High performance lubricants for machineries in the mining sector
By Staff Report | August 13, 2024 12:37 pm SHARE
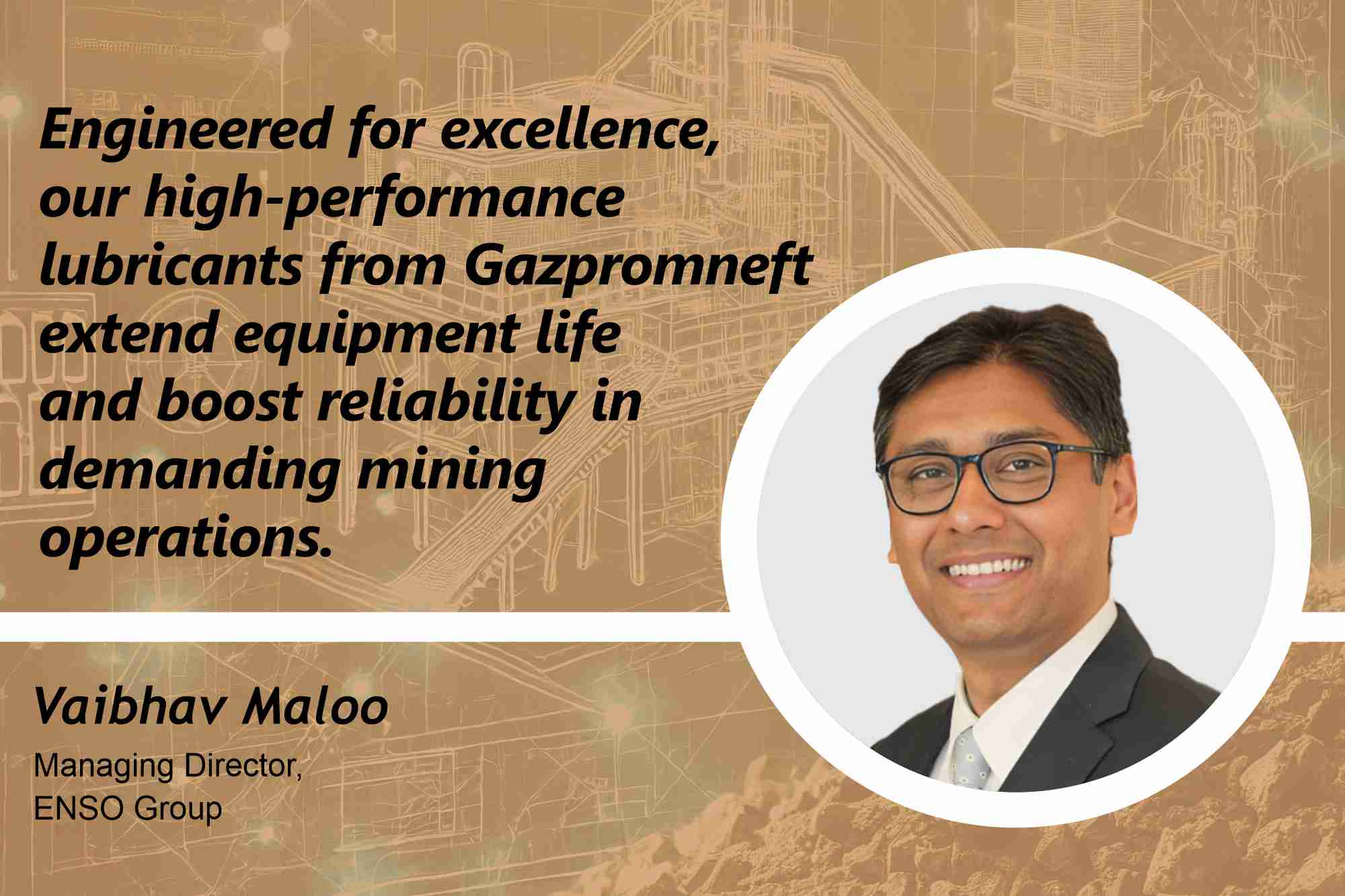
ENSO Group collaborates with Gazpromneft Lubricants to provide high-performance products that improve mining equipment efficiency, extend lifespan, and reduce downtime through innovative engine oils, hydraulic fluids, and other components.
Could you elaborate on the specialised lubricants you provide for mining equipment?
Enso Oils and Lubricants offer various high-performance products from Gazpromneft Lubricants, Russia, specifically designed to satisfy the demanding needs of mining operations. These items improve equipment performance, increase lifespan, and save downtime. Heavy-duty engine oils are engineered with increased thermal stability, a high viscosity index, and modern additives such as detergents and dispersants to reduce engine wear, lengthen equipment lifespan, and reduce downtime by lowering engine failures and extending oil change intervals. Hydraulic fluids have exceptional anti-wear qualities, thermal and oxidative stability, and good water separation and filtration, which protect hydraulic components and provide reliable operation while reducing maintenance and failures. Gear oils containing extreme pressure (EP) additives and corrosion inhibitors protect gears and bearings against wear and corrosion, increasing their life and saving downtime. Greases with excellent adhesion, water resistance, and anti-wear additives protect vital components like bearings and joints from wear and corrosion, decreasing the need for regular maintenance. Compressor oils, noted for their low volatility and thermal stability, as well as anti-wear additives, reduce wear on compressor components, lengthen their lifespan, and require less maintenance as oil life increases.
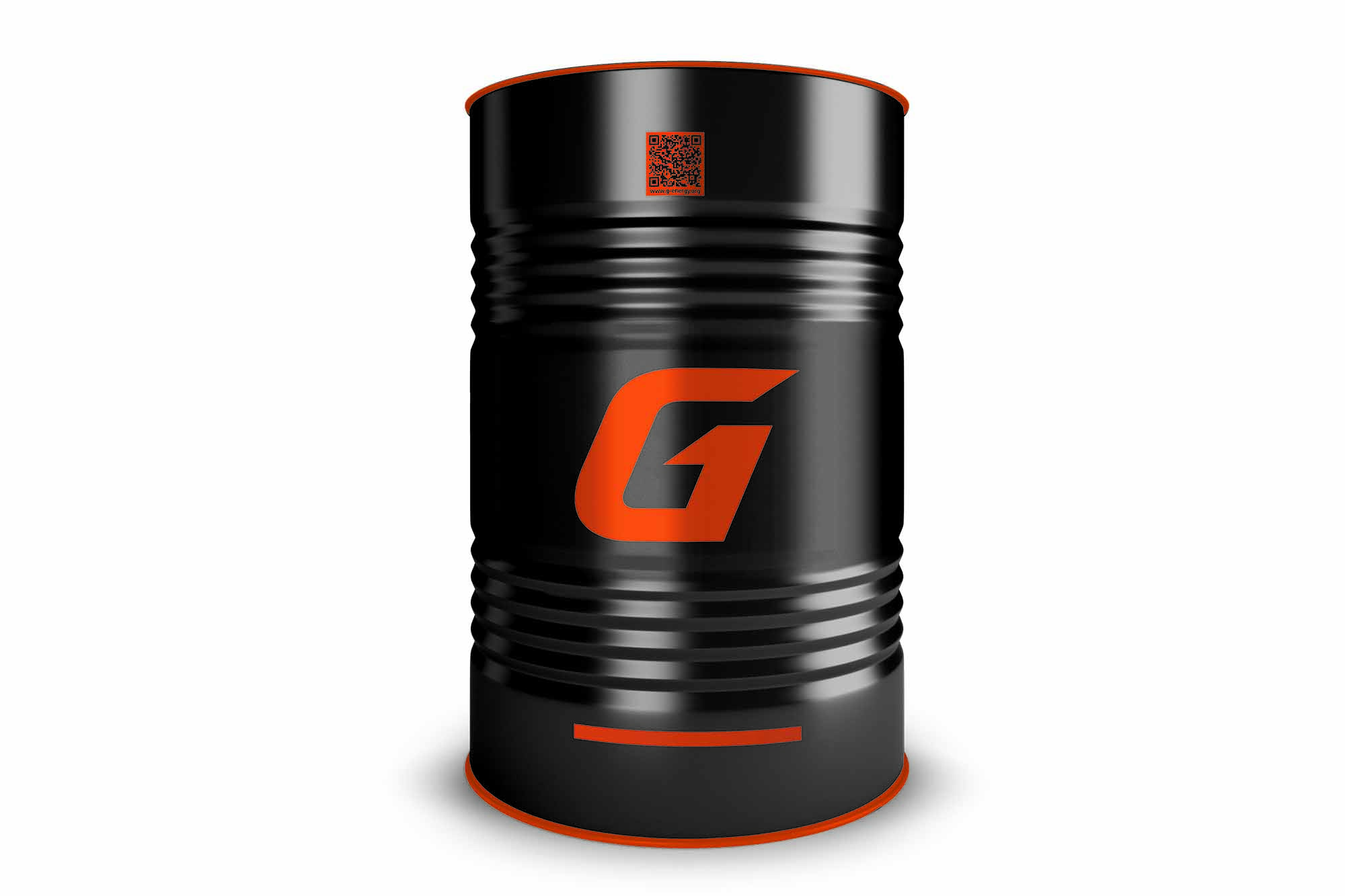
How do ENSO Group cater to the performance demands of these sectors?
Enso Oils and Lubricants provide high-performance products from Gazpromneft Lubricants, Russia, specifically for construction, infrastructure, and mining machinery. These lubricants are designed to withstand large loads, with sophisticated additives that increase load-carrying capacity and minimise wear, increasing machinery life under adverse conditions. Extreme Pressure (EP) additives create a protective layer on metal surfaces, preventing metal-to-metal contact and enabling smooth functioning. Anti-wear technology further decreases friction and wear, hence increasing equipment reliability.
These lubricants thrive in demanding settings because of their thermal stability, which allows them to maintain viscosity and performance across a wide temperature range. They also provide oxidation resistance, which prevents the production of sludge and varnish, and water resistance, which ensures efficacy in wet and humid settings while also protecting against rust and corrosion.
Furthermore, the lubricants are intended to control impurities by repelling dust and dirt and are compatible with various filtering systems to ensure smooth operation. Its improved lubricity improves the life of bearings, gears, and hydraulic systems, whereas anti-corrosion additives protect metal surfaces in wet or chemically exposed settings.
Can you discuss the impact of high-performance and synthetic lubricants on the machinery’s energy efficiency and thermal management in mining operations?
High-performance and synthetic lubricants improve energy efficiency and thermal control in mining operations. For energy efficiency, these lubricants decrease friction and wear. High-performance lubricants with modern additives enable smoother operations and lower energy consumption, while synthetic lubricants provide stable lubrication due to their homogenous molecular structure. It also increases the viscosity index, ensuring appropriate thickness across temperatures and lowering energy loss. Furthermore, they improve load-carrying capacity with extreme pressure additives and the ability to take larger loads without failure, resulting in reduced mechanical losses.
High-performance lubricants carry heat away from important components, whereas synthetic lubricants provide superior thermal conductivity for efficient heat dissipation. Their oxidation resistance minimises sludge and varnish formation, ensuring thermal control. Their long lifespan and resistance to thermal degradation eliminate the need for frequent replacement. They also reduce operating temperatures by minimising friction and wear, resulting in more consistent performance and cooler machinery.
These benefits improve machinery performance by providing smoother and more reliable operation, cost savings from reduced energy use and extended lubricant life, increased equipment lifespan, and reduced downtime due to fewer breakdowns and maintenance requirements, all leading to higher productivity.
How do you foresee enhancing support and services for the construction equipment and mining sectors in lubrication needs and technical support?
The partnership between ENSO Group and Gazpromneft-Lubricants aims to improve lubrication solutions and provide technical support for the construction and mining industries. This collaboration broadens the product portfolio with high-performance lubricants like engine oils, hydraulic fluids, gear oils, and greases, leveraging Gazpromneft’s R&D expertise to create unique formulas that provide improved protection and efficiency. It improves supply chain and distribution by implementing effective logistics and local warehousing, resulting in prompt delivery and easy access to items. The cooperation focuses on sustainability and compliance by conforming to local and international standards. A dedicated helpline for technical support, emergency assistance, and a comprehensive feedback mechanism for continual improvement demonstrate a customer-centric attitude. Additionally, the collaboration will involve participating in industry events to educate and create awareness about the most recent goods and technology. This collaborative endeavour seeks to provide enhanced lubrication solutions, improve equipment performance, and increase operating efficiency in the construction and mining industries.
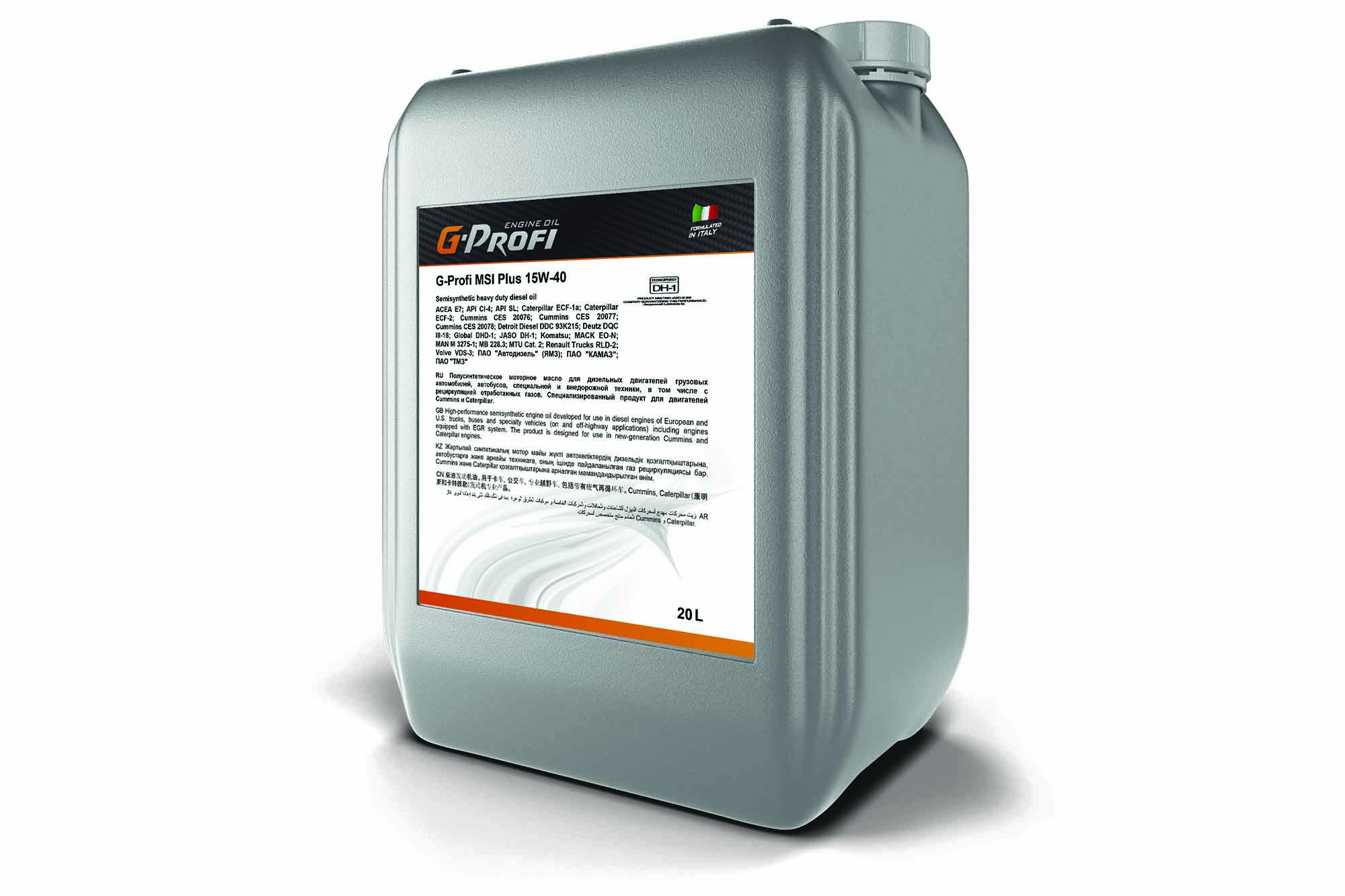
How do you ensure lubricants comply with environmental regulations and sustainability standards, particularly in sensitive environments such as mining sites?
Enso Oils and Lubricants are committed to ensuring that its products, which Gazpromneft Lubricants supply, are environmentally safe, especially in sensitive locations like mining sites. The lubricants comply with local and international environmental requirements, such as ISO 9001, 14001, and 45001 standards. They come in bulk packaging to reduce waste, and suitable disposal instructions are supplied to prevent contamination. We also invest in R&D to reduce environmental effects during production and disposal. The corporation prioritises training teams in optimal environmental standards and spill response protocols. In addition, we work with industry leaders and environmental organisations to stay current on rules and implement best practices.
What role does tribology play in reducing wear and friction in critical components of mining machinery?
Tribology, or the study of interacting surfaces in relative motion, is critical in reducing wear and friction in mining machinery, which improves efficiency, reliability, and lifetime. Understanding various wear mechanisms, such as abrasive, adhesive, fatigue, and corrosive wear, allows the selection of materials with optimal hardness, toughness, and corrosion resistance. Lubrication science contributes by using lubricants to build protective coatings, distribute heat, and remove pollutants; modern lubricants, such as synthetic oils and those with EP and anti-wear additives, provide improved protection. Surface engineering enhances wear resistance with hard coatings and surface texturing, whilst material composites with integrated lubricants increase durability. Friction reduction controls sliding, rolling, and fluid friction by carefully selecting and applying lubricants. Tribological testing and monitoring, which includes lab simulations and field tests, validate performance and detect early wear indicators using wear particle and vibration analysis. The tribological design prioritises optimising component geometry and bearing selection, integrating lubrication systems, and utilising sophisticated seals to prevent contamination. Economically, these techniques cut maintenance costs, lengthen component life, reduce downtime, and improve energy efficiency, resulting in lower operational expenses.
For more information, visit: https://www.ensogroup.com/
Cookie Consent
We use cookies to personalize your experience. By continuing to visit this website you agree to our Terms & Conditions, Privacy Policy and Cookie Policy.