We have the technology to make asphalt plants with alternate fuel
By Admin | October 31, 2022 2:50 pm SHARE
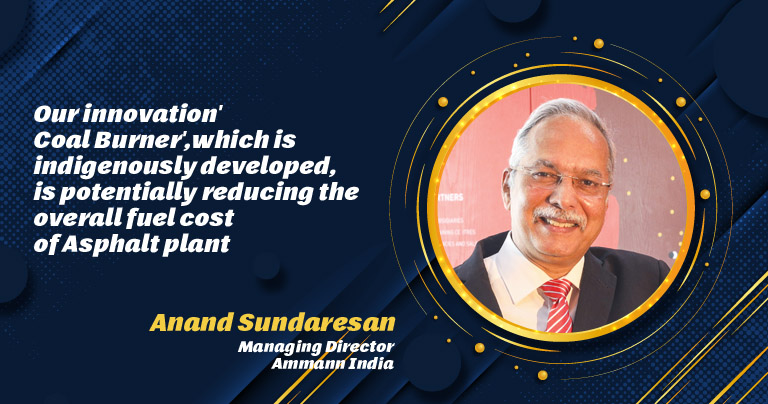
Along with the growing emphasis on batching asphalt plants, we see a transition in the asphalt equipment business, with manufacturers and customers moving toward lower fuel costs and using recycled materials, says Anand Sundaresan, Managing Director of Ammann India.
Technology trends in Asphalt batching plants
Ammann has been the pioneer in manufacturing asphalt plants for over 150 years. The market focused on continuous plants and the drum mix plant in the early years. But the industry is changing now. Even though the government has made it mandatory to have the batch type of asphalt plants, which gives the best advantage for gradation and mixing of material precisely to provide a good quality of Asphalt. Another critical area where we see changes is reducing fuel costs an recycling materials. A lot of technological development is taking place rapidly.
We have made our mark in India by introducing technology that can use up to 60 percent of recycled material. Moreover, for countries like Europe and others, we have technology that can use 100 percent recycled material, which proves that Ammann is technologically well advanced.
Unique innovation exhibited at INTERMAT 2022
We have many new models we desire to display here, but the only one we have shown this time is the Coal Burner. This innovation was kept on hold as it needed a good quality of coal, which is hardly available in India. Coal quality is critical, as we know that customers using coal burners are importing coal from Indonesia, Australia and other places. The most significant advantage of using a coal burner is that the fuel cost is reduced. You know, it will be practically 50 percent of the price if they use diesel, LDO or any other fuel. So, if the customers choose this coal burner in one project, they will save huge money on the plant operating cost.
Rapid road making
We produce a variety of equipment, most of which is used on roads and highways, including asphalt plants that produce Asphalt for road construction. With that, we have the entire range of wet and dry mix plants; pavers to pave the way; soil, tandem rollers, and PTR right from earth compaction to asphalt. In the secondary sector, we have ancillary equipment like bitumen sprayers, chip spreaders, and entire range of road-making machinery. We have a whole range of equipment, from very small to extensive equipment, which can produce up to about 260
tonnes of Asphalt mix per hour.
Available capacity of Asphalt batching plants
We focus on all the aspects of road building; national highway customers prefer to walk or ride on 180 or 260 TPH plants, but if the building is a minor job, like for PWD or something, then people even go for 120 tonnes. If it is even smaller than that, like municipal roads or projects, they go for continuous plants ranging from 60 to 120 tons per hour.
Going green to complement sustainability
Though going green is not so popular in India, we already have the technology to use gas and other fossil fuels to manufacture our equipment. Our parent company in Europe is working more on this innovation in power consumption and green technology, which we will know soon.
Ammann is deeply entrenched in introducing more and more green fuel for our products, as taking care of Mother Nature is also our responsibility.
Outlook on the Indian asphalt plant market
India is a large country with a vast road network. From small roads to big roads and all the connections, there are more than 40 million kilometres of roads that we have to build. As a result, it leads to asphalt roads while the government plans concrete roads. But now, there have been a few stragglers for various reasons. At one point, we discovered that asphalt roads constituted at least 50–60 percent of all road construction. So, there is a promising future for these asphalt plants in India.
Cookie Consent
We use cookies to personalize your experience. By continuing to visit this website you agree to our Terms & Conditions, Privacy Policy and Cookie Policy.