Fluid Coupling
By Edit Team | November 13, 2017 6:41 am SHARE
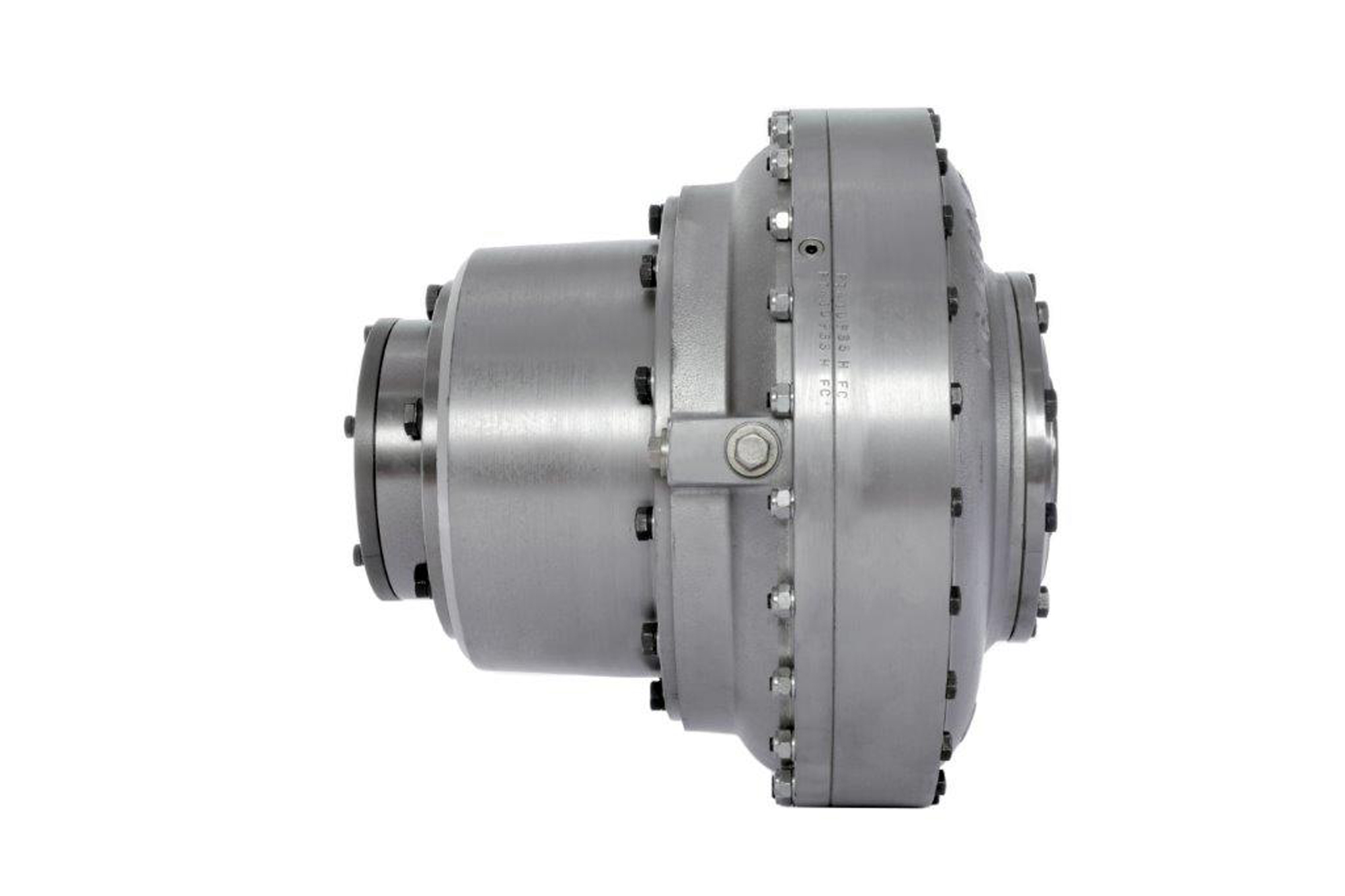
Fluid coupling belongs to the hydro-kinetic group in which power is transmitted by means of transfer of energy through a circulating fluid. The hydro-kinetic transmission was evolved by Dr. Fottinger of Germany around 1905. Harold Sinclair, during 1928, foresaw the application of fluid coupling to industrial drives. Premium Transmission Ltd started manufacturing fixed and variable speed fluid coupling almost 40 years back at Unit III, Aurangabad.
Basic Principles for selection of Fluid coupling are:
Fundamental laws of performance:
Fluid couplings follow the fundamental laws in a similar manner to centrifugal pumps as show below:
- KW a n3 input
- Torque a n2 input
- Torque output =Torque input (under all working condition).
Slip:
The difference between input and output speeds is normally expressed as a percentage of the input speed and referred to as slip i.e.
Slip % = Input rpm – Output rpm X 100
Input rpm
Fluid couplings are selected, so that the slip under normal full speed full load working conditions is usually between 2 per cent to 4 per cent.
At this point it is appropriate to refer to overall efficiency of traction type fluid couplings. Since there are no losses associated with the fluid coupling other than slip and a very small peripheral wind-age factor, then the efficiency can be considered to be proportional to the function (100 – slip %). this statement may be expressed as:
KW output =100-2XKWinputXoutput rpm
100 input rpm
Selection criteria for traction couplings:
A. Hydraulic strength (Kr & Ks)
B. Mechanical strength ( torque )
C. Heating (slip heat against self dissipation)
Over 70 years of research and development experience have developed the most modern circuit of fluid coupling. The working circuit diameters, delayed fill chamber and baffles etc, in each fluid coupling circuit has been so chosen that by changing the amount of oil (within the Ks range) you can precisely control and achieve the stalling of fluid coupling between 140 per cent to 250 per cent of full load torque as required, and at the same time keeping the slip at normal full load speed within 2 to 4 per cent.
In other words with a predetermined quantity of oil filling, you can achieve the following two very important performance characteristics in a fluid coupling simultaneously.
1. Slip at normal full load speed within 4 per cent.
2. Stalling of fluid coupling at any predetermined overload between a range of 140 per cent – 250 per cent full load torque.
It has been already explained separately the innumerable advantages that can be drawn by use of fluid couplings with simple squirrel cage motors and DOL starters for various applications. But against this, the engineers should reckon the cost of slippage. In some of the
poorer quality brands, this loss can be as high as 7 to 8 per cent with relatively little overload protection. But, the manufacturers of repute can claim an efficiency of 96 per cent or 98 per cent, which is equivalent to other mechanical transmission.
Therefore, it is important that customers/consultants specify the application; Motor KW; Actual KW/torque required to be transmitted through the fluid coupling; Rpm input; Precise stall torque and slip etc, so that our engineers at various offices throughout India can help you in selecting the right size of fluid coupling and the quantity of oil filling required. In some cases torque speed characteristic curves of motors are also essential to match with fluid coupling curves. It should also be borne in mind that fluid coupling selection should be on the basis of actual KW transmission and not on motor prime mover KW.
A. Hydraulic strength :
Considering idealised flow conditions the KW /HP work input to the impeller of a fluid coupling is proportional to
KW a N3 x D5 where D = working Circuit diameter
In other words, K = KW
N3 D5
Or, K= T X 190.5
N2 D5
This K is stated as the specific load factor
Hence Kr =Tr X 190.5 and Ks =Ts X190.5
Nr2X D5Ns2xD5
Kr = specific load factor with coupling running
Ks = specific load factor with coupling stalled.
Tests have therefore been carried out on various sizes of fluid couplings over a range of the input speeds, torques and slip so that a curve can be plotted connecting the proportionality factor K and the slip across the fluid coupling. A typical relationship is shown below for a modern design of circuit and operating with a constant oil quantity.
B. Mechanical strength
It is also important to check the shaft sizes etc to ensure that the coupling is mechanically strong to transmit the torque. The maximum rated torque for each coupling can be furnished on request.
C. Heating
Having checked hydraulic and mechanical strengths, heating of the coupling should also be checked for specific applications where number of starts and stops are more or for heavy inertia drives.
Normally in a traction coupling the only loss is considered is heat loss due to slip.
Heat loss due to slip = Slip heat = KW running X slip
Self dissipation
It is the heat that can be dissipated by the coupling to its surrounding while running. This depends upon the following factors:
Area of the coupling casing
Thermal conductivity of the material
Temperature rise acceptable, which is generally 1200 F over an ambient of 800 F.
It is always to be checked that:
Self-dissipation >> slip heat
In case of applications where large number of starts and stops are involved (like crane application etc) heating during total duty cycle (i.e) Heating during acceleration time should also be taken into account in addition to slip heat during running. For heavy inertia drives like crushers, ball mills, centrifuges etc. From WR2 or GD2 value of the machine, the acceleration time and heating thereof should be calculated and on that basis number of permissible starts and stops should be evaluated.
Hence it is important that for these application customer or consultants should specify the duty cycle of the machine as also its WR2 or GD2 values.
We have now very briefly dealt with selection criteria of traction type fluid couplings. Hence selecting right type and size of the fluid coupling should also be ensured, its good quality by checking its manufacturing standards, quality controls, casting qualities, ceilings, run outs, alignment and other mechanical features etc. so that it gives desired performance.
(Source: Premium Transmission Limited)
Cookie Consent
We use cookies to personalize your experience. By continuing to visit this website you agree to our Terms & Conditions, Privacy Policy and Cookie Policy.