Layher’s Allround Scaffolding sets the standard for modular scaffolds, offering unparalleled versatility, safety, and efficiency across industries worldwide. With continuous innovation and a dedication to customer satisfaction, Layher remains the preferred choice for demanding scaffolding applications.
Layher produces high-quality scaffolding systems. Layher has a worldwide presence with more than 43 sales subsidiaries. Industries like Construction, chemical plants, power plants, shipyards, and offshore are using the products. Nowadays, for demanding and complex scaffolding applications – i.e. wherever conventional scaffolding technology falls short of optimal, thus cost-effective use, Layher Allround Scaffolding convincingly comes in with an unmatched range of advantages: unbeatably fast assembly, persuasive economic arguments, and an extensive range of series-produced accessories.
The proven combination of positive and non-positive connections in a rapid and bolt-free system technology with AutoLock function facilitates connections that are automatically right-angled, obtuse-angled, and acute-angled – and ensures built-in safety simultaneously. Layher Allround Scaffolding has now become synonymous with modular scaffolding on the market.
Since its launch in 1974, this original system has been continuously developed and offers an impressive variety of uses: on any construction site, in industry, chemical plants, power stations, shipyards, and for events. It can be used as scaffolding for working, protection, façade work or support, internal or birdcage scaffolding, or rolling towers.
Even with very difficult layouts, architectural styles, and heightened safety requirements, Allround Scaffolding is the faster, safer, and more economical solution.
More Possibilities – Layher Products and Services
Layher’s present product characteristics and services help customers achieve long-term success and increase the profitability of their companies. The Layher Allround Scaffolding has been established as a synonym for modular scaffolds on the market. It offers unsurpassed versatility for use in construction sites, the chemical industry, power plants, aircraft, shipyards, the event sector, theatres, and arenas.
Allround scaffolding uses a simple, unique, and bolt-free connection technology. Sliding the wedge head over the rosette and inserting the wedge into the opening immediately secures the component. There is still sufficient play to secure the other end of the ledger. A hammer blow to the wedge transforms the loose connection into a strong, strong, structurally rigid one. The face of the wedge head is now precisely positioned against the standard. Connections in quick-to-assemble and spanner-less scaffolding systems make a unique combination: providing structural strength immediately on assembly and subsequent ultimate force transmission while offering a choice of automatically right–angled or splayed connections with universal safety right from the start.
To transfer pulling force, every frame is secured by locking pins or bolts to each other. This way, the tower can be assembled on the ground and placed by crane.
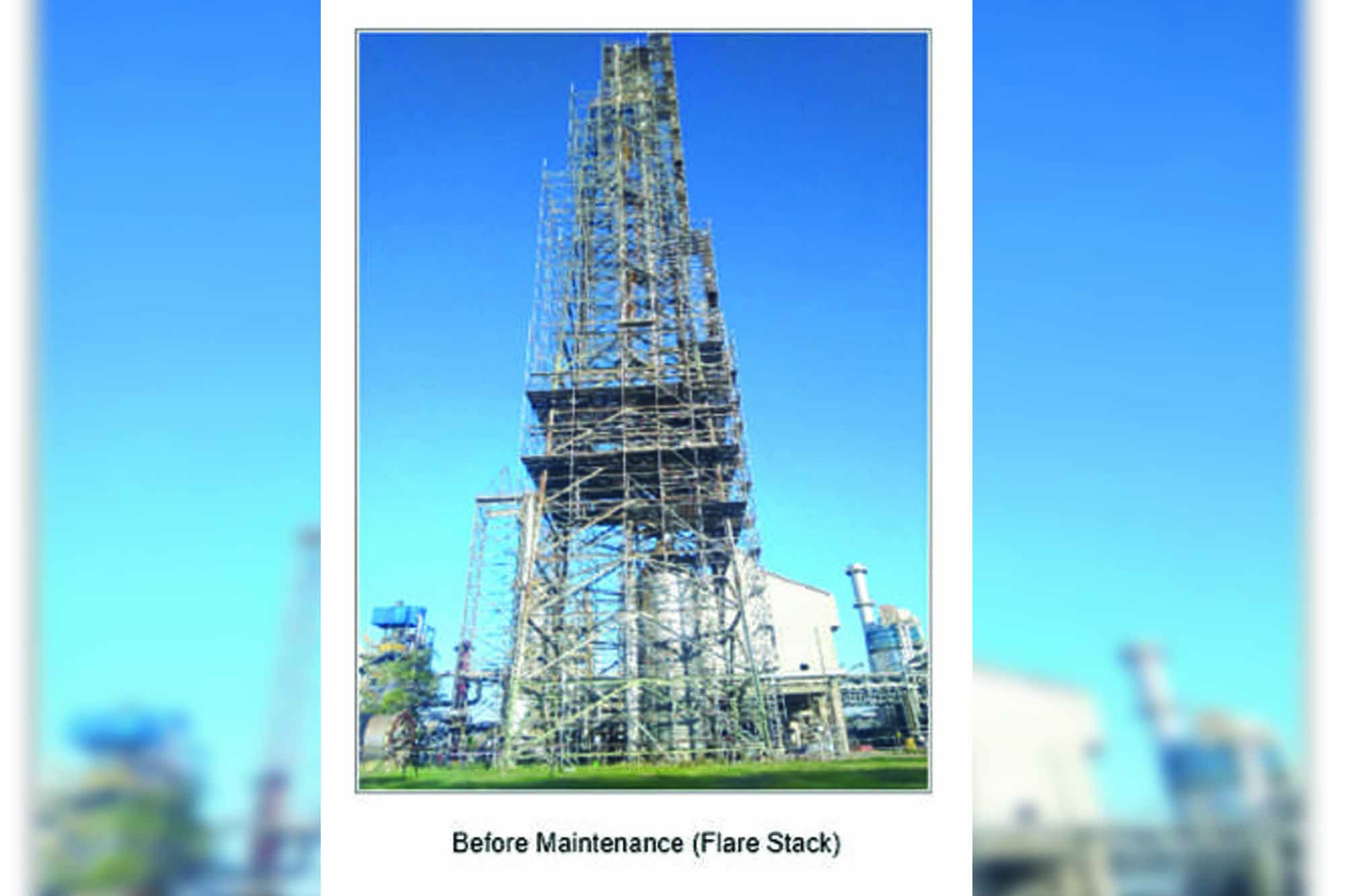
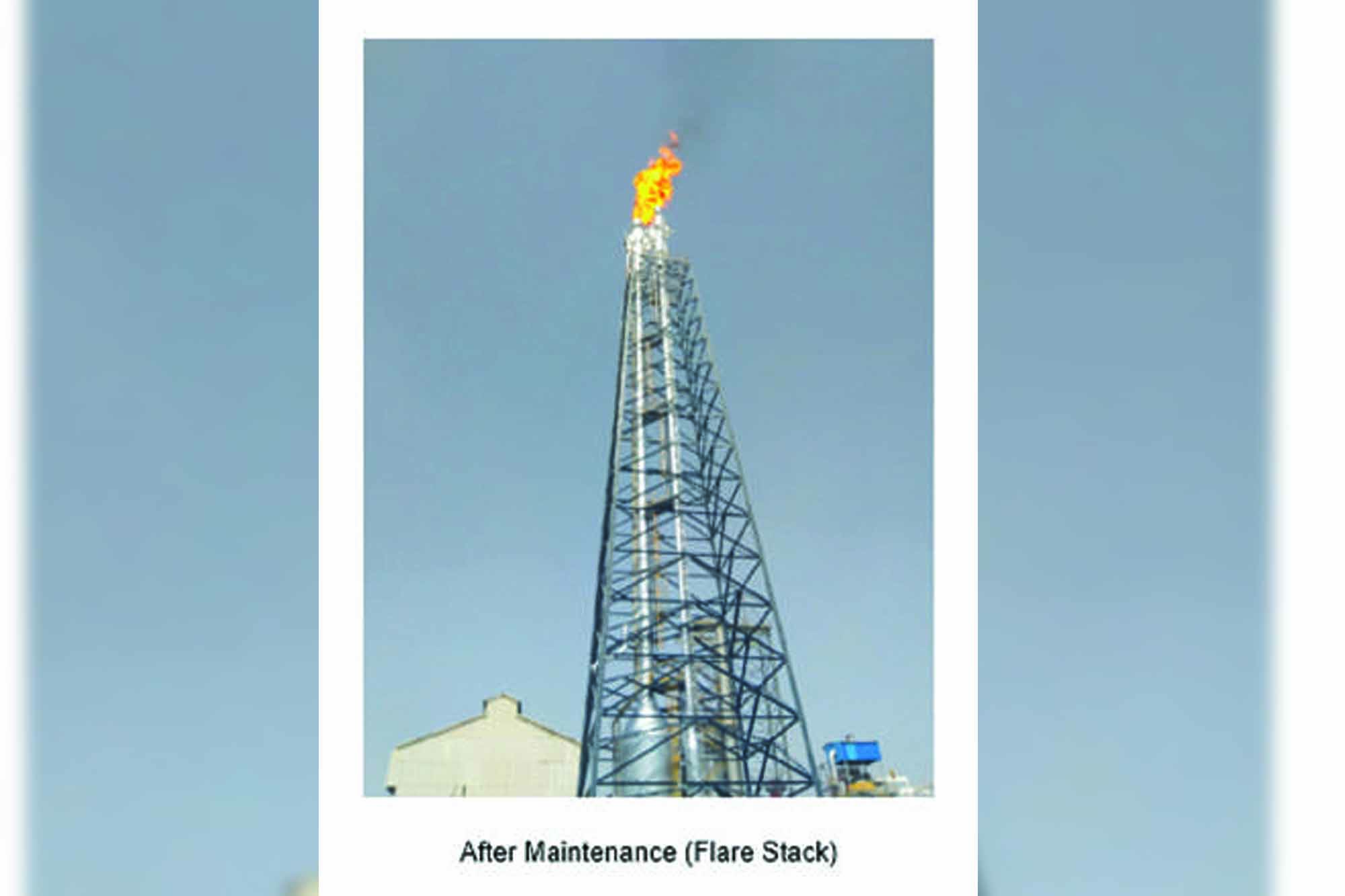
Application of Allround for Maintenance of Flair Stake in Chemical Plant
A gas flare, alternatively known as a flare stack, is a gas combustion device used in industrial plants such as petroleum refineries, chemical plants, and natural gas processing plants, as well as at oil or gas production sites having oil wells, gas wells, offshore oil and gas rigs, and landfills. In industrial plants, flare stacks are primarily used to burn off flammable gas released by pressure relief valves during unplanned over-pressuring plant equipment.
Gas flaring at many oil and gas production sites protects against the dangers of overpressuring industrial plant equipment. An example of the consequences of failing to flare escaping gas was evident in the Bhopal disaster when a flare tower was broken and couldn’t flare escaping Methyl isocyanate gas (the gas had been in an overpressured tank and released by a Safety valve), which resulted in its release into the surrounding area.
Multiple structures of different sizes operated by Chemicals and Fertilizers are currently being refurbished, and corrosion prevention experts have to treat the entire structure from time to time. A modular scaffolding system assures safe access to all locations of the main building. Using an all-around scaffold is the only possibility of completing maintenance on time and safely as required.
The Chemical Plant requires painting of the complete flare stack and associated derrick structure on an apply–supply basis (services along with material Supply). This includes complete scaffolding erection and dismantling (M/s Layher providing all necessary material) to execute the painting job of flare stack Ammonia and around the associated derrick structure. The basis of erection services is scaffolding material Supply.
Flare stack Riser of diameter 36 inches for connection between the Knock out Drum at the base and Flare seal at the top. The approximate height of the riser is 68 meters.
Painting specifications for painting and working procedure of scaffolding erection and dismantling as per Company standards. There shall be three levels of safety viz., full-body harness Safety belt, fall arrestor (one-on-one rope), and safety net. The rope should be M/s Karam with a load test certificate from the competent authority.
Shifting scaffolding material up to working height is to be done with tested rope and pulley, and care must be taken to ensure that no one is in the vicinity of the working area.
The advantage lies in the speed with which the system can automatically obtain the right angle, and variable angles can be achieved if required. This is done by fitting the ledgers in rosettes, each with four holes at right angles, with four larger holes (usually used for diagonal braces) facilitating variable angles. This means that the erectors can also make connections at any angle as the conditions on-site dictate. The Scaffolder can easily, thanks to the eight possible connections in every connector, make adaptions quickly and optimally for almost any application.
These advantages ensure the optimum conditions for effectively enclosing the Circular and rectangular structure with safe and minimal time required to construct the scaffolding. Allround Scaffolding was easily adapted to follow the contour shape of the structure without being difficult to access. The erectors didn’t need to create complex tube structures, saw off tubes all the time, repeat measuring of connections, or constantly align the upright elements. The wedge head provides an all-in-one simple yet stable connection, logical assembly sequence, and integral safety. Hot-dip galvanisation and certified quality ensure that all-around scaffolding’s top-quality products are extremely long-lived.
Several work levels and a lift going up 66 meters were required to be integrated into the scaffolding. The challenge set by this particular job was to follow as precisely as possible due to inclined angles. This was possible due to the extensive capability of parts Layher Allround can offer.
Due to the restriction of open space, access is only possible with an Aluminium deck with an integrated ladder. Access decks can be built into the scaffolding for internal access. These decks conform to the requirements of DIN EN 12811 and are available with a separate or integrated access ladder for internal access.
The stability of a structure shall be checked both with and without the wind loads, as there may be a reversal of the forces under wind besides a reduced factor of safety considered with the wind loads as per IS 875 (Part 3). Assembly, alteration, and dismantling of the Layher Allround Scaffolding involves a risk of falls. Perform scaffolding assembly work so that the risk of falls is avoided as far as possible and that the residual risk is minimised.
The top lift of the scaffold at the top of the structure called for Layher’s expertise. Following the increasingly safe scaffolding with proper access at all locations, Layher’s Technical Bureau designed a series of connections to the topmost existing structure—all-around standards that made them converge in tension-resistant form. The scaffolders then placed the structure on the highest point of the building using All-Around standards and applicable accessories.
Construction of Scaffolding to approach all required locations was a major challenge during the work due to the unsymmetrical structure, but it is easy when considering Allround Scaffolding Systems.Layher new Lightweight scaffolding is the result of a major, multi-year R& D project with a clearly defined objective: to make scaffolding easier, safer, and more cost-effective for customers.
Cookie Consent
We use cookies to personalize your experience. By continuing to visit this website you agree to our Terms & Conditions, Privacy Policy and Cookie Policy.