Vögele MT 3000-2 Offset PowerFeeder: Paving the roads for the future
By Edit Team | February 19, 2021 5:50 pm SHARE
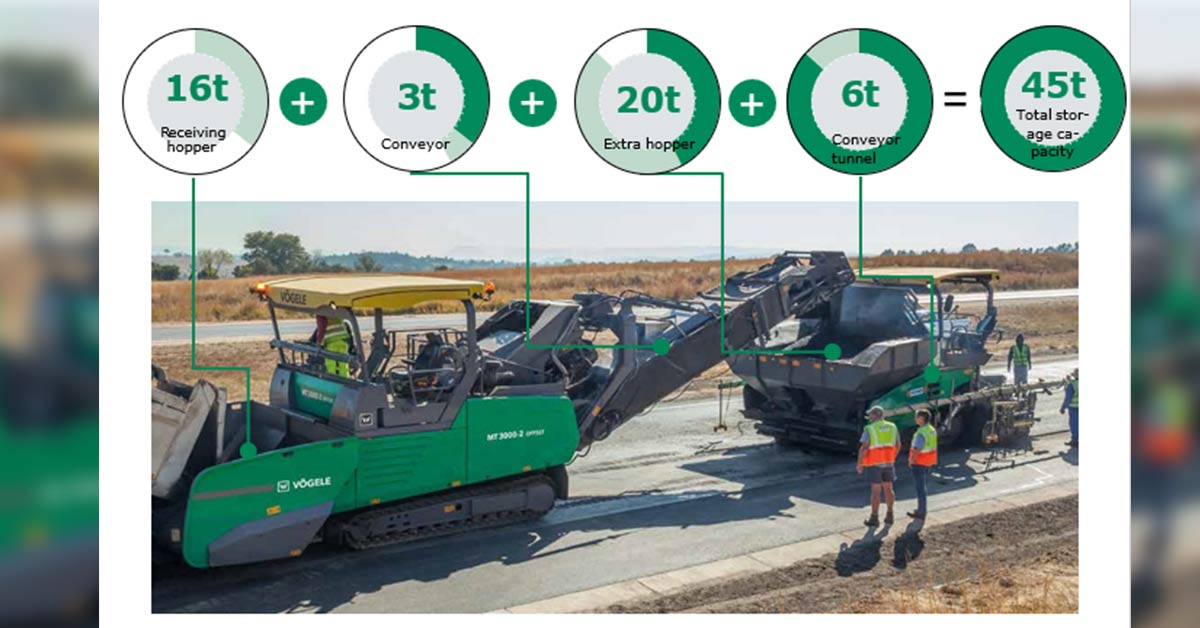
Vögele is the world market leader in Asphalt paving and offers a right paver for every application with various combinations of different paving widths and also offers state-of-the-art PowerFeeders especially for the large-scale job sites to offer reliable, uninterrupted transfer of mix to the pavers.
Bharatmala Pariyojana is a prestigious infrastructure project of the Indian government. The Vögele MT 3000-2 PowerFeeder along with the 13 m Super 2100-3 paver and Hamm compactors were deployed by one of our esteemed customers, Gawar Construction Ltd on NH 148B, the project in Haryana state.
After the successful completion of the project, Rakesh Gawar, MD, Gawar Construction Ltd, said, “Jerk free continuous paving is the key to the excellent surface finish and riding quality thanks to MT 3000-2 PowerFeeder. The difference can be definitely experienced as very less vibrations can be felt while riding on the paved road. Roads paved using power feeder have performed well in the roughness test as well. We have experienced the difference between conventional paving and the paving using the Vögele PowerFeeder and we look forward to use it in the future
projects as well.” Application of PowerFeeder Large roads, such as motorways or trunk roads, are the best applications for mobile feeders. The Power Feeder from Vögele is perfectly tailored for use when paving “hot to hot” with two pavers. The offset technology is also ideal for filling the spaces between safety barriers on motorways or long distance roads quickly and economically. The mobile feeder also demonstrates its strengths when it comes to surfacing footpaths or cycle paths. With its pivoting conveyor, it can travel on the main road and conveniently transfer mix to a small or compact paver on the cycle path. The Vögele PowerFeeder is also used in an InLine Pave train laying binder and surface courses “hot on hot” in a single pass. Its pivoting conveyor alternately supplies mix to the paver for binder course and the paver for surface course by way of a transfer module.
A non-stop, non-contacting transfer of mix achieved by the feeder is a decisive factor for perfect paving quality. With a peak conveying performance of 1,200 tones/ hour it can empty a full truck load in just 60 seconds. The on-board total storage capacity of 45 tones ensures uninterrupted paving, high quality matt finish and faster job completion. The excellent paving performance ensures cost saving to customers on account of fixed expenses and more revenues per day.
Highlights of the Vögele MT 3000-2 Offset PowerFeeder
• Uninterrupted paving thanks to a total storage capacity of 45t with a maximum conveying capacity of 1,200t/h.
• Non-contacting material transfer makes for maximum pavement quality. • Homogenized material in the receiving hopper of the material feeder due to conical augers.
• Wide range of applications thanks to the pivoting and inclining conveyor.
• Reliable material transfer based on automatic distance control and anti-collision protection.
• Optimum overview and safety thanks to the convenient and practical ErgoPlus operating concept.
• Powerful Deutz Engine with 142 kW at 2,000 rpm with ECO mode 139 kW at 1,800 rpm.
• 55 degrees conveyor pivoting angle with infrared heating panel.
• Backlit operating console.
New Generation of material feeders from Vögele
To increase the user-friendly nature and efficiency of the machines still further, Joseph Vögele AG has now comprehensively overhauled its former Dash-2 generation: the new MT 3000-3i Standard PowerFeeder and the MT 3000-3i Offset PowerFeeder with pivoting conveyor are equipped with the efficient and ergonomic Dash-3 machine concept. This includes, among other things, the ErgoPlus 3 intuitive operating concept, AutoSet Plus automatic functions and the PaveDock Assistant truck communication system.
Vögele has also optimized the material handling concept: the new design of receiving hopper, the improved conveyor belt control and the effective belt heating system allow material to be unloaded and conveyed rapidly without loss – whilst simultaneously reducing wear. Maintenance and transport have likewise been simplified: users can now reach setting and cleaning points even more conveniently. The angle of inclination and the receiving hopper have also been optimized for transport on a low-loader.
For more information, visit:
www.wirtgen-group.com
Cookie Consent
We use cookies to personalize your experience. By continuing to visit this website you agree to our Terms & Conditions, Privacy Policy and Cookie Policy.