Explore the intersection of efficiency and reliability in resource extraction with Caterpillar’s groundbreaking solutions. From fuel-efficient excavators to proactive maintenance strategies, uncover how Caterpillar empowers industries to optimise their extraction operations.
Caterpillar recently launched a new series of excavators, offering increased fuel efficiency and reduced maintenance costs. Can you elaborate on the key features and innovations incorporated?
Recently, we have launched Cat®350, 374 and 395 Excavators. These products are equipped with the best-in-class technology, which can help increase productivity, provide better cost efficiency, enhance safety, and offer more customisable features than their predecessors to meet the multi-functional requirements of customers. This new range of products is in addition to the existing models of Cat 313, 320, and 323 range of excavators. Our excavators are designed to increase operating efficiency, lower fuel and maintenance costs, and improve operator comfort. These machines come with a high-ambient capability of 52°C (125°F) and a cold start capability of -18°C (0°F). An optional -32°C (-25°F) cold start is available for extreme cold conditions. The Swing Assist technology of the excavators automatically stops the excavator swing at defined points during truck loading and trenching, reducing fuel usage and improving cycle times.
Sustainability is deeply ingrained in our technology development strategies, extending seamlessly into our New Product Introduction (NPI) process. Our unwavering commitment is to not only meet but surpass our customers’ expectations while ensuring that our innovations harmonise with environmental and sustainability objectives. Designed with a comprehensive understanding of our customers’ needs, our excavators are a testament to this ethos.
Recent advancements underscore our dedication to enhancing overall efficiency and productivity within our customers’ operations. Our focus on fuel efficiency is exemplified by developing engines that adhere to the latest emissions standards while consuming less fuel. These engines decrease operating costs and contribute to improved environmental performance. Additionally, we offer engines capable of running on blended fuels like ethanol and petrol, with the versatility to accommodate biodiesel, providing economic and ecological benefits. Furthermore, our compliance with Bharat Stage V (BSV) emission norms in India underscores our commitment to environmental stewardship.
Innovative solutions like advanced telematics have become integral to our approach, leveraging big data to deliver substantial customer value. Our tamper-proof product link device, equipped with anti-theft protection, enhances security and aids in the recovery of stolen machines. By harnessing data and transforming it into actionable insights, we empower our customers to optimise equipment utilisation, minimise downtime, and enhance overall efficiency. Real-time monitoring capabilities enable proactive maintenance, further reducing operational costs.
Introducing electrohydraulic systems into our excavators signifies another step towards sustainability and operational excellence. This technology reduces fuel consumption and maintenance expenses and enhances operational control and efficiency. By providing flow on demand to activate hydraulics, the system minimises energy waste and the potential for leaks, aligning with our commitment to sustainable practices while delivering tangible benefits to our customers.
How does Caterpillar ensure that its equipment meets customers’ evolving needs and supports timely project completion?
At Caterpillar, while our machines symbolise power and longevity, our people are the true force behind this reputation. Over 3,000[1] engineers currently work at the Caterpillar R&D Centre in India, investing in areas with the most potential to create value. Our engineers are at the core of our R&D centre, offering diverse engineering expertise—mechanical, hydraulics, electronics, software, autonomy, and more. Our expansive footprint today comprises the company’s second-largest concentration of engineers worldwide.
We are committed to understanding and meeting customer needs at every stage of the equipment lifecycle, emphasising safety and efficiency. We aim to design and develop best-in-class, 360-degree solutions for our customers.
Our technology strategy is intricately tied to understanding the long-term operational environments of our machines. Through careful assessment, we tailor our focus towards innovating smarter solutions to address specific customer needs. Recent strides in this direction have significantly enhanced our customers’ ownership experience.
Connectivity[2] is a cornerstone of our progress, with over 1.5 million assets now seamlessly integrated into our network. This number expands daily, affording us an ever-growing wealth of data. This abundance of data empowers us to adopt an even more customer-centric approach, aiding customers in bolstering safety measures, enhancing productivity, minimising downtime, and optimising asset utilisation.
Our suite of equipment management tools offers customers invaluable insights, enabling them to mitigate unplanned downtime and amplify productivity. Providing visibility into asset usage and location, these tools empower customers to streamline processes, whether procuring parts or requesting services.
Condition monitoring remains a linchpin in our service offerings, with Cat dealers leveraging advanced tools and insights to proactively recommend service interventions, thus ensuring customers’ equipment operates at peak efficiency. Backed by extensive proprietary equipment knowledge and industry expertise, our dealers assume the role of trusted advisors, proficiently monitoring the health of customers’ assets, even amidst mixed fleets.
Incorporating digital intelligence, our lead and opportunity management systems prioritise and recommend tailored solutions to customers, delivering timely and precise interventions. This proactive approach enhances service delivery and drives productivity gains while curbing unplanned downtime, ultimately fortifying our commitment to customer satisfaction.
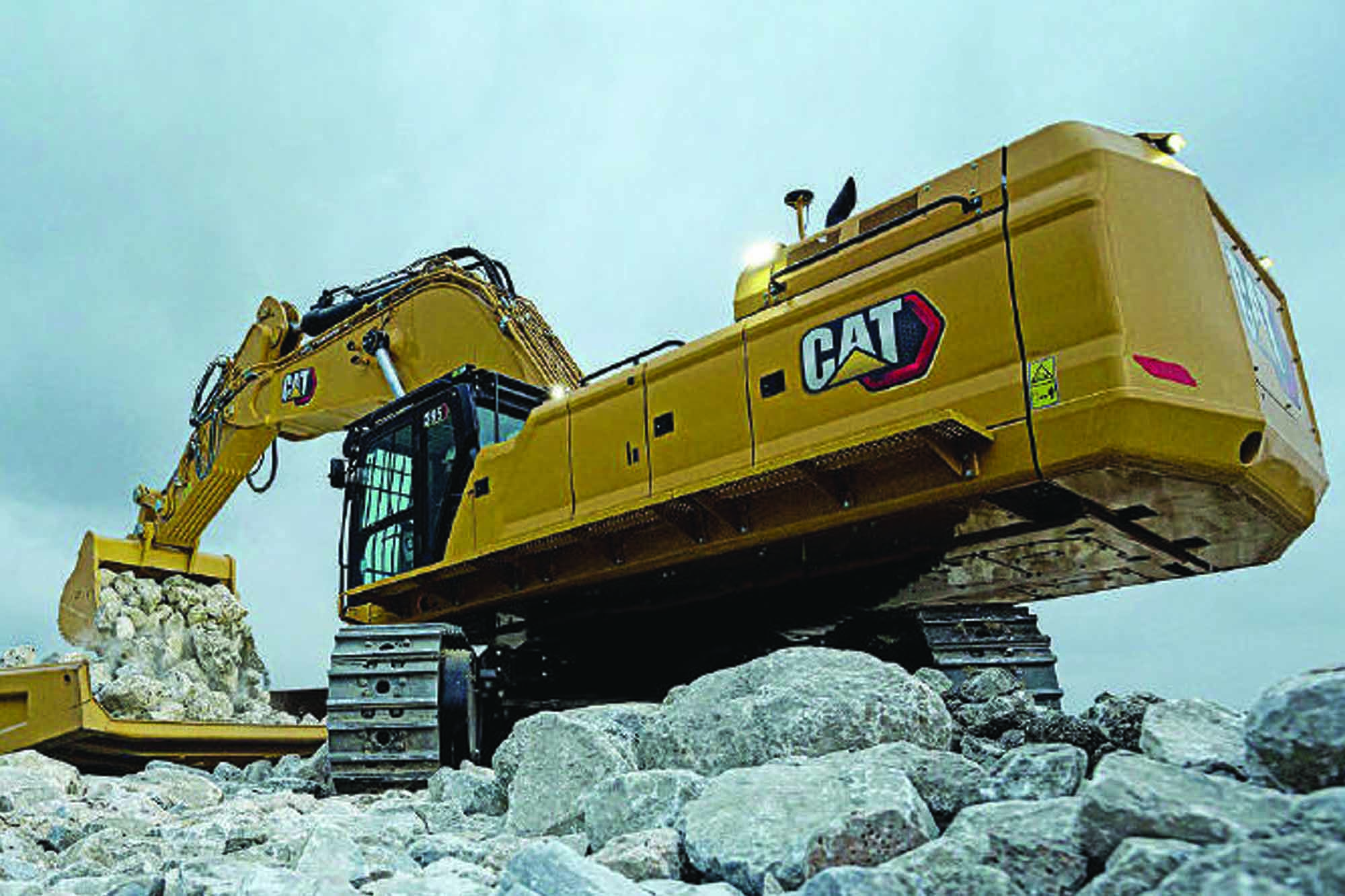
How does Caterpillar’s commitment to sustainability align with its efforts to develop customised plans?
Caterpillar is committed to sustainability by offering integrated and differentiated solutions that help our customers achieve the optimal product and job site energy lifecycle, allowing them to maximise value and minimise their total operation costs. We offer ‘Aftermarket Performance Customer Value Agreements’ (CVAs) to support hassle-free service to customers at any point in the machine lifecycle to help maximise machine performance and utilisation. This includes dealer technician support using genuine Cat parts for certain planned maintenance and fluid health management to help identify issues before they cause unexpected downtime. Customers can contact their dealer to learn more about CVAs and other offers. Long-standing Cat dealers Gainwell Commo Sales India Pvt Ltd (GCPL) and Gmmco Ltd have all the technical information, training, and access to the latest updates to provide reliable services to our customers. The improved analytical and service capabilities such as telematics, inspections, SOS Services, as well as eCommerce platforms like www.parts.cat.com and other dealer-specific mobile applications are making it easy for our customers to own, operate and maintain the equipment at the click of a button.
Our Cat Financial services help customers make the best choice to support their business no matter how big or small, whether it be for new or used Cat machines or repair/ rebuild options to keep their current machines operational. Cat Financial provides retail and wholesale financing solutions and extended protection products to Cat customers and dealers for the complete line of Cat machinery and engines. Whether the customers want to finance equipment, acquire working capital, improve cash flow, or protect their investment, Cat Financial understands the customers’ businesses and has the solutions to fit their needs. We offer quality service throughout the life cycle of equipment, including purchase, protection, management, and resell.
Cat Reman and Rebuild product offerings, as well as the range of repair options, help lower equipment ownership costs. Cat equipment is built to be rebuilt and reconditioned, and the Cat Certified machine Rebuild options can transform used machines and bring new life to assets with like-new performance at a fraction of the cost of a new machine. Cat Reman uses fewer resources and helps meet global customer demand while supporting a circular economy and building a more sustainable world.
Can you elaborate on how technologies like Cat Product Link and Vision Link?
At Caterpillar, we continually look for opportunities to broaden our product and service offerings, address customers’ needs, and help them succeed in their businesses. Our technology solutions, combined with the unmatched support and experience of the Cat dealer network, help customers enhance their fleet efficiency and profitability.
Cat Product Link™, along with GPS connect, not only helps improve traceability and visibility but also enables the systems to observe, identify and understand different facets of heavy machinery operation without human intervention and improves the maintenance and operation of machines. Vision Link takes the guesswork out of fleet management by providing timely equipment data to make informed decisions that help lower costs, boost productivity, simplify maintenance, and improve job site safety. Cat® Grade with Assist for excavators uses machine position sensors and operator-defined depth and slope parameters to automate boom and stick movements for more accurate cuts with less effort to help increase operator efficiency.
Cookie Consent
We use cookies to personalize your experience. By continuing to visit this website you agree to our Terms & Conditions, Privacy Policy and Cookie Policy.