Epoxy mastic coatings, according to Prof. A S Khanna, Chairman of SSPC India, are the ideal option since, when used as a primer coating, they offer good adhesion to conventional paint coatings when applied to such surfaces.
Can you tell us more about the current need for industrial coating protection products? Industrial coating is a huge segment that involves industries including chemicals, refineries, fertiliser, petrochemical plants, power plants, and offshore structures. The coatings needed for the said structures/ facilities are for a life which varies from a few years to several years, ranging from 10 to 20 years. There is further classification in terms of internal and external surfaces. Coatings for external surfaces: This is a relatively well-understood area. The coatings are well defined in terms of low, moderate, and highly aggressive environments, also classified as C1, C2, C3, and C5 environments as per ISO classification. The coating combines a zinc-based primer – epoxy zincrich or inorganic zinc silicate with an intermediate epoxy coating and a top aliphatic polyurethane coating to protect it from UV and sunlight.
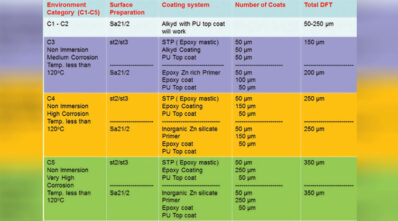
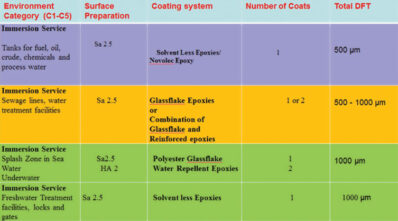
See in Table 1 below various coatings for the C3 to C5 environment, along with the coating thicknesses and several coats: Internal coatings are complicated and vary depending on the storage material. Therefore, an epoxy coating liner with a thickness of 500 to 1000 microns will be adequate. For harsh fluids, the epoxy is further modified by the addition of glass flakes or fibre. A fast-curing coating like polyester glass flake is preferable for harsh environments like corrosion and erosion and splash zone applications. See table 2 for more information:
Acid/Alkali Resistant Coatings
The third most severe environment is acidic, also known as acid rain, in which SO2 and CO2 combine to create a very harsh environment. For this, we recently developed a solid coating called Nanomodified Acid Resistant Coating, which can withstand acids and alkalis ranging from pH 1 to 14 as well as any solvent. This coating is also appropriate for ship and submarine battery rooms, wastewater treatment plants, and pickling plants. The TDS of this system is shown in table 3 below and is available upon request.
What is cutting-edge technology currently being incorporated into paints and coatings to improve adhesion and dependability?
Paint coating adhesion can be improved primarily by creating a clean blasted surface with a suitable anchor profile. All standard organic paints adhere well to blast-cleaned surfaces. However, for partially cleaned surfaces which can be cleaned by blasting, paint systems that create sufficient wetting on the partially cleaned surface are required. Epoxy mastic coatings are the best choice because they provide good adhesion to standard paint coatings when applied to such surfaces when used as a primer coating.
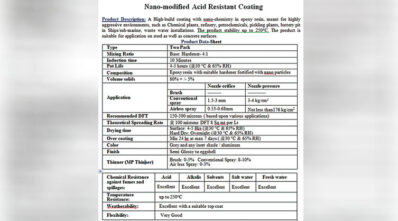
,Another example is thin metal sample sheets with a thickness of 1.5-2 mm that cannot be blast cleaned. They require the application of a conversion coating, such as phosphating, which roughens the surface to improve adherence. The majority of coil coatings require phosphating before the primary coating is applied. Adherence is also related to the cleanliness of the surface after blasting. Dust, chlorides or moisture, if retained during primer application, can disband the coating. Hence, the blasted surface is kept covered after blasting till the painting is not done.
Can you highlight the available tools to improve the paint coating’s qualities for industrial applications?
Large industrial paint coating applications are made through spray coatings, which are available in two different types: • Air Spray Techniques, and • Airless Spray Techniques. Air spray is a technique used for high-gloss paint applications. This technique uses low-volume solid paint systems for consumer durables and car bodies where a high-class surface finish or gloss is the primary requirement. Here, the paint is exposed to high-pressure gas at a pressure of 20–60 psi to break the paint into liquid drops and force it onto the substrate. This method has a lower efficiency of around 30-35 per cent, but the air-spray guns are relatively inexpensive.
The Airless Spray Technique gives an extremely corrosion-resistant coating with a lower surface finish and gloss. It typically employs high-volume solid paint, a solvent-free paint system which produces a relatively thick coating of 500 to 2000 microns. In this case, a hydraulic method generates a high pressure of about 2000 psi to create liquid droplet forces on a substrate and achieve a bond strength of 4 to 20 MPa. The efficiency is also relatively high, ranging between 50 and 55 per cent.
In addition, there is another industrial application called Powder coating, done by the electrostatic spray method. Here the powders are electrostatically charged in a particular gun which makes the charged paint particles hit on the oppositely charged substrate, followed by heating. The coatings obtained are highly flexible and have long durability. The process has an efficiency of about 75 per cent or more.
What effects and advantages come from including changed waterproofing components into paints and coatings?
Waterproofing is an essential requirement for painted components, equipment, and structures. It is always advisable to apply a coating after ensuring no components are leaking. Take, first, the painting of the rooftop. There is no point in coating a leaking roof. Thus, the first step to painting an old rooftop is to make it leak-proof. We provide a 3-layer roof coating technology. It is a nano-modified compound which is applied first as an absorbent coat, followed by filling all cracks using a paste made with this compound and white cement on the roof and also repairing the parapet of the roof, which causes many leaks. This is followed by a 1 mm coat of this compound mixed with white cement. The surface is ready for post-paint application, Coba or tile fitting, or using an energy-saving rooftop coating. We usually do an energy-saving solar heat-reflective coating on its surface. A combo offer of waterproofing and solar heat-reflective coating systems is available with us.
What are the newest and most popular trends in this market?
Popular paints and coatings trending in the market are Functional Coatings, Smart Coatings, Nano-modified Coatings, Energy-saving Coatings, Sustainable Coatings, and Waterborne Coatings.
(SSPC India is known for giving level 1 and level 2 training on paint coating inspection and quality control and many other training programs on this subject for the last 20 years. Prof. Khanna now runs a fully NABL accredited lab called SECC LAB at Vikhroli West.)
Cookie Consent
We use cookies to personalize your experience. By continuing to visit this website you agree to our Terms & Conditions, Privacy Policy and Cookie Policy.