Connecting India—a mammoth task
The new Samruddhi Expressway, also known as the Mumbai–Nagpur Expressway, is currently under construction and will connect the Indian cities of Mumbai and Nagpur over 701 km. This expressway will link India’s largest container port, JNPT in Mumbai, to MIHAN in Nagpur, simplifying import and export activities throughout the country. Furthermore, interconnecting highways and feeder roads are being built to connect all major cities and tourist attractions along this route.
The Samruddhi Expressway Mahamarg project consisted of 16 packages and was awarded to 13 companies: Megha Engineering & Infrastructures (Pkgs 1 & 9), Afcons Infrastructure (Pkgs 2 & 14), NCC (Pkg 3), PNC Infratech (Pkg 4), Sadbhav Engineering (Pkg 5), Apco Infratech (Pkg 6), Reliance Infrastructure (Pkg 7), Iron Triangle (Pkg 8), Larsen & Toubro (Pkg 8), Gayatri Projects (Pkg 11), Dilip Buildcon (Pkg 12), GVPR Engineers (Pkg 13), and Navayuga Engineering Company (Pkg-15&16).
Wirtgen slip form pavers show their potential all the way.
With a speed limit of 150 km/h, the expressway is the fastest in India, reducing the travel time between Mumbai and Nagpur from 16 to 8 hours. This calls for maximum concrete paving performance in terms of output and quality to ensure the drivers’ comfort and safety on their journey. Along 701 km, 16 Wirtgen slip-form pavers SP 1600 were in operation to lay the concrete surface. Concrete is ideal for a gigantic project like this: it is cost-effective, extremely durable, and requires very little maintenance. Over a working width of 15 m, pavement quality concrete (PQC) at a depth of 310 mm was used. The proper reinforcement could be managed by an automatic dowel bar inserter and three longitudinal tie bar inserters. These ensure that the cracks, which are invariably produced as a result of stresses and temperature fluctuations, are diverted into the concrete pavement in a controlled manner.
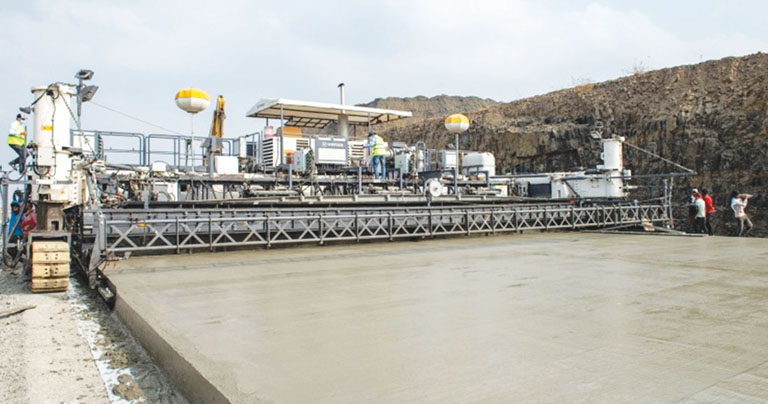
Highlights of the Wirtgen slip-form paver SP 1600:
- Working width of up to 16 metres (special paving heights and widths up to 18.75 m are available on request.)
- Cost-effectively pave concrete surfaces for traffic areas, roadways, industrial areas, or surfaces at airports, such as runways or taxiways.
- Unparalleled concrete paving performance
- Long-term reliability
- Ergonomically designed, walkthrough operator’s platform for non-tiring, productive work
- High-powered, fuel-efficient diesel engine for concrete paving in the optimum performance and torque ranges
- Spreading the plough for even distribution of the freshly delivered concrete in front of the inset paving mould
- Electrically driven vibrators for reliable concrete compaction
- Automated insertion of longitudinal joint tie bars to prevent the slabs from drifting apart
- Inset paving mould suitable for mounting between the track units underneath the machine.
- Pivoting legs allow for full adjustment of the track units to the conditions prevailing on site.
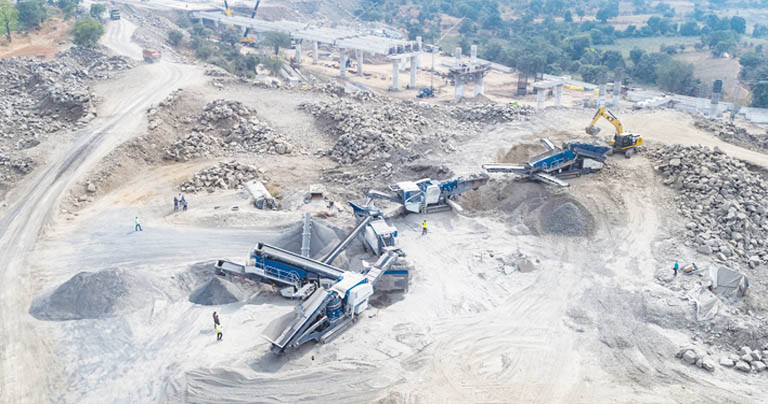
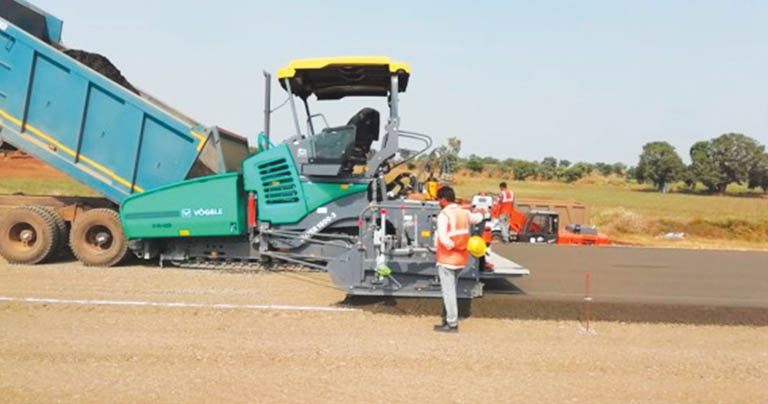
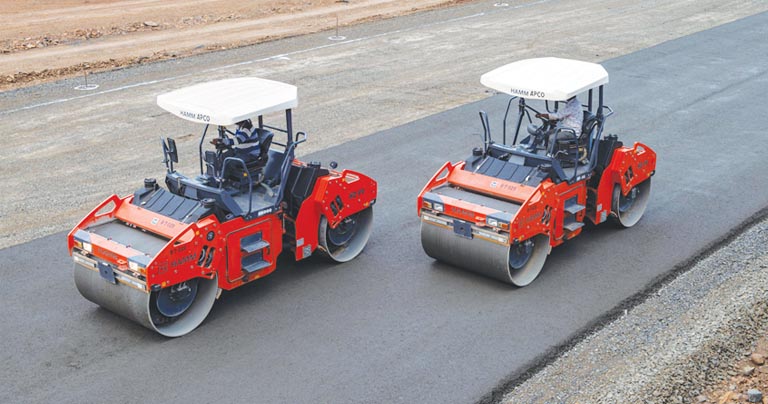
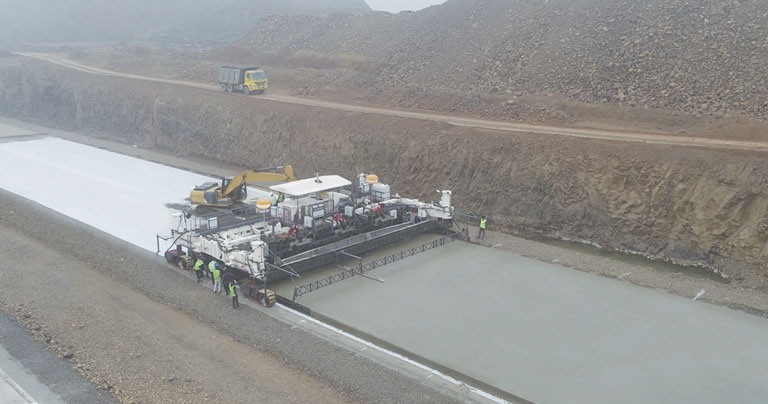
Wirtgen Group service impresses on site
When it comes to the experience and day-to-day handling of their equipment, there is unanimity: Everyone is more than happy with the performance of the machines. “They are doing very well, and we are delighted with their services,” said Neeraj Sharma, quality in-charge (Sr. Manager) at Apco Infratech Pvt. Ltd., responsible for package 5. “They are good in technology, quality, and output.” Wirtgen India, the local subsidiary of the Wirtgen Group, is always at hand should there be any customer requirements. “They always care for our needs and challenges.” From time to time, they guide our team and help. “Whenever challenges arise, they are always there.”
“The machines are doing very well, and we are extremely satisfied with their services.” Neeraj Sharma, Quality Incharge (Sr. Manager), Apco Infratech Pvt. Ltd.
Cookie Consent
We use cookies to personalize your experience. By continuing to visit this website you agree to our Terms & Conditions, Privacy Policy and Cookie Policy.