms that aid high-volume transactions, interactions, and relationships from hundreds of data sources. These platforms also unify data from multiple standalone sources and present a comprehensive view to support real-time decision-making —today, more commonly called Data-Driven Decisions (DDD).
Customers’ machining requirements are also evolving. These can range from machining a complex 5-axis part with a high machinability index and tight tolerances to prioritising the optimisation of machining strategies to streamline processes, drive productivity, control cost, and reduce waste.
To help customers solve machining challenges, Kennametal uses an innovative end-to-end solution-driven approach called “Digital Twin.”
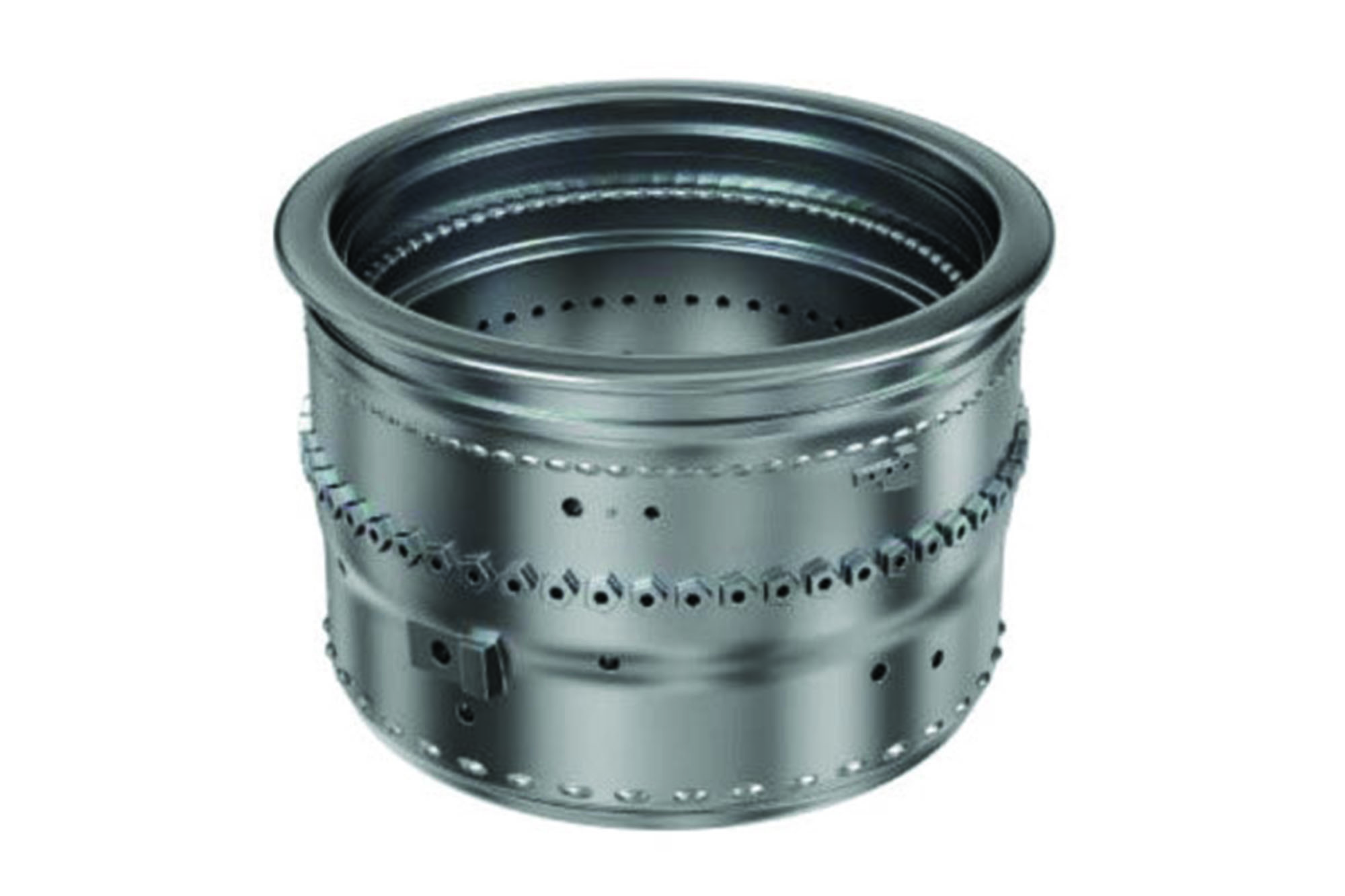
Digital Twin is a blueprint for smart machining.
A “digital twin” is a virtual model designed to represent a physical object or product accurately and precisely. In this case, it can be tested and validated before it is put into production and the market. A digital twin allows engineers and process planners to identify failures before the part goes into production.
Complex multi-axis machines require a deep knowledge and understanding of fixtures, cutting tools, and processes, as well as programming.
Kennametal’s digital twin solution helps customers visualise the complete machining operation in a virtual setting with the proper process parameters so that issues or adjustments can be addressed in the planning stages instead of potentially halting operations later. Digital twin replicas also help translate machining results to performance by allowing for a precise estimation of chipping loss, cycle time, and executable NC codes. The bottom line is that better decisions are made on the shop floor.
With Kennametal and its blueprint for smart machining, customers can create custom tool path simulations and access the latest CNC programs for metal cutting tools and machining strategies while continuing to deliver proven machining and manufacturing solutions.
Kennametal can help take your manufacturing to the next level.
For more information, contact a Kennametal Authorised Channel Partner or Application Specialist or send an email to: k-india-communication@kennametal.com.
Cookie Consent
We use cookies to personalize your experience. By continuing to visit this website you agree to our Terms & Conditions, Privacy Policy and Cookie Policy.