Membrane Bioreactor delivers superior water quality and process control
By Edit Team | July 22, 2017 5:30 am SHARE
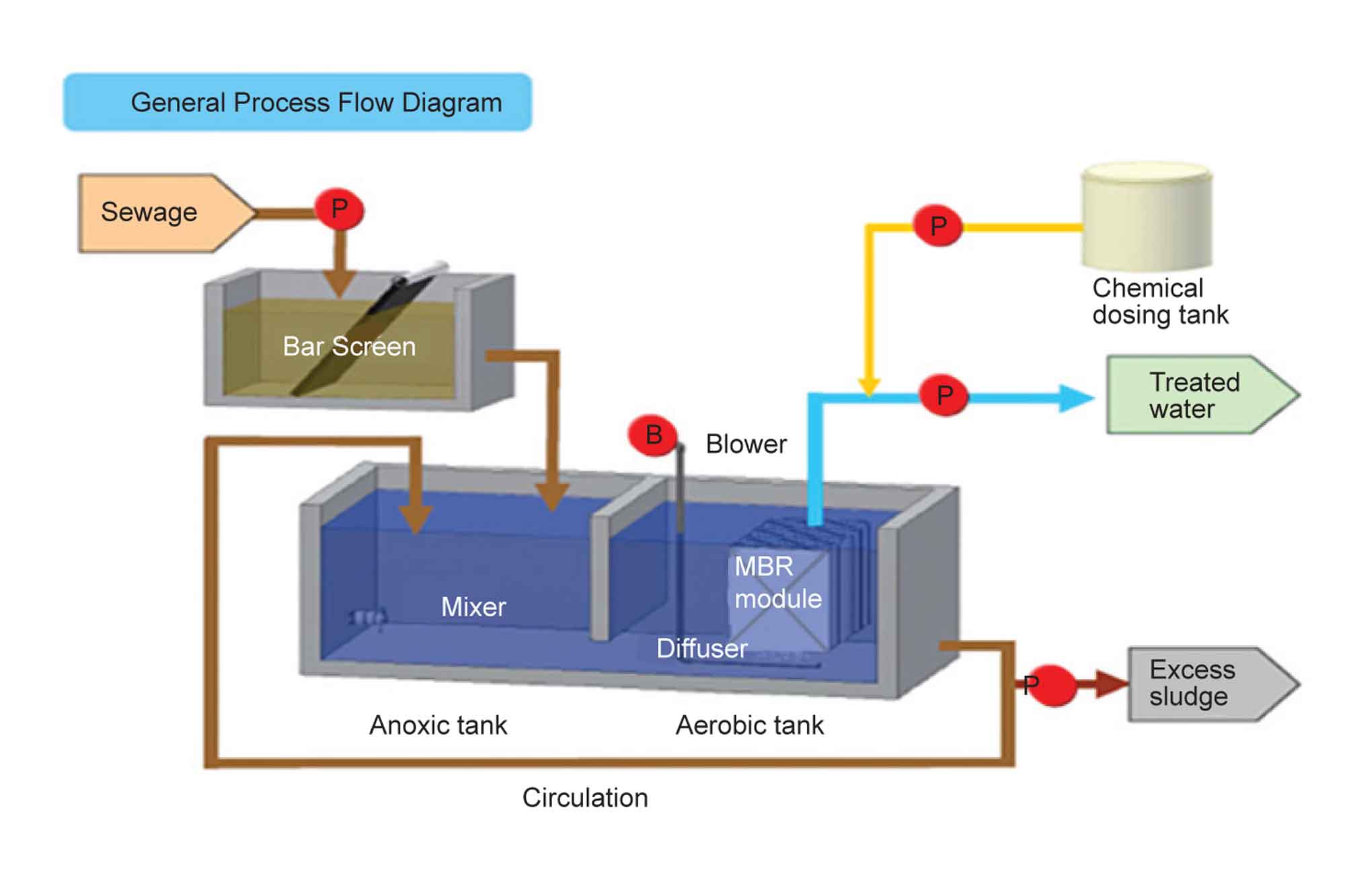
A membrane-based technology for wastewater treatment
In today’s scenario of a growing population and shrinking availability of fresh water, water shortage has already assumed alarming proportions in India and is worsening. With tighter environmental norms by pollution boards and restrictions on usage of ground water, water conservation is gaining momentum across the country and recycle/ reuse becoming inevitable and extremely crucial.
New technologies that are environmentally friendly and sustainable have emerged over time to treat and recycle water, with much less space requirement and minimal chemical usage. Membrane Bio Reactor (MBR) is one such membrane-based technology for wastewater treatment that is far superior in terms of water quality and process control.
MBR a modified activated sludge process
MBR is a modified version of the conventional Activated Sludge Process (ASP). Whilst ASP has a secondary clarifier followed by media filters and then ultra-filtration membranes, MBR completely eliminates the tertiary treatment process. The treated water after MBR is highly superior and can be directly used for recycling. Further, the points of operations in MBR technology are drastically reduced, which saves space by up to 30 percent and results in 50 per cent reduction in power and chemical usage. This gives MBR a definite edge over conventional technologies.
Process advantages
MBR works at a higher Mixed Liquor Suspended Solid (MLSS) of more than 8000 mg/l as against 3000 mg/l in conventional systems (due to limitation of secondary clarifier). This ensures complete removal of dissolved BOD and COD which in turn gives superior product water quality after MBR. Complete de-nitrification can be achieved in MBR as sludge retention time (SRT) is longer which in turn reduces the nitrates in product water.
Other tangible benefits
MBR based wastewater treatment systems result in a reduction in purchase of tanker raw water by 70 per cent, which translates into a saving of approximately ` 10,500/day for a 100 KLD plant. The tanker raw water is procured for cooling tower makeup and for flushing purposes.
One of the most reliable and robust technology
MBR is the most reliable and robust technology available today compared to all other existing wastewater treatment processes. It saves space, money, and energy. In today’s times of water scarcity, MBR can play a pivotal role in recycling water and saving fresh water consumption.
Why Choose QUA’s EnviQ submerged ultrafiltration membranes?
State-of-the-art technology from the USA.
Headquartered in the USA, QUA is the only company that manufactures membranes in India, providing seamless pre-sales, commissioning and servicing support.
Cost comparisons of various technologies
MBR being a robust membrane, the feed limiting conditions can be flexible and beyond the conventional limits. As the points of operations get reduced in MBR, power and chemical consumption also reduce considerably when compared to conventional systems.
QUA’s EnviQ membranes have been specially developed to improve the ease of operation and maintenance of MBR systems. EnviQ’s innovative design offers ultrafiltration quality product water with a stronger and more rugged PVDF flat sheet membrane. EnviQ’s unique features such as reverse diffusion and specially designed air diffusers maximise scrubbing efficiency resulting in reduced cleaning.
• Frameless design – no dead pockets, ensures minimal fouling
• Small size cassettes (0.5m membrane height) – easy cleaning and installation
• Pore size 0.04 micron – UF quality water
• Less number of permeate connections – easy installation and maintenance
• No forced backwash – saves backwash pump cost thus saves energy
• We Make In India – local technical support and quick delivery
• Consistent spacing of 2 mm between membranes – ensures highly efficient air scouring, reduces fouling and chemical cleaning
• Proprietary air diffuser design – ensures effective cleaning.
Authored by –
Karthikeyan Kanakabal
Manager, Sales and Business Development, Qua Water Technologies.
Nidhi Wagh
Manager, Sales and Business Development, Qua Water Technologies.
Cookie Consent
We use cookies to personalize your experience. By continuing to visit this website you agree to our Terms & Conditions, Privacy Policy and Cookie Policy.