Modern structural engineers are confronted with diverse challenges, demanding innovative solutions and adaptability to navigate the complexities of contemporary construction projects.
From technological advancements to sustainability concerns, each challenge presents an opportunity for engineers to showcase their expertise and resilience in the face of evolving industry demands.
What are the modern-day challenges a structural engineer faces, and how does he overcome them?
Modern structural engineers face many challenges, each requiring unique solutions. One significant challenge is keeping pace with technological advancements. Engineers must continuously learn and leverage advanced modelling tools to stay ahead. Environmental sustainability is another critical area, addressed through green building practices and comprehensive life-cycle assessments to minimise the environmental impact of structures.
Resilience to natural disasters is essential, and engineers employ performance-based design techniques alongside advanced materials to enhance building durability. Staying compliant with evolving regulations demands a proactive approach to updating knowledge of codes and collaborating closely with regulatory bodies.
Utilising Building Information Modelling (BIM) and other project management tools facilitates effective project management, ensuring seamless coordination and execution. The rapid pace of urbanisation necessitates innovative solutions like vertical construction and modular methods to efficiently use space and resources.
Material and labour shortages are tackled by diversifying supply sources and integrating automation into construction processes. Maintaining health and safety standards involves implementing rigorous safety protocols and ergonomic design principles to protect workers and occupants.
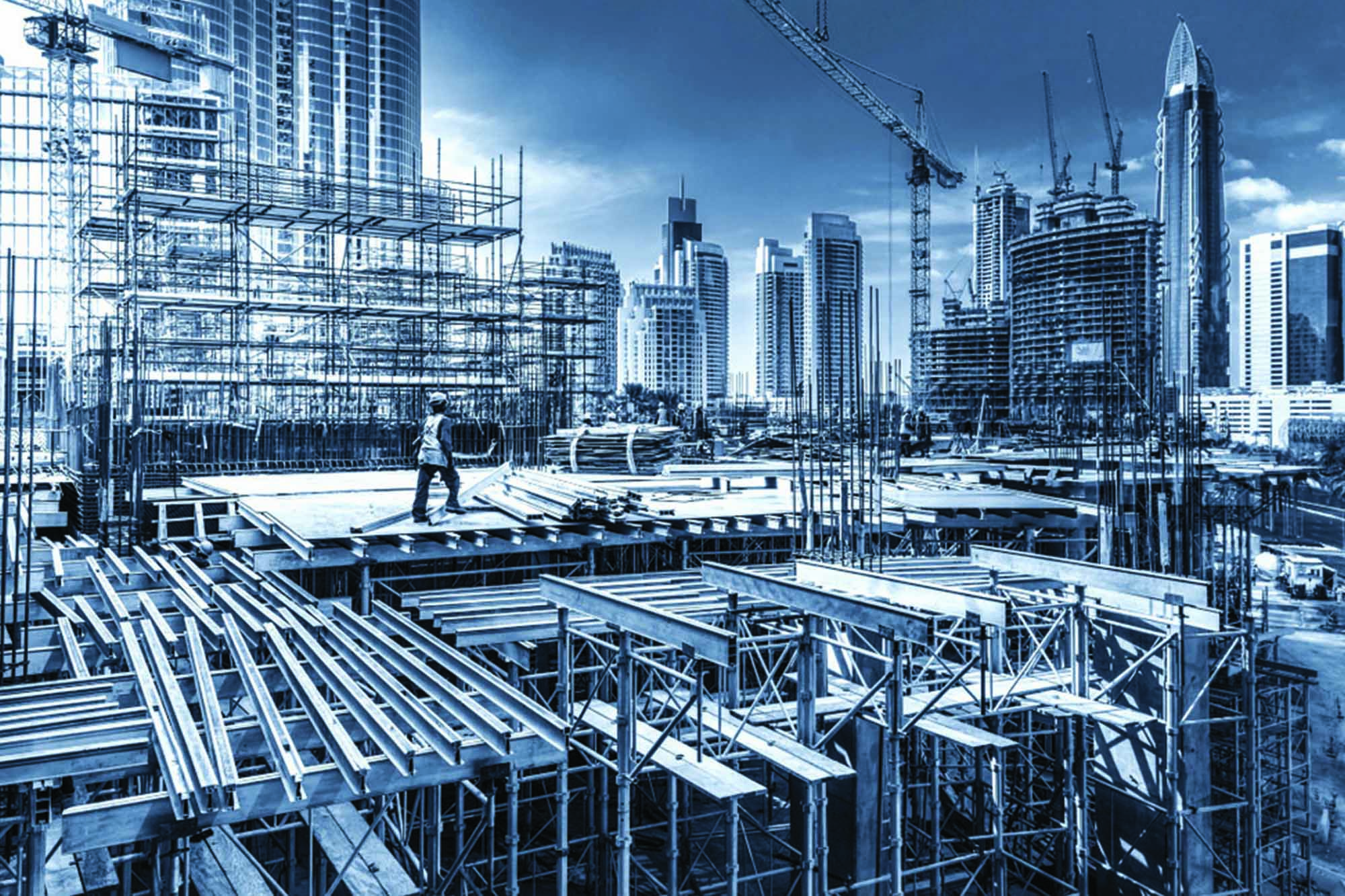
Cost management is achieved through value engineering and thorough cost-benefit analyses, ensuring projects remain financially viable. Lastly, integrating smart technology, such as the Internet of Things (IoT) and smart building systems, helps create more efficient and responsive structures, meeting the demands of modern infrastructure.
What are the benefits of using high-strength steel as reinforcement in RCC structures?
High-strength steel in RCC structures offers benefits like increased load-carrying capacity, reduced material usage, and thinner sections, leading to lighter structures. It enhances durability, reduces construction costs, and allows for greater architectural flexibility. Additionally, it improves seismic performance and overall structural resilience.
What are the advantages of cement replacement and mineral admixture in modern-day concrete? Cement replacement and mineral admixtures in modern-day concrete offer several advantages. First, they significantly enhance concrete’s compressive and tensile strength, making it more robust and capable of bearing greater loads. Additionally, these replacements improve concrete’s durability, providing better resistance to chemical attacks and reducing its permeability, extending the structures’ lifespan.
From a practical perspective, cement replacements and mineral admixtures enhance the workability of concrete, making it easier to handle and place, which is crucial for achieving a smooth construction process. They also help in thermal control by reducing the heat of hydration, thereby minimising the risk of thermal cracking in the concrete.
Sustainability is a major benefit, as these materials often involve using industrial by-products, which reduces the carbon footprint associated with cement production. This benefits the environment and tends to be cost-efficient by lowering material costs. Ultimately, incorporating these elements improves the overall performance and longevity of concrete structures, ensuring they remain safe, reliable, and economically viable over time.
What are the common durability issues associated with reinforced concrete structures, and how can they be mitigated through construction chemicals?
Reinforced concrete structures often face several durability issues, but construction chemicals can effectively mitigate these. One common issue is the corrosion of reinforcement, which can be addressed by applying corrosion inhibitors and protective coatings to the steel within the concrete, significantly extending the lifespan of the structure.
Cracking in concrete is another prevalent problem. This can be mitigated by using crack sealants and flexible waterproofing membranes, which help maintain the integrity of the concrete and prevent further damage. Alkali-silica reaction (ASR) is also a concern, but it can be controlled by incorporating ASR inhibitors and using low-alkali cement in the mix.
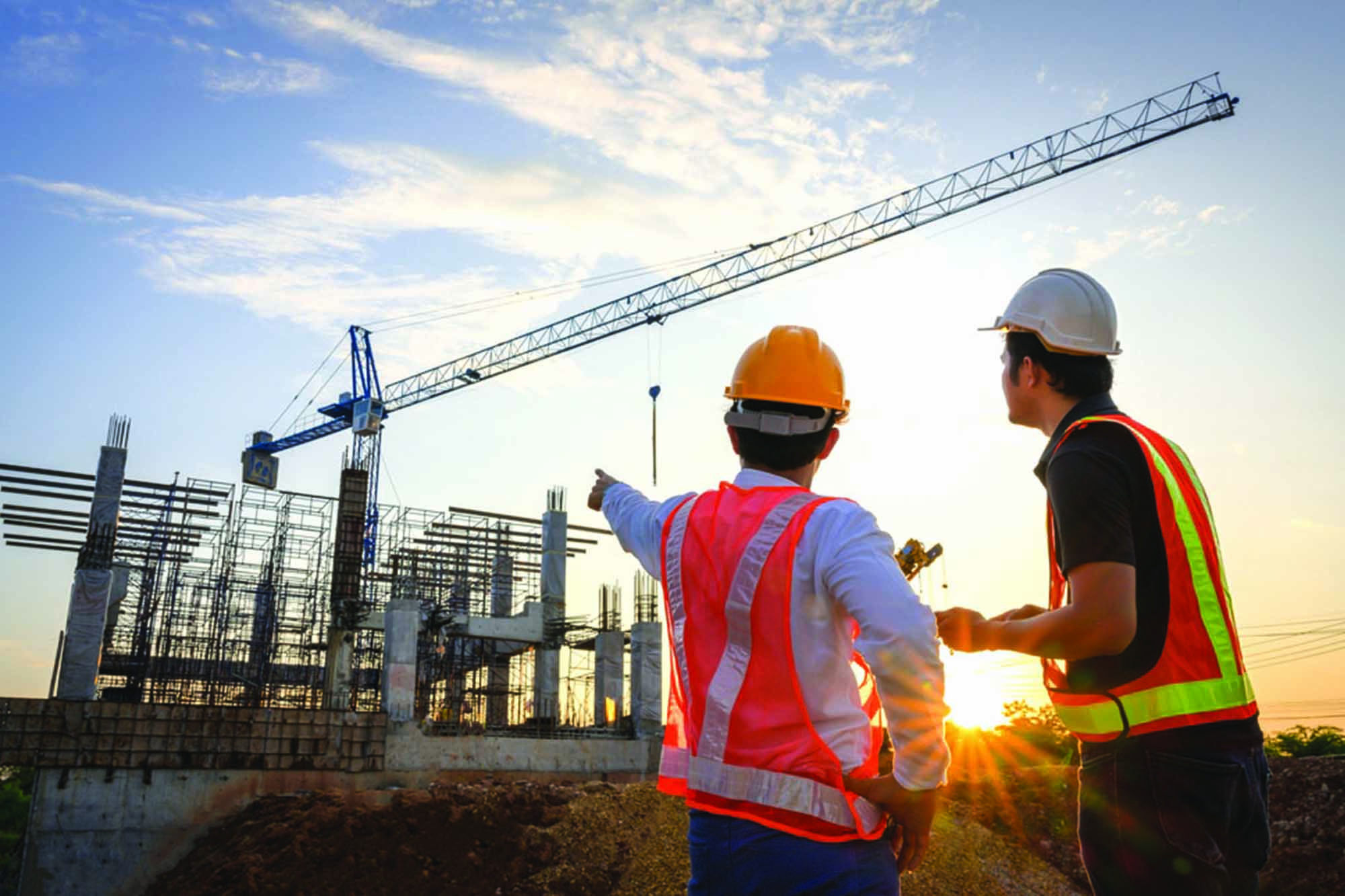
Freeze-thaw damage, which can cause serious deterioration in concrete, can be minimised by adding air-entraining agents to the concrete mix, improving its resistance to freezing and thawing cycles. Chemical-resistant coatings and sealants are highly effective in protecting against chemical attacks, providing a barrier against harmful substances.
Carbonation, which can lead to reinforcement corrosion, can be addressed by applying surface treatments and carbonation inhibitors to prevent carbon dioxide from penetrating the concrete. Lastly, moisture ingress can be mitigated using water repellents and damp-proofing agents, which help keep the concrete dry and reduce the risk of damage.
How do construction chemicals impact the cost and sustainability of a concrete structure?
Concrete admixtures are essential chemicals added to concrete mixes to improve workability, enhance strength, and provide resistance to adverse weather conditions. By optimising the concrete mix, these admixtures help engineers achieve greater efficiency and cost-effectiveness in construction projects. They improve sustainability by minimising material waste, enhancing resource efficiency, and lowering the carbon footprint through a reduced need for frequent reconstruction. Concrete admixtures enhance high-volume fly ash (HVFA) and GGBS mixes by improving workability, setting time, and strength. Water reducers, set retarders, and air-entraining agents ensure optimal performance, compensating for slower hydration rates. This allows a significant replacement of Portland cement, reducing CO₂ emissions and material costs. The use of industrial by-products like fly ash and GGBS further minimises environmental impact and waste.
How critical is using corrosion-inhibiting admixtures to increase the durability of RCC structures?
Using corrosion-inhibiting admixtures is critical for increasing the durability of RCC structures. These admixtures protect the reinforcement from corrosion, significantly extending the lifespan of the structure and reducing maintenance costs. They are essential for ensuring long-term structural integrity, especially in marine environments or areas with high chloride concentrations
What is the importance of barrier coats in enhancing the service life of concrete structures, specifically for infra projects?
Barrier coats play a crucial role in enhancing the service life of concrete structures, especially in infrastructure projects. These coatings provide essential protection against moisture, chemicals, and abrasion, effectively preventing damage to the concrete. This protective layer is vital for maintaining the structural integrity of the concrete, particularly by inhibiting the corrosion of reinforcement bars, which is a common cause of structural deterioration. Using barrier coats significantly extends the lifespan of concrete structures by preserving their condition over time. This reduces the required maintenance frequency and extent, ensuring that infrastructure remains safe and functional for longer periods. Also, reducing repair and maintenance needs translates to substantial cost savings. By minimising the expenses associated with ongoing upkeep and potential structural repairs, barrier coats offer an economical advantage for infrastructure projects, contributing to a more efficient allocation of resources and better long-term financial planning.
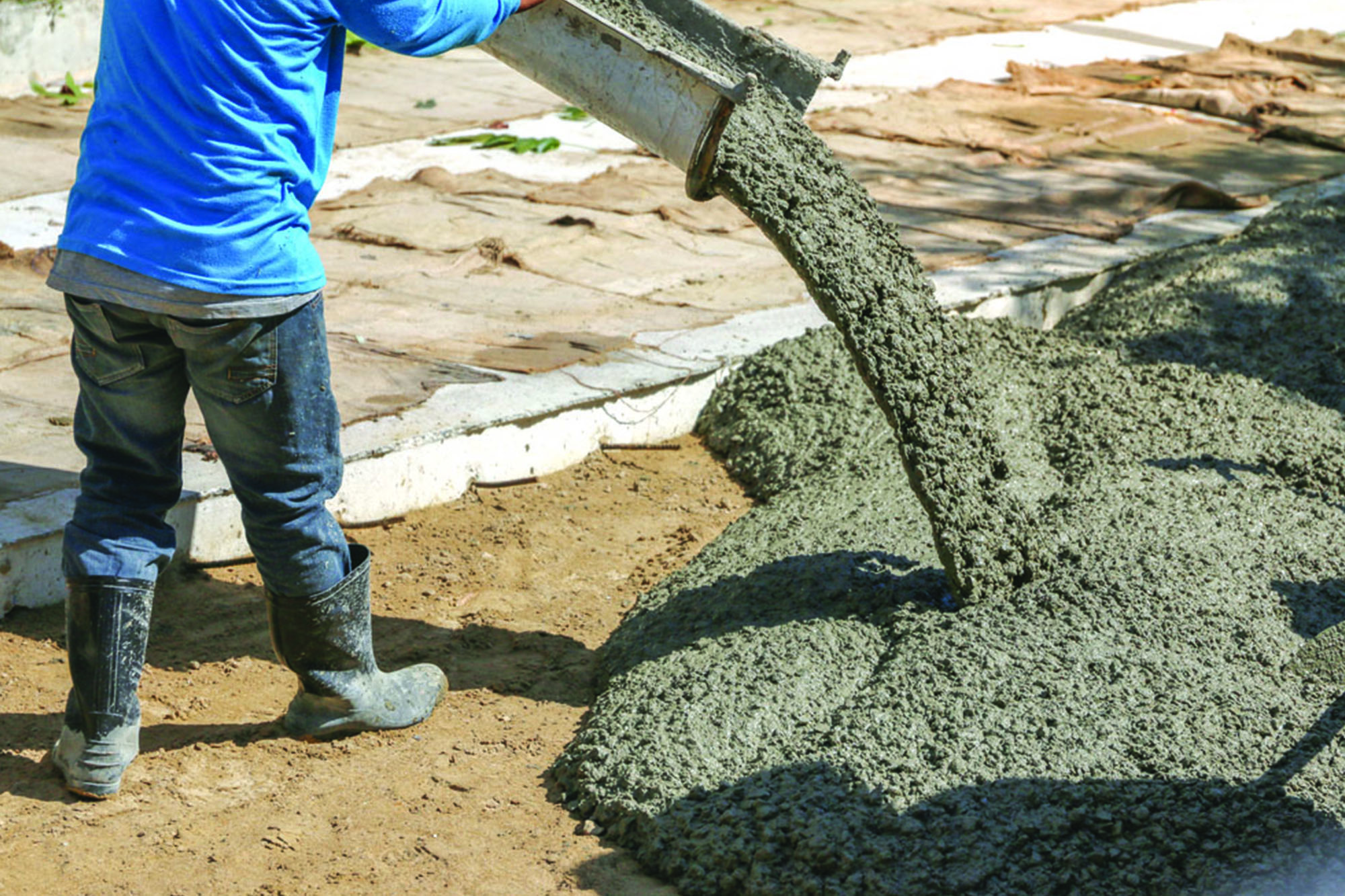
How do you see the field of structural engineering evolving in the next decade, and how are you preparing for these changes?
In the coming decade, we anticipate significant advancements in structural engineering, driven by several key factors. First, there will be a notable integration of digital technologies such as AI, machine learning, and advanced modelling tools. This integration will streamline processes, enhance accuracy, and allow for more efficient design solutions. There will be a heightened focus on sustainability and resilience, emphasising green and resilient design practices. This shift reflects the growing awareness of environmental concerns and the need for structures to withstand increasingly severe weather events. The adoption of advanced materials will play a pivotal role in shaping the future of structural engineering. Exploring innovative materials will lead to structures with enhanced performance, durability, and sustainability.
Collaborative platforms will gradually become more prevalent, facilitating knowledge-sharing and fostering industry insights. Engaging in such platforms will be essential for staying informed about emerging trends and best practices.
Eventually, continuous learning will be paramount for professionals in the field. Staying updated with emerging technologies and trends through ongoing training and education will ensure that we remain at the forefront of innovation and adapt to evolving industry standards. As a proactive professional, I prepare for these changes by staying informed, embracing new technologies, and investing in continuous education and skill development.
With fast-paced infrastructure growth and changing construction practices, how imperative is it to create a platform where industry experts join hands to share their knowledge and experience and promote the adoption of advanced construction practices?
Yes, it’s very important to join hands in sharing knowledge and experience through the collaborative efforts of industry professionals. It facilitates adopting advanced construction practices, ensuring projects are executed efficiently, sustainably, and resiliently. By exchanging insights and best practices, professionals can navigate challenges, promote innovation, and collectively drive the industry towards more effective and sustainable solutions, meeting the demands of modern infrastructure development.
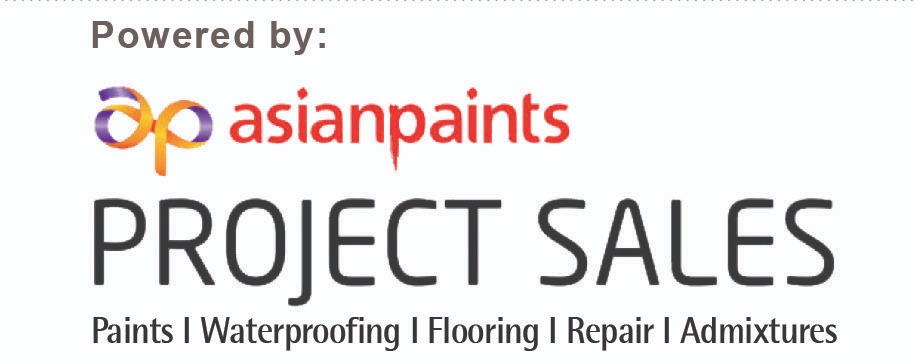
Cookie Consent
We use cookies to personalize your experience. By continuing to visit this website you agree to our Terms & Conditions, Privacy Policy and Cookie Policy.