Overcoming deficiencies of epoxy-coated rebar in concrete
By Staff Report | August 21, 2024 6:09 pm SHARE
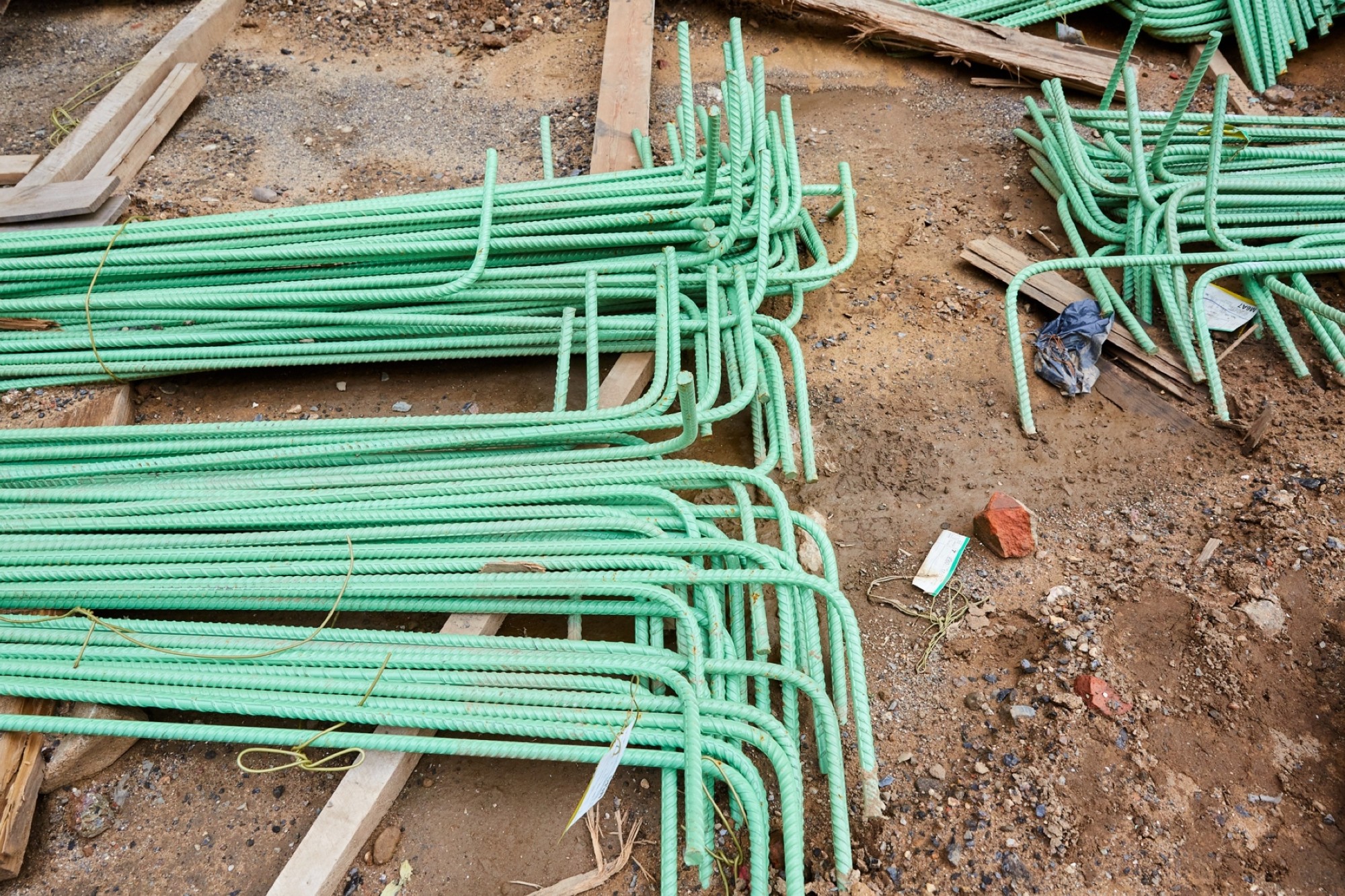
Rust threatens the long-term durability of concrete. Epoxy-coated rebar helps, but engineers must look into further options for good protection.
The most widely used construction material in the world is concrete. Although incredibly robust, its main susceptibility is rust. This is more common on older structures and can also damage new concrete in hot, humid seaside climates or areas that rely heavily on deicing salts. As a result, rows upon rows of green epoxy-coated rebar are frequently placed at construction sites to provide additional protection. However, engineers and contractors must recognise that this is not a cure-all for their corrosion concerns, and they must be aware of alternate techniques for overcoming the limitations of epoxy-coated rebar.
Epoxy coating deficiencies
If the epoxy coating on the rebar remained intact, it would provide superior protection by forming a thick barrier to corrosives. Unfortunately, coating degradation is far too common. As epoxy-coated rebars leave the paint line and are packaged for shipment to a jobsite, their most vulnerable stage begins. Cortec® CEO Boris Miksic stated that, “When coated rebars are transported, bent, welded, and installed, there is a great probability that the coating will be physically damaged. The damaged areas will become small anodes coupled to large coated areas becomes cathodes, causing pitting failures.” The question now is how to discover a backup technique that prevents corrosion at these spots.
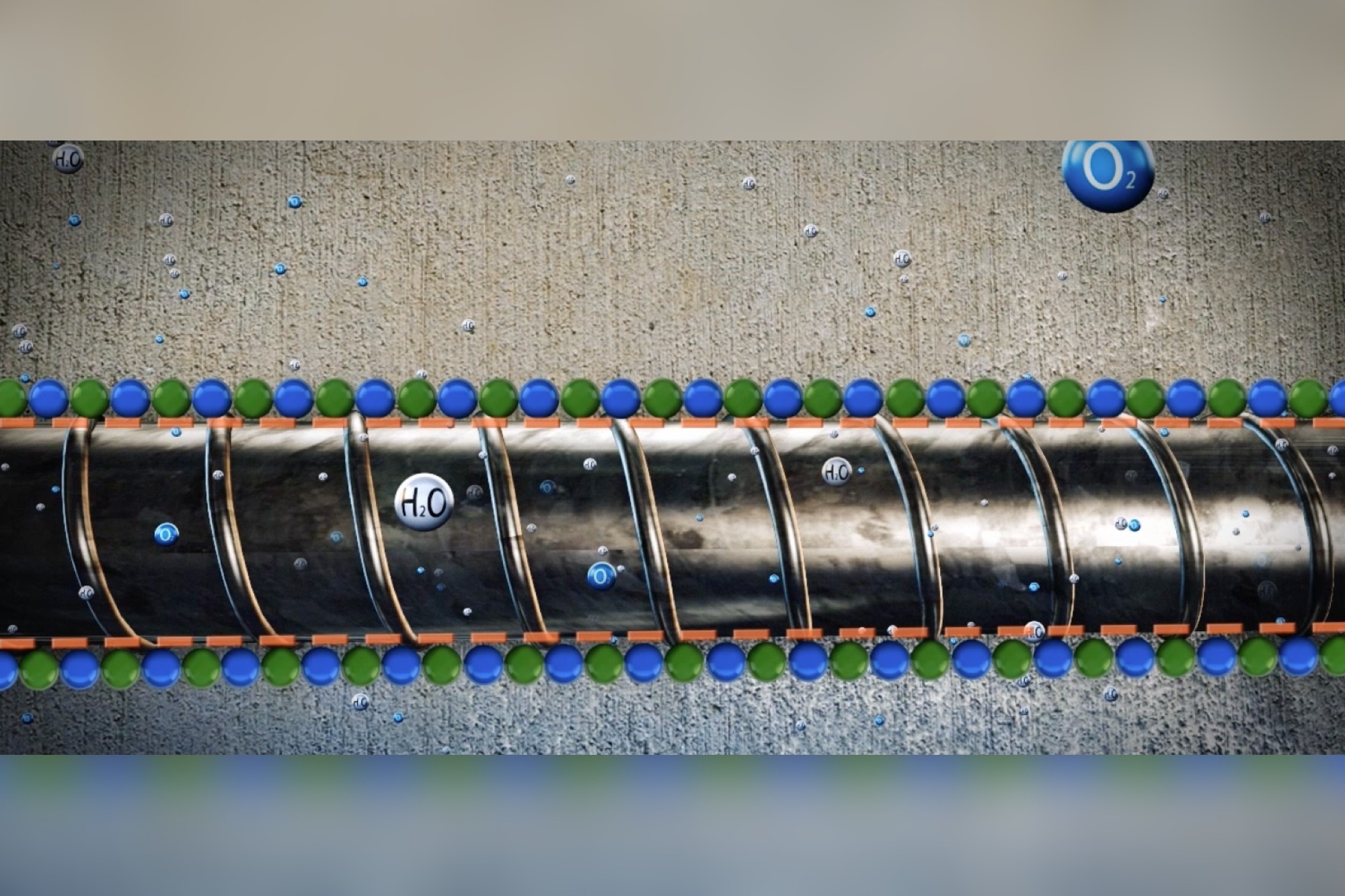
A molecular protective layer
Migrating Corrosion Inhibitors (MCI®) are an innovative, adaptable, and cost-effective solution. When used as an additive or surface treatment, MCI® chemistry works its way through concrete pores, forming a protective molecular layer on the surfaces of metal reinforcement due to ionic attraction. As a result, it can preserve a totally uncoated rebar or molecularly fill in broken parts of an epoxy-coated rebar where the metal is visible. MCI® is categorised as a “mixed” inhibitor since it affects both the anodic and cathodic components of the corrosion cell. MCI® can double or quadruple the delay to corrosion commencement while drastically reducing corrosion rates once initiated.
Comparing MCI® and Epoxy-Coated Rebar
MCI® admixtures, such as MCI®-2005 (a USDA Certified Biobased Product) or MCI®-2005 NS, are simple to use when mixed into ready-mix concrete during construction. Specifying engineers can utilise service life prediction modelling to estimate and compare how much MCI® is likely to extend service life in different settings vs epoxy-coated rebar’s estimated performance. Differences can be large. In one Gulf Coast project, the MCI®-2005 service life projection outlasted the expected service life of epoxy-coated rebar, saving the project hundreds of thousands of dollars. Although MCI® can be used as a complete replacement for epoxy-coated rebar, those who want extra “insurance” and have the funds to do so can request MCI® alongside epoxy-coated rebar for backup protection in locations where the coating may have been destroyed.
What if the damage is already done?
Sometimes the contractor has already noticed degradation to the rebar coating, but it is too late to request an MCI® admixture for an ongoing project. Fortunately, builders can still add an MCI® surface applied corrosion inhibitor (SACI) once the building is built. MCI®-2020 has the highest concentration of MCI® of any SACI available on the market and can be sprayed or rolled over existing buildings. It flows through the concrete matrix by capillary absorption and then vapour diffusion, eventually moving as far as several inches into the concrete to reach and protect the embedded rebar.
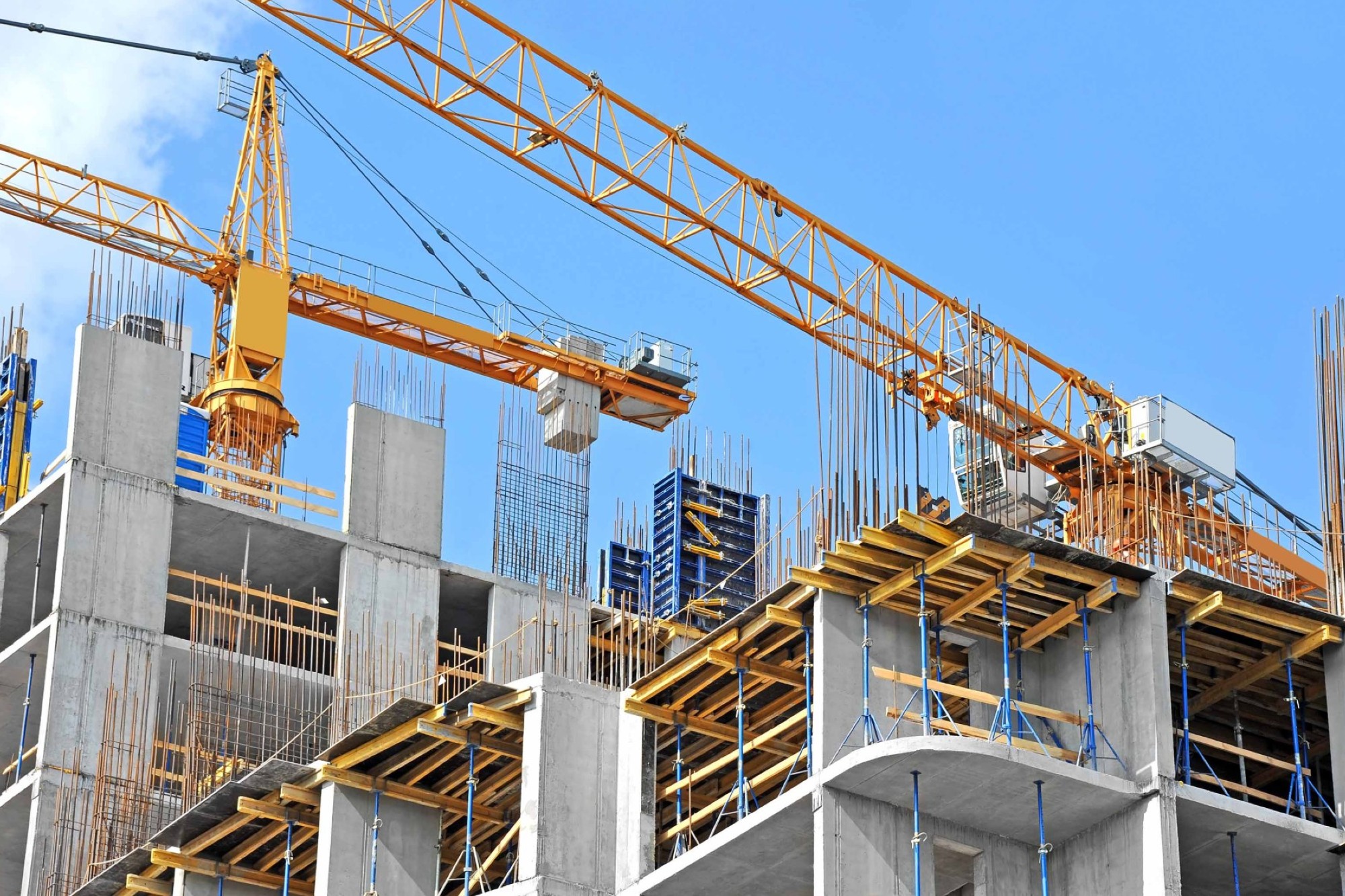
Start exploring the costs/benefits of MCI®
Epoxy-coated rebar may appear to be an appealing alternative until you consider the cost and the possibility of coating degradation. Because MCI® can increase service life at a substantially lower cost, engineers should carefully consider specifying MCI® as a complement or complete substitute for epoxy-coated steel.
Cookie Consent
We use cookies to personalize your experience. By continuing to visit this website you agree to our Terms & Conditions, Privacy Policy and Cookie Policy.